Belshaw Adamatic INSIDER Ventless Donut System User Manual
Page 34
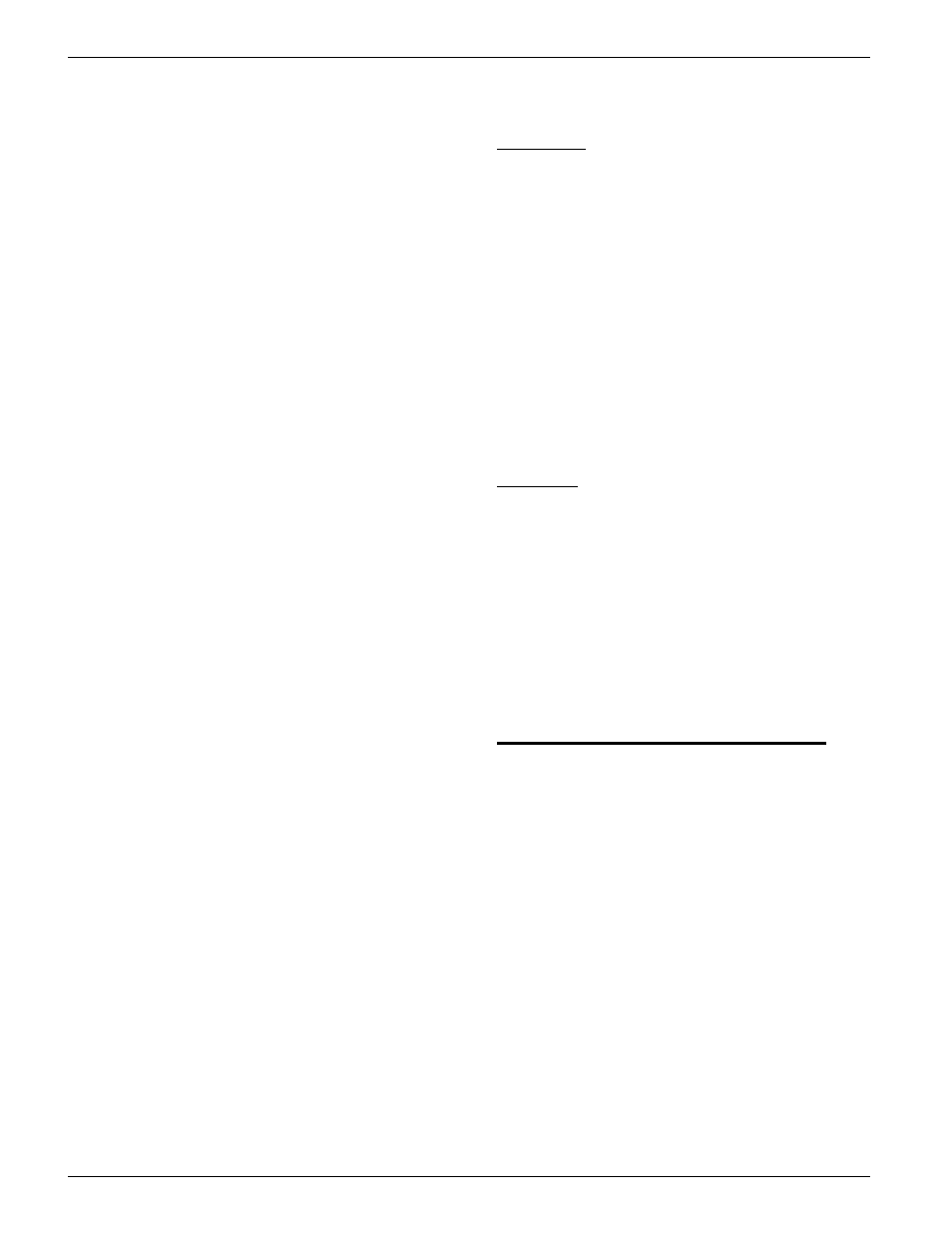
Belshaw Bros., Inc.
• www.belshaw.com • Phone 206-322-5474 • Fax 206-322-5425
8 MN-1853EN
Insider
TS
switch, and releasing devices, including
manual pull station and other associated
equipment. A discharge of the wet chemical
normally is not part of this test.
5. Where the maintenance of the system
reveals defective parts that could cause an
impairment of failure of proper operation of
the system, the affected parts shall be
replaced or repaired in accordance with the
manufacturer’s recommendations.
6. The maintenance report, with
recommendations, if any, shall be filed with
the owner or with the designated party
responsible for the system.
7. Each wet chemical system shall have a tag
or label securely attached, indicating the
month and year the maintenance is
performed and identifying the person
performing the service. Only the current tag
or label shall remain in place.
Fixed temperature-sensing elements of the
fusible metal alloy type shall be replaced at least
annually from the date of installation. They shall
be destroyed or removed.
The year of manufacture and the date of
installation of the fixed temperature-sensing
element shall be marked on the system inspection
tag. The tag shall be signed or initialed by the
installer.
Recharging
All extinguishing systems shall be recharged
after use or as indicated by an inspection or
maintenance procedure.
Systems shall be recharged in accordance with
the manufacturer’s installation and maintenance
manual.
Hydrostatic Testing
The following parts of wet chemical
extinguishing systems shall be subjected to a
hydrostatic pressure test at intervals not
exceeding 12 years:
1. Wet fire suppression cylinder
2. Auxiliary pressure container
Exceptions:
1. Auxiliary pressure containers not exceeding
2-in. (0.05-m) outside diameter and less than
2 ft (0.6-m) in length.
2. Auxiliary pressure containers bearing the
DOT “:3E” marking.
Wet fire suppression cylinder and auxiliary
pressure container, shall be subjected to a
hydrostatic test pressure equal to the marked
factory test pressure or the test pressure specified
by the manufacturer. No leakage or rupture shall
be permitted. The test procedure shall be in
accordance with the manufactures’ detailed
written hydrostatic test instructions.
Exception:
Containers bearing DOT or TC markings shall be
tested or replaced in accordance with the
appropriate DOT or TC requirements.
Wet chemicals removed from the containers
prior to hydrostatic testing shall be discarded.
To protect the hazard during hydrostatic testing,
if there is no connected reserve, alternate
protection acceptable to the authority having
jurisdiction shall be provided.
c) Pipe and Nozzle Installation
All pipe ends shall be thoroughly reamed after
cutting and all oil and foreign matter removed
from the pipe. It is recommended that the
following procedures be followed:
1. Disconnect and remove discharge piping
from the inside.
2. Make certain that all threaded ends and pipe
are clean and the pipe is free of foreign
matter and oil.
3. Apply Teflon tape on threaded ends. Start at
the second mail thread, wrapping the tape
clockwise around the threads, away from the
pipe opening.
4. Do not over tighten, but be sure the pipe is
snug. Do not back-off sections of pipe to
make them fit better.