9 protection systems, 5 commissioning, startup, operation and shutdown, 1 pre-commissioning procedure – Flowserve ESP2 User Manual
Page 27: 1 pre start-up checks, 2 packing and mechanical seals, 1 installing mechanical seals
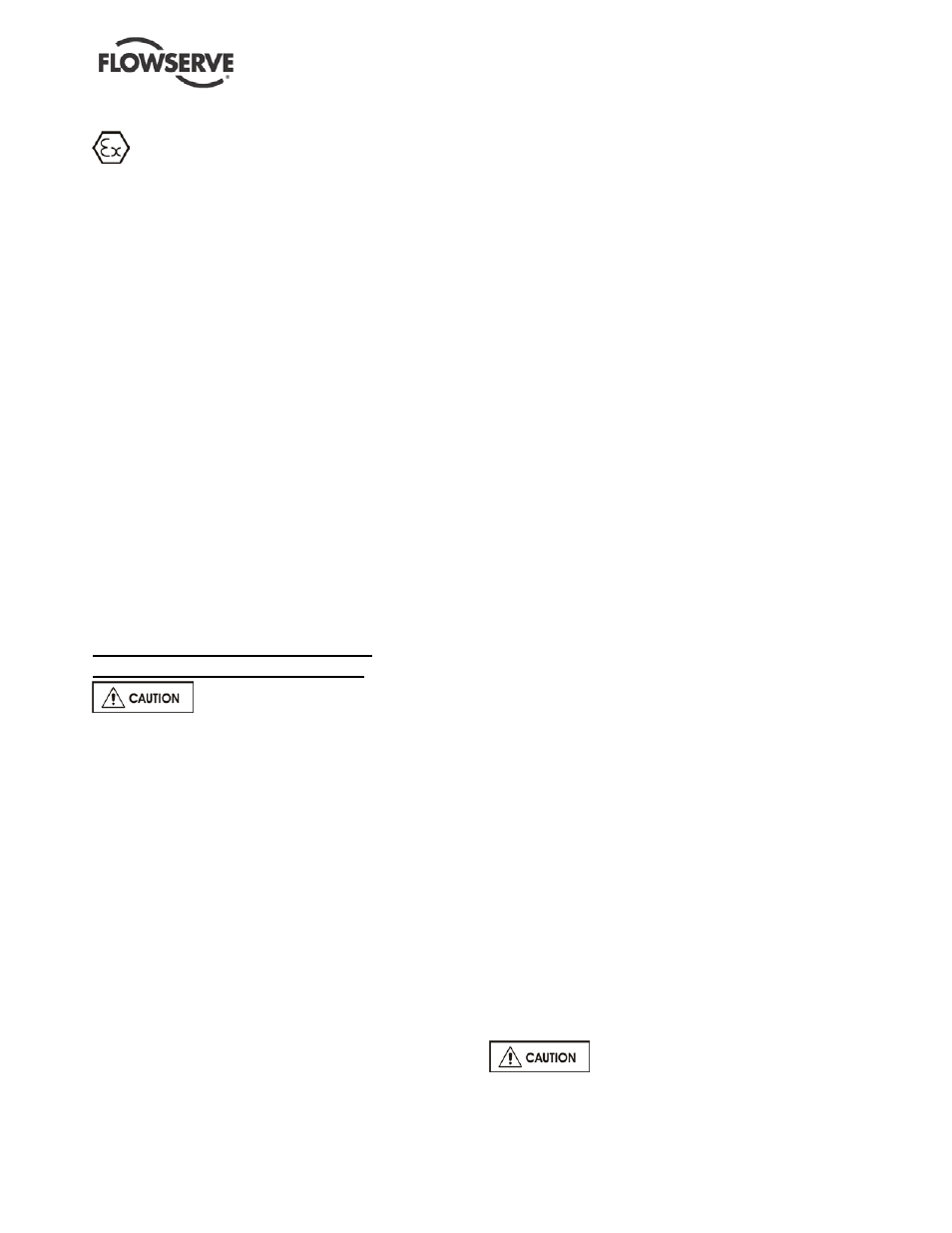
ESP2 USER INSTRUCTIONS ENGLISH PCN-(71569292) 4-12
Page 27 of 64
4.9 Protection systems
The following protection systems are
recommended particularly if the pump is installed in a
potentially explosive area or is handling a hazardous
liquid. If in doubt consult Flowserve.
If there is any possibility of the system allowing the
pump to run against a closed valve or below
minimum continuous safe flow a protection device
should be installed to ensure the temperature of the
liquid does not rise to an unsafe level.
If there are any circumstances in which the system
can allow the pump to run dry, or start up empty, a
power monitor should be fitted to stop the pump or
prevent it from being started. This is particularly
relevant if the pump is handling a flammable liquid.
If leakage of product from the pump or its associated
sealing system can cause a hazard it is
recommended that an appropriate leakage detection
system is installed.
To prevent excessive surface temperatures at
bearings it is recommended that temperature or
vibration monitoring is carried out.
5 COMMISSIONING, STARTUP,
OPERATION AND SHUTDOWN
These operations must be carried
out by fully qualified personnel.
5.1 Pre-commissioning procedure
5.1.1 Pre start-up checks
Prior to starting the pump it is essential that the
following checks be made. These checks are all
described in detail in the Maintenance section of this
manual.
• Pump and motor properly secured to the
baseplate
• All fasteners tightened to the correct torque (see
section 6.5)
• Coupling guard in place and not rubbing
• Rotation check (see sections 4.5 and 5.4).
This is absolutely essential
• Impeller clearance setting
• Shaft seal (if supplied) properly installed
• Seal support system (if supplied) operational
• Bearing lubrication
• Pump instrumentation is operational
As a final step in preparation for operation, it is
important to rotate the shaft by hand to be certain that
all rotating parts move freely, and that there are no
foreign objects in the pump casing.
5.1.2 Packing and mechanical seals
Pumps supplied with vapor proof construction or
pressurized design are furnished with an upper
stuffing box (4100) equipped to take mechanical
seals or packing (See Vapor Proof and Pressurized
Design cross-sections in section 8).
5.1.2.1 Installing mechanical seals
Mechanical seals (4200) are usually shipped
separately to prevent damage during shipment. To
install the seal some disassembly will be required
(Split seals require no disassembly and only steps e.
and f. should be followed).
a)
Unbolt the support head (3160) from the bearing
bracket (3130).
b)
Unbolt the thrust bearing holder (3110) and
disconnect the thrust bearing assembly (3712,
3031) (Do not remove the thrust bearing (3031)
from the sleeve (3712)).
c)
Remove the bearing bracket (3130).
d)
If the pump comes with the gland (4120.2)
already on the stuffing box (4100), then it must
be removed at this time before the seal can be
set in the stuffing box.
e)
Temporarily wrap Teflon tape on the shaft
threads to protect the seal from damage while
being slid on the shaft.
f)
CAREFULLY slip the seal (4200) onto the shaft
(2100) and slide it down until it sets into the
stuffing box (4100). DO NOT SET THE SEAL
AT THIS TIME.
g)
Slip the gland (4120.2) over top the stuffing box.
Leave the gland and seal (4200) loose on the
shaft for now.
h)
Reassemble the bearing bracket (3130), then
the thrust bearing assembly (3712, 3031), thrust
bearing holder (3110), and finally the support
head (3160).
i)
The impeller must be set before the seal. Follow
the directions listed in section 5.3.
j)
Now the seal can be set. For the proper seal
setting consult Figures 5.1 and 5.2. If the seal
being used is not contained in the seal settings
chart, follow the seal manufacturer's instructions
and drawings furnished with the mechanical
seal.
Seals must never be run without
lubrication. Abrasive lubrication will greatly
reduce seal life.