3 position feedback system, 4 pressure sensor replacement – Flowserve StarPac 3 User Manual
Page 27
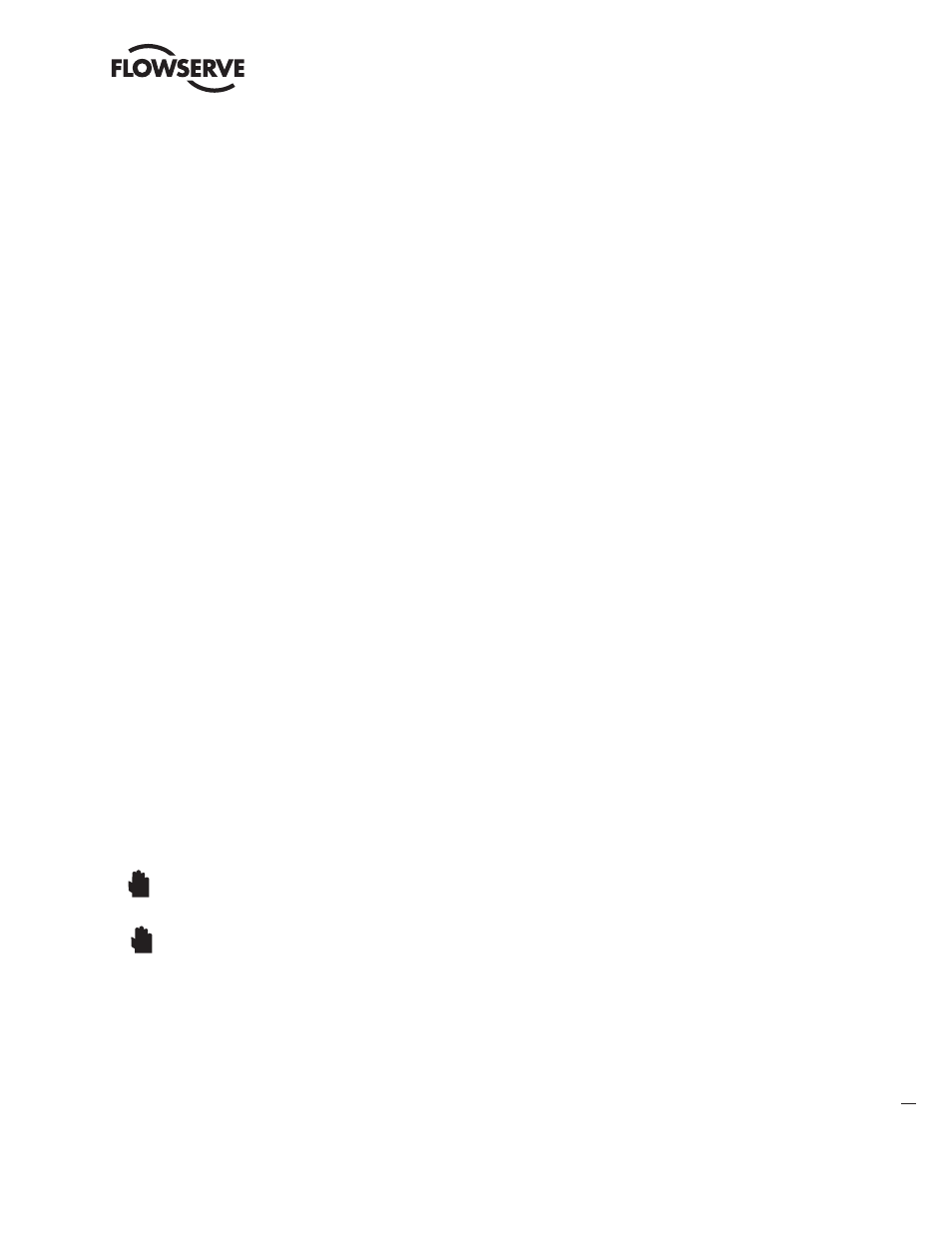
27
StarPac Intelligent Control System FCD VLENIM0066-05 04/14
flowserve.com
®
7. Standard valve maintenance may now be done on the actuator or valve body components. Refer to the Flow-
serve IOM instructions for details on such things as trim or packing replacement. If you have to replace the
trim, use the same trim number and characteristic as the original trim so the flow calculations are not affected.
If a trim size change is needed, contact your Flowserve representative to find out about flow characterization
options.
8. Reassemble the system by reversing the above steps. Be sure to follow the procedures outlined in the Flow-
serve Installation, Operation and Maintenance (IOM) instructions for valve reassembly. When reconnecting
the follower arm, make sure that the arm fits correctly on the keyed shaft and has a positive spring action.
9. Turn on the air supply to the valve and check for leaks in the reattached actuator tubing lines.
10. Turn on power to the unit. Check the system calibration and perform a Valve Stroke Calibration to reset the
position feedback. Refer to the Calibration section of the StarPac 3 User Interface Manual.
14.3 Position Feedback System
The position feedback linkage of the StarPac 3 system is a critical part of the system. This linkage is also used in the
StarPac 3 to calculate the valve’s CV for a given stroke for flow measurement. This linkage should be lubricated and
checked periodically for tight, smooth operation. The follower arm should operate smoothly with no binding and have
a positive spring loading on the arm. Inspect the follower arm pin for excess wear and replace if needed. The take-off
arm attached to the stem clamp must be firmly secured to the stem clamp and perpendicular to the actuator stem. If
this takeoff arm is canted or misaligned, problems may occur with positioner calibration and the position reading on
the unit may go out of range.
On rotary actuators, make sure the adjustment linkage locknut is tight and has no excessive play in the ball joints. The
rotary shaft clamp must be tight and should not freely rotate on the shaft.
14.4 Pressure Sensor Replacement
Standard StarPac 3 pressure sensors are typically installed directly into the control valve body. Before they can be
removed, the process line must be depressurized and drained of all fluids and the valve decontaminated.
To replace a pressure sensor, refer to Figure 10 then proceed as follows.
WARNING: The process line must be depressurized and drained of process fluid, and decontaminated prior to
working on internal valve components. Failure to do so may cause serious injury to personnel.
WARNING: If the pressure sensors are remote mounted, the sensor will be located in a sensor housing in the
tubing line and not in the sensor housing located on the valve body. This section of the tubing contains pro-
cess fluid and must be drained and decontaminated before the sensor is removed. The procedure for sensor
removal and replacement will be similar to that outlined below.
(Refer to alternate sensor information when this type of sensor is included with system.)
1. Depressurize and decontaminate the line and valve. Loosen the tubing nuts on the conduit leading to the
pressure sensor, if applicable.
2. Loosen the sensor nut.
3. Gently pull the conduit and sensor nut approximately 1/2” to 3/4” from the sensor. Use needle nose pliers to
STOP!
STOP!