Electrical connections, Protection systems – Flowserve U-MAG INNOMAG User Manual
Page 18
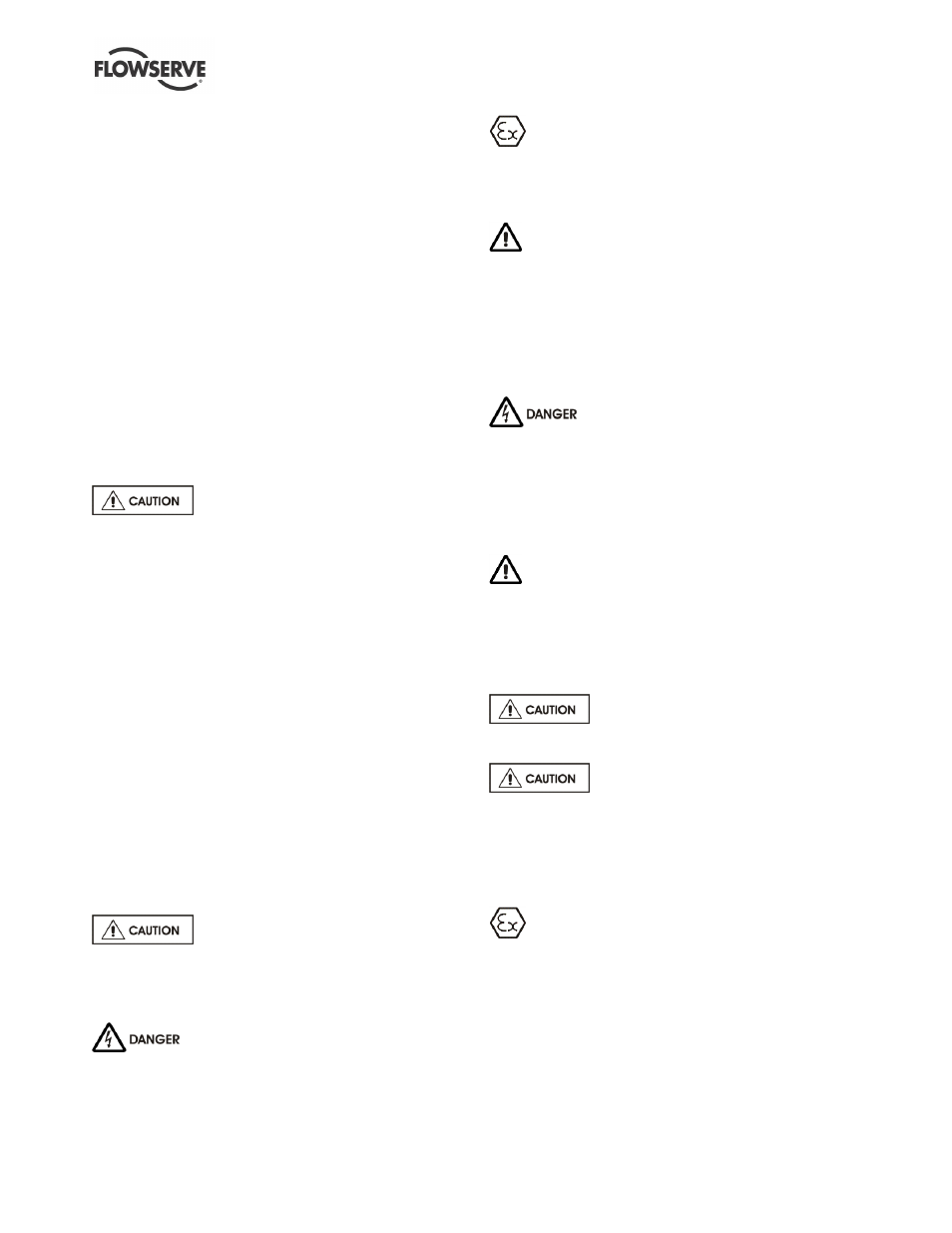
U-MAG ENGLISH 26999990 10-14
Page 18 of 40
Avoid the use of throttling valves and strainers in the
suction line. Start-up strainers must be removed
shortly before start up. When the pump is installed
below the source of supply, a valve should be
installed in the suction line to isolate the pump and
permit pump inspection and maintenance. However,
never place a valve directly on the suction nozzle of
the pump.
Refer to the Centrifugal Pump IOM Section of the H.I.
Standards for additional recommendations on suction
piping. (See section 10.)
Refer to section 3.4 for performance and operating
limits.
4.5.3 Discharge piping
Install a valve in the discharge line. This valve is
required for regulating flow and/or to isolate the pump
for inspection and maintenance.
When fluid velocity in the pipe is high,
for example, 3 m/s (10 ft/sec) or higher, a rapidly
closing discharge valve can cause a damaging
pressure surge. A dampening arrangement should
be provided in the piping.
4.5.4 Allowable nozzle loads
Maximum forces and moments allowed on the pump
flanges vary with the pump size and type. To minimize
these forces and moments that may, if excessive, cause
misalignment, hot bearings, worn couplings, vibration
and the possible failure of the pump casing, the
following points should be strictly followed:
Prevent excessive external pipe load
Never draw piping into place by applying force to
pump flange connections
Do not mount expansion joints so that their force,
due to internal pressure, acts on the pump flange
Contact your local Flowserve Sales office, Distributor,
or Representative for further details.
4.5.5 Auxiliary piping
The connections that are to be piped
up will have been fitted with protective metal or
plastic plugs which will need to be removed.
4.6 Electrical connections
Electrical connections must be made by
a qualified Electrician in accordance with relevant
local national and international regulations.
It is important to be aware of the EUROPEAN
DIRECTIVE on potentially explosive areas where
compliance with IEC60079-14 is an additional
requirement for making electrical connections.
It is important to be aware of the EUROPEAN
DIRECTIVE on electromagnetic compatibility when
wiring up and installing equipment on site. Attention
must be paid to ensure that the techniques used during
wiring/installation do not increase electromagnetic
emissions or decrease the electromagnetic immunity of
the equipment, wiring or any connected devices. If you
have any doubt contact Flowserve for advice.
The motor must be wired up in
accordance with the motor manufacturer's
instructions (normally supplied within the terminal
box) including any temperature, earth leakage,
current and other protective devices as appropriate.
The identification nameplate should be checked to
ensure the power supply is appropriate.
A device to provide emergency stopping must
be fitted. If not supplied pre-wired to the pump unit,
the controller/starter electrical details will also be
supplied within the controller/starter. For electrical
details on pump sets with controllers see the
separate wiring diagram.
See section 5.1, Direction of rotation
before connecting the motor to the electrical supply.
For close coupled pumps it is
necessary to wire the motor with flexible conduit of
sufficient length to allow the motor/power end
assembly to be moved back from the casing [1100]
for maintenance.
4.7 Protection systems
The following protection systems are
recommended particularly if the pump is installed in a
potentially explosive area or is handling a hazardous
liquid. If in any doubt consult Flowserve.
If there is any possibility of the system allowing the
pump to run against a closed valve or below
minimum continuous safe flow a protection device
should be installed to ensure the temperature of the
liquid does not rise to an unsafe level.