Final checks, Commissioning, start-up, operation and shutdown, Direction of rotation – Flowserve U-MAG INNOMAG User Manual
Page 19
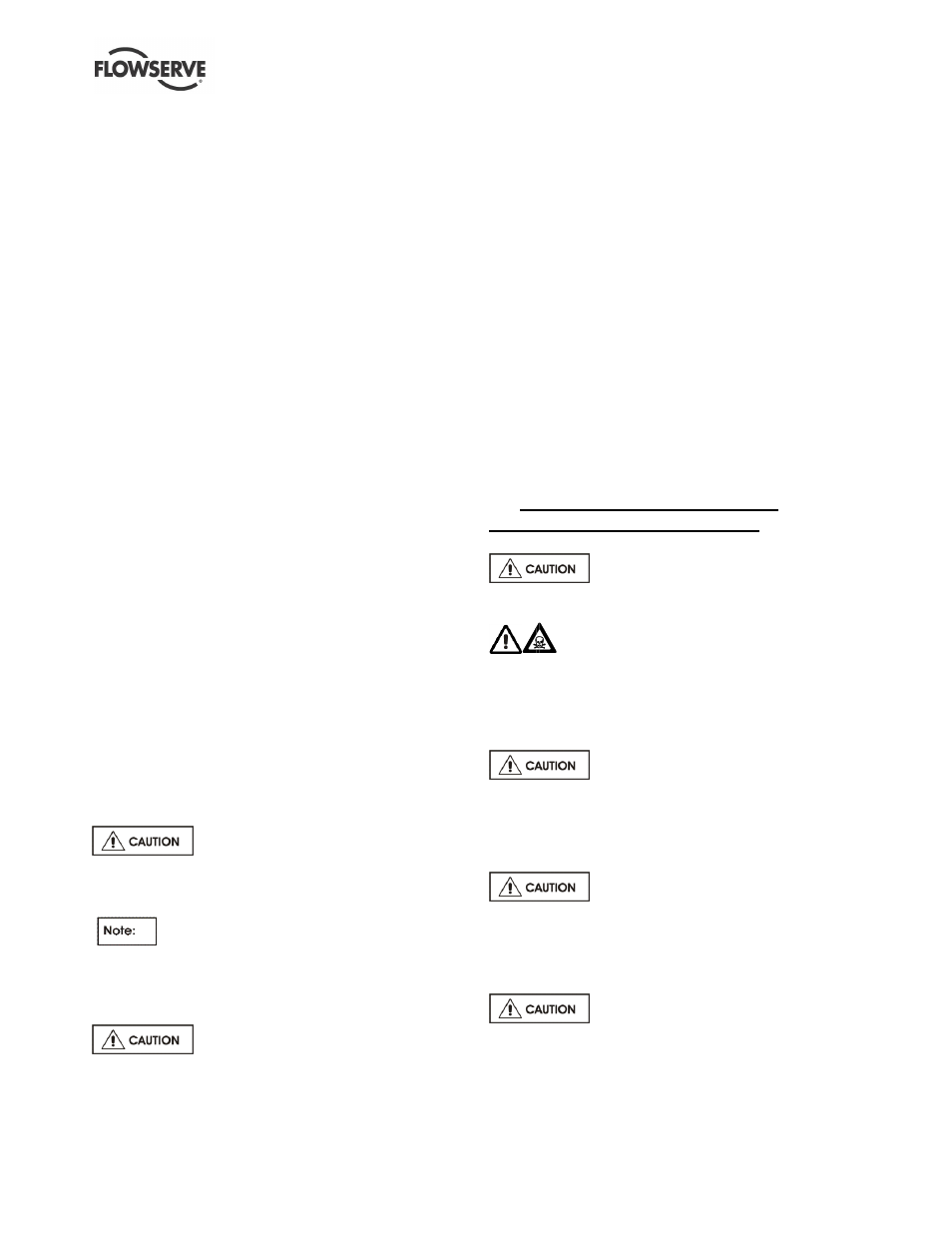
U-MAG ENGLISH 26999990 10-14
Page 19 of 40
If there are any circumstances in which the system
can allow the pump to run dry, or start up empty, a
power monitor should be fitted to stop the pump or
prevent it from being started. This is particularly
relevant if the pump is handling a flammable liquid.
If leakage of product from the pump or its associated
sealing system can cause a hazard it is
recommended that an appropriate leakage detection
system is installed.
To prevent excessive surface temperatures at
bearings it is recommended that temperature or
vibration monitoring is carried out.
4.7.1 Auxiliary equipment
– instrumentation
Contact your local Flowserve Sales office, Distributor,
or Representative for more details.
4.7.1.1 Leak detection
An intrinsically-safe, optical leak detection system is
available for U-
MAG™ pumps.
4.7.1.2 Temperature probe
An optional ThermicSense temperature probe can be
installed on the casing drain to monitor the internal
fluid in the casing [1100].
4.7.1.3 ThermicSense Installation
The ThermicSense thermowell will be packaged
separately for protection during shipping and must be
assembled before use. For wiring refer to the
thermocouple sensor manufacturer’s instructions
a)
Verify that rubber gasket / o-ring is secured to
temperature sensor tip.
b)
Insert temperature sensor tip into the thermowell
and hand tighten.
c)
Use a 1/2 in. wrench to fully secure the sensor to
the thermowell.
Do not over-tighten.
d)
Adjust direction of sensor sheathing before
tightening compression fitting.
e)
Ensure sensor tip is fully pressed into thermowell.
The sensor must be fully inserted to get an
accurate reading.
f)
Hand-tighten the compression fitting.
g)
Use a 1/2 in. wrench to fully tighten the
compression fitting and secure sensor sheathing.
Do not over tighten the fitting.
h)
Affix the PTFE drain gasket to thermal well.
i)
Insert the completed ThermicSense assembly into
the casing drain and insert 1/2 in.-13 bolts with lock
washers.
j)
Tighten bolts evenly to maintain alignment and
torque to 13.5 Nm (10 lbf
•ft)
k)
Install wire leads to appropriate temperature
monitor per manufacturer instructions and
guidelines.
4.8 Final checks
Alignment between the pump shaft and motor shaft is
built in by precise machining of the parts that position
these shafts. Parallel alignment of 0.18 mm (0.007
in.) and angular alignment of 0.002 mm/mm (0.002
in./in.) can be expected.
Check the tightness of all bolts in the suction and
discharge pipework. Check also the tightness of all
foundation bolts.
5 COMMISSIONING, START-UP,
OPERATION AND SHUTDOWN
These operations must be carried
out by fully trained and qualified personnel.
Personal Protection Equipment suitable for
the conditions and environment must be worn at all
times.
5.1 Direction of rotation
Correct rotation is indicated by the
arrow on the casing [1100]. Improper rotation will not
damage the pump however, performance is greatly
reduced. Rotation may be determined by viewing the
motor’s fan.
Do not bump the motor to test rotation
or run the pump without the suction completely flooded.
Dry running can damage the pump in a matter of
seconds if the pump is not equipped with dry-run
bearings.
If maintenance work has been carried
out to the site's electricity supply, the direction of
rotation should be re-checked in case the supply
phasing has been altered.