Flowserve MF User Manual
Page 34
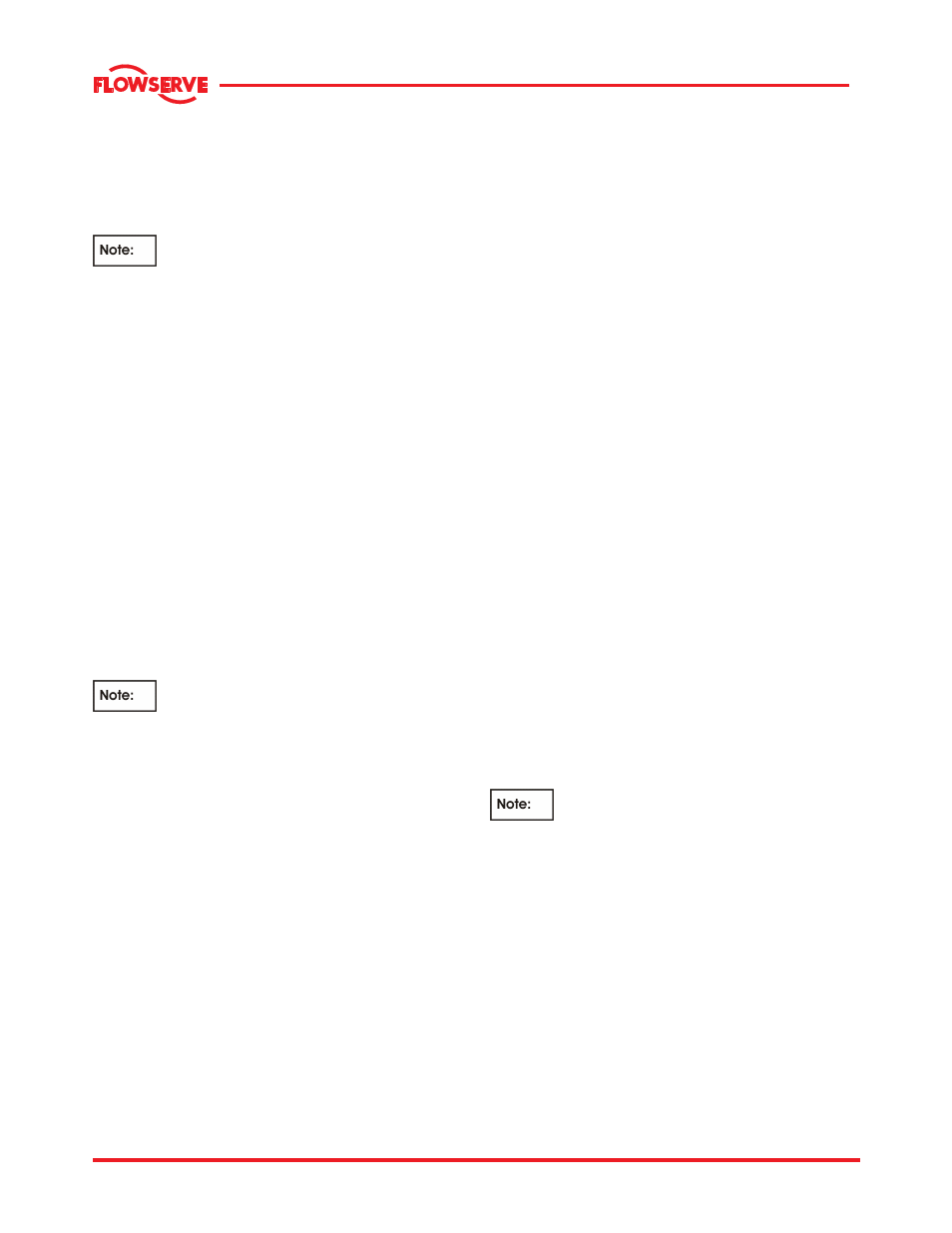
MF USER INSTRUCTIONS ENGLISH 71569191 12/04
Page 34 of 50
®
6.1.6.1 Measuring wearing ring gap
There are two methods for checking wearing ring
clearance on pumps equipped with axial wearing ring
construction. The simplest is to remove the suction
head hand hole cover and check with a feeler gauge
around the gap perimeter. The second method is as
follows but is difficult to perform on horizontal pumps:
The bearing frame support bolts must be
loosened to allow movement of the bearing frame
during adjustment. Be sure to re-tighten the bolts
when the wearing ring gap adjustment is completed.
a) Disconnect pump-coupling halves if required.
b) Back off the bearing frame retaining screws
between the bearing frame and the stuffing box
approximately 1.5 mm (0.06 in.). Do Not
Remove. For 7A frame units remove the cap
screw holding the bearing frame support to the
bearing frame.
c) Tighten the two exterior jacking bolts to break the
shim joint, then remove all shims.
d) Bottom out the rotor in casing by backing out
adjusting bolts. Tap the coupling end of the shaft
assembly with a mallet until the rotor makes
contact with the casing.
e) Measure the gap between the bearing housing
and the stuffing box head flange. Add 0.25 mm –
0.050 mm (0.010 – 0.020 in.) to the
measurement and select the required adjusting
shims.
6.1.6.2 Adjusting wearing ring gap
Pumps equipped with mechanical seals
may require rotor removal and resetting of the seal
after adjusting the wearing gap.
After the actual ring gap has been determined, adjust
the shim pack as required to obtain the desired ring
gap. If the desired ring gap cannot be obtained
because of having reached the limit of axial
adjustment, one or both of the wearing surfaces will
have to be restored or replaced.
a) Loosen the 4 screws (or nuts) between the
bearing frame and the stuffing box head. Break
the shim joint by tightening the two adjusting bolts
and remove the shims.
b) Adjust shim pack thickness such that the desired
wearing gap will result. Put the adjusted shim
pack back in place. The following chart is
provided for identification of shim stock by color:
Light Brown
0.76mm (0.030 in.)
Yellow
0.50mm (0.020 in.)
Brown
0.25mm (0.010 in.)
Blue
0.13mm (0.005 in.)
c) Back off the two adjusting bolts until they no
longer project into the gap between bearing frame
and stuffing box head.
d) Tighten the 4 screws (or nuts) between bearing
frame and stuffing box.
e) Re-check the ring gap and repeat steps (a)
through (d) if necessary.
f) For 7A frame horizontal pumps replace and
tighten cap screws between bearing frame support
and bearing frame.
g) Adjust pump coupling half to pump shaft
engagement as necessary to compensate for the
shim adjustment.
If the required axial clearance cannot be obtained
because of having reached the limit of axial
adjustment, one or both of the wearing surfaces must
be restored.
Optional single or double wearing rings (supplied if
ordered) are mounted on the impeller and/or casing
and are held in place by screws which are retained
with Loctite thread locker #271 or equivalent to
prevent loosening. It may be necessary to heat
screws to 400 degrees F to remove them.
6.1.6.3 Removal of wearing rings
The impeller and suction head wearing rings are held
in place by screws locked in place using Loctite 271
or equivalent. They may require heating to 200
o
C
(400
o
F) to allow removal.
6.1.6.4 Mounting of wearing rings
Clean the screw threads and taps. Clean the ring
and the area where the ring is to be mounted. Mount
the ring and secure it using screws with Loctite 271
or equivalent applied to the threads.
New tapped holes may be required to
facilitate installation of a new wearing ring. Use the
wearing ring as a template.
6.1.7 Maintenance of shaft and shaft sleeve
When the pump is dismantled, examine the shaft
carefully. Its condition should be checked at the
impeller hub fit, under the shaft sleeve (if sleeve is
removed), at the bearings, and under the coupling
flange (if flange is removed). The shaft may become
damaged by rusting or pitting due to leakage along
the shaft at the impeller or shaft sleeve, excessive
exposure to moisture, or mishandling.
Anti-friction bearings improperly fitted to the pump
shaft may result in the bearing cone rotating on the
shaft, thus causing undue damage.