Theory of operation of the autotuning algorithm – Yaskawa YTerm User Manual
Page 50
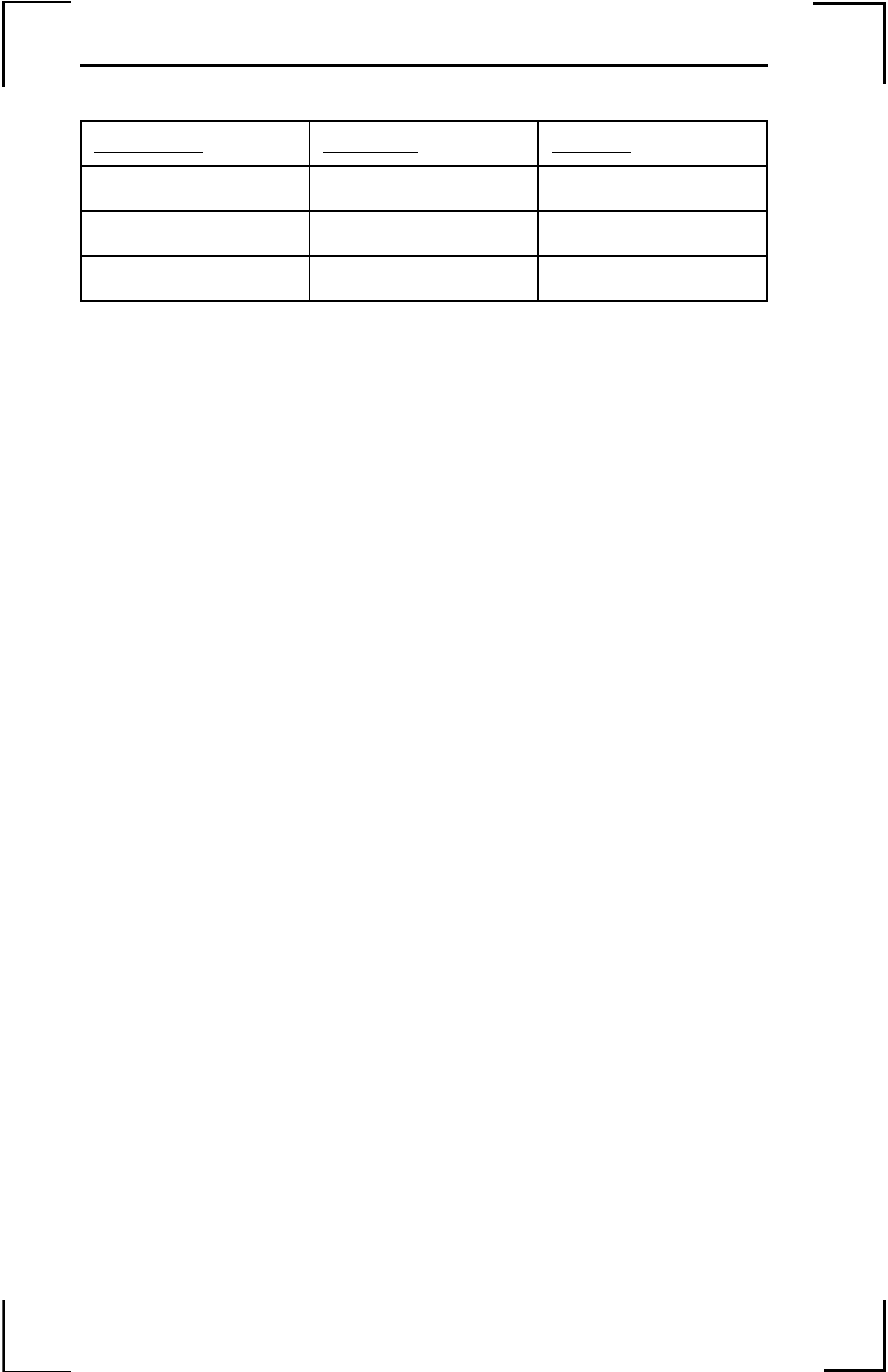
44
YTerm Software Manual
Theory of Operation of the Autotuning Algorithm
The motor is jogged in a positive direction at 3.75 R.P.M. while 5000 torque
reference values are recorded and averaged. The purpose of this is to get an
idea of the torque required to overcome friction. This is done with minimal
gains settings of KD=10, KP=1, and KI=0.
The PID loop is shut off (KD=0, KP=0, and KI=0) and a voltage of 1.5 volts
is applied to the motor command output for 100 msec. The motor position is
recorded before and after this voltage is applied to determinate how far the
motor traveled in 100 msec. The farther it moved, the lower the inertia
mismatch.
Calculations are made to determinate KD, KP, and KI based on the inertia
and selected rigidity level.
The motor is moved backward and forward (approximately 11 degrees for an
1:1 gear ratio, more for higher ratios). The motion is repeated as the gains
are increased until an oscillation is detected at the end of the move. When
this happens, the gains are decreased. If the rigidity level is other then 1, the
process is repeated using less reduction in the gains after oscillation while
watching for smaller amounts of oscillation.
Table 3: Pin Description (Servo Amplifier Side - 9 Pin Male)
Pin Number
Pin Name
Function
2
TXD - Transmit Data
output
4
RXD - Receive Data
input
9
GND
ground