Maintenance schedule – Flowserve U-MAG INNOMAG User Manual
Page 22
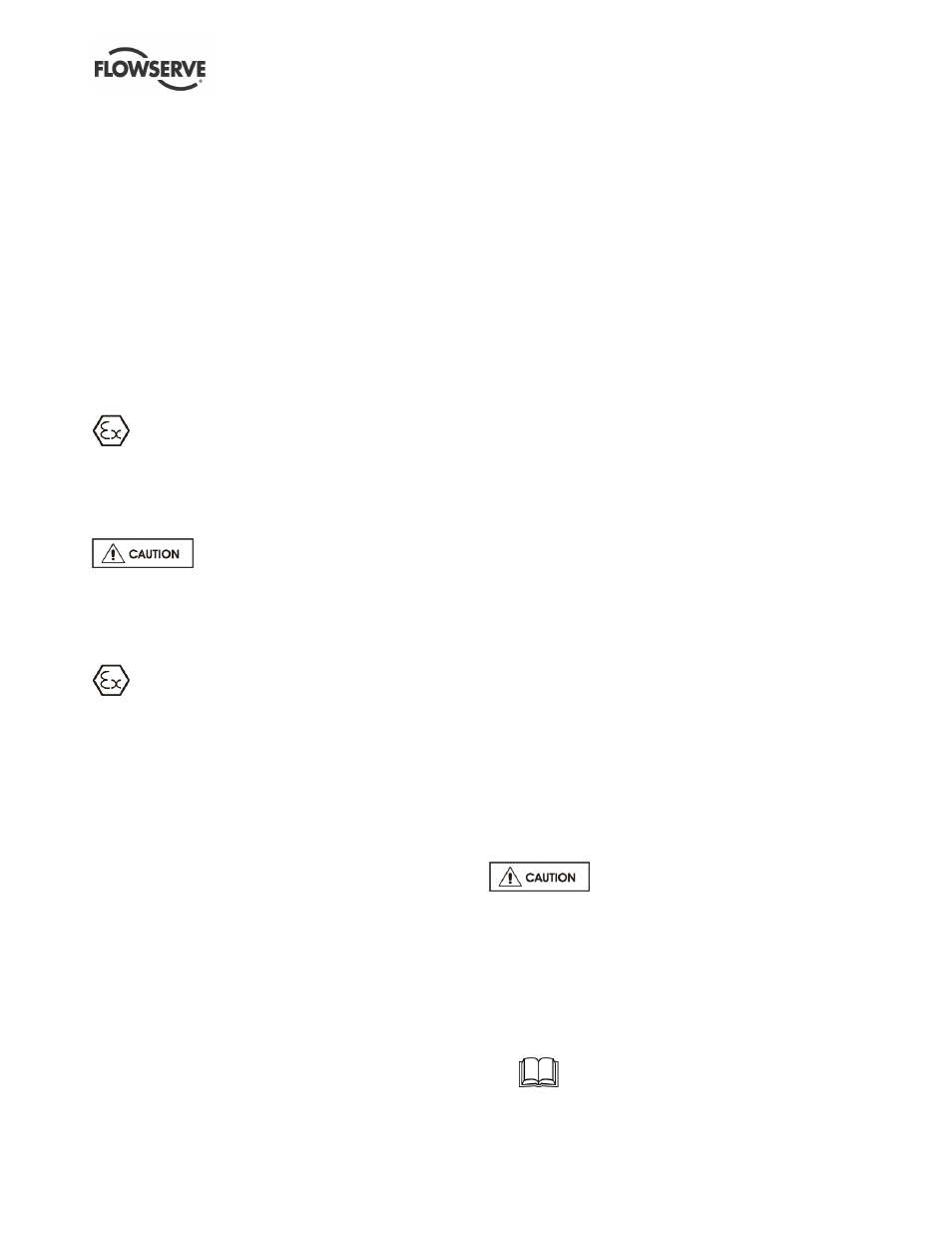
U-MAG ENGLISH 26999990 10-14
Page 22 of 40
Never use air or compressed inert gas to clean
clothes.
Before working on the pump, take measures to
prevent an uncontrolled start. Put a warning board
on the starting device with the words:
"Machine under repair: do not start".
With electric drive equipment, lock the main switch
open and withdraw any fuses. Put a warning board
on the fuse box or main switch with the words:
"Machine under repair: do not connect".
Never clean equipment with flammable solvents or
carbon tetrachloride. Protect yourself against toxic
fumes when using cleaning agents.
When operating with CHARGABLE LIQUIDS
with conductivities of <10-8 S/m, inert gases (e.g.
nitrogen) must be used to flush the pump. Before
removal of the pump it is recommended to wait one
hour to allow static peak charges to be eliminated.
ALWAYS make certain that no toxic or
flammable fumes / vapors remain in the pump casing
[1100] or surrounding area.
6.2 Maintenance schedule
It is recommended that a maintenance plan and
schedule is adopted, in line with these User
Instructions, to include the following:
a) Any auxiliary systems installed must be
monitored, if necessary, to ensure they function
correctly.
b) Check for any leaks. Pump is designed to be
leak-free, any leak is abnormal.
c) Check that the duty condition is in the safe
operating range for the pump.
d) Check vibration, noise level and surface
temperature to confirm satisfactory operation.
e) Check dirt and dust is removed from areas around
close clearances and motors.
Our specialist service personnel can help with
preventative maintenance records and provide
condition monitoring for temperature and vibration to
identify the onset of potential problems.
If any problems are found the following sequence of
actions should take place:
a) Refer to section 7, Troubleshooting, for fault
diagnosis.
b) Ensure equipment complies with the
recommendations in this manual.
c) Contact Flowserve if the problem persists.
6.2.1 Preventive Maintenance Guidelines
Different applications call for different preventative
maintenance schedules. Applications that involve
pumping abrasives, or applications that are likely to
precipitate solids should be examined on a regular
basis to ensure that accumulating solids (if any) are
removed. There are many factors that can
necessitate periodic preventative maintenance and
inspection, but for clean, continuously operating
services, preventative maintenance can usually be
done without disassembling the pump. See
recommended spare parts list for more information.
Devices/techniques to help monitor the pump
externally:
a) Install pressure gauges on the suction and
discharge
b) Regularly monitor the process conditions
c)
Use the motor’s fan to check for free rotation
d) Use a shaft power monitor to protect the pump as
well as monitor pump performance
e) Check vibration, noise level and surface
temperature to confirm satisfactory operation.
For preventative maintenance schedule
recommendations that are specific to your
application, please contact your authorized local
distributor.
If ABRASIVE SOLIDS are present within the fluid,
additional wear of the pump should be expected.
Intervals between inspections should be shortened
compared to usual times.
6.2.2 Routine inspection (daily/weekly)
The following checks should be made
and the appropriate action taken to remedy any
deviations:
a) Check operating behaviour. Ensure noise,
vibration and bearing temperatures are normal.
b) Check that there is no abnormal fluid leak from
the pump.
c) Check any auxiliary equipment or supplies are
functioning correctly.
Refer to the manuals of any associated
equipment for routine checks needed.