Worcester controls – Flowserve Worcester Controls Electri-SAFE DataFlo User Manual
Page 10
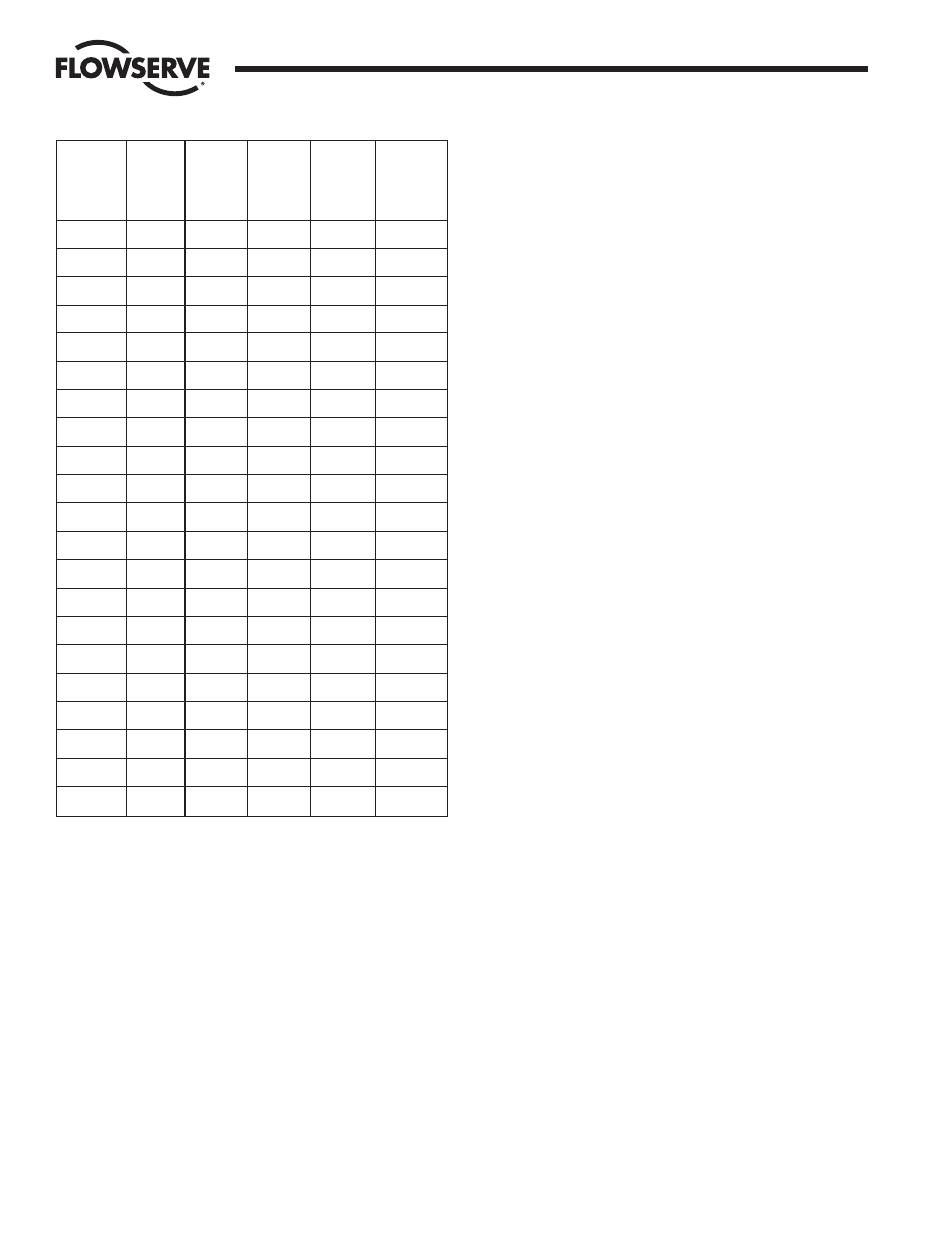
10
Electri-SAFE DataFlo Digital Electronic Positioner
FCD WCAIM2048-01
Flow Control
Worcester Controls
4.4.11 Positioner Deadband
The display will alternately display dEbA and the deadband
value.
The deadband is used to prevent oscillations about a setpoint
because of small fluctuations in either the setpoint signal or
the position feedback signal. The deadband represents a plus
and minus percentage of the full range of either the input
signal or the feedback signal. Fixed deadband values can be
selected from 0.1 to 10.0 (percent) of range. When the DOWN
switch is pressed when the right most digit is selected, the
display will show Auto. Pressing SEL while on that screen will
select Auto deadband.
A deadband setting of Auto will allow constant automatic
adjustment of the deadband in an adaptive fashion as required
for best performance. This is the recommended setting. The
lower Auto default value is .5 but this can be changed with
the manual setting. Whatever value has been set for the
manual deadband setting, becomes the lower limit for the
Auto deadband mode.
4.4.12 Loss-of-Signal Position and Delay Time
The display will alternately display SPOS and the position the
valve will move to if there is a loss of signal. A loss-of-signal
condition occurs in either of two situations: 1) When the
positioner is in analog position control and the input signal is
less than 2 mA; or 2) When the positioner is controlled by the
serial data link (digital control) and no signal has been
received within the SPt time period.
When a loss of signal occurs in the analog control mode, the
positioner will immediately go to the SPOS position. A HOld
option specifies the positioner is to hold its current position.
The positioner will hold the SPOS position until a valid analog
input signal is present for the SPt delay period. If the SPt
parameter is set to 0 seconds, restoration of the signal will
cause the positioner to work as normal with no time delay.
A loss of signal in PC CMD control mode means the
positioner has not received a valid command within the SPt
time period. In that case, the positioner will immediately go to
the SPOS position. A HOld option specifies the positioner is
to hold its current position. The positioner will hold the SPOS
position until a valid digital position command is received.
The display will alternately display SPt and the delay time (in
seconds). The time range is 0 to 9999 seconds. A time of 0 in
analog control mode disables the loss-of-signal option. A time
of 0 in digital control mode effectively disables the loss-of-
signal option by allowing an infinite time between received
commands. In digital-control mode, non-zero SPt time values
less than three seconds will use three seconds as the delay.
4.4.13 Power-On Position and Delay Time
When power is first applied to the positioner and the unit is in
analog signal control mode, it will go to the position specified
by the PPOS parameter for a time specified by the PPt
parameter. During that time, any input signal is ignored.
If the unit is in PC Cmd control mode and there is a valid PC
signal, the unit will respond to the signal immediately,
otherwise, it will go to the power on position for the PPt time
and then go to the SPOS position for the SPt time.
The display will alternately display PPOS and the position (in
percent) the valve will move to when power is first applied or
when power is restored. The actuator will hold that position
for the time specified in the next step. The position range is
0.0 to 100.0% and HOLd. A HOLd option specifies the
positioner is to hold the last position (i.e., the actuator will
not move).
The display will alternately display PPt and the time (in
seconds) that the PPOS position will be held. During that
time, the positioner will ignore any input signal and will hold
the PPOS position. The time range is 0 to 9999 seconds. A
time of 0 disables this option such that the positioner will
immediately respond to the input signal when power is first
applied or restored.
Free
Free
Linear
Curve #1
Curve #2
Free
Free
Curve
1:25
1:50
Curve #3
Curve #4
Parameter
(Lin)
(FrE1)
(FrE2)
(FrE3)
(FrE4)
SL 0
0.0 %
0.0 %
0.0 %
0.0 %
0.0 %
SL 1
5.0 %
0.8 %
0.3 %
5.0 %
5.0 %
SL 2
10.0 %
2.1 %
0.8 %
10.0 %
10.0 %
SL 3
15.0 %
3.2 %
1.5 %
15.0 %
15.0 %
SL 4
20.0 %
4.9 %
2.6 %
20.0 %
20.0 %
SL 5
25.0 %
6.5 %
3.7 %
25.0 %
25.0 %
SL 6
30.0 %
8.4 %
5.0 %
30.0 %
30.0 %
SL 7
35.0 %
10.7 %
6.6 %
35.0 %
35.0 %
SL 8
40.0 %
13.2 %
8.4 %
40.0 %
40.0 %
SL 9
45.0 %
15.7 %
10.9 %
45.0 %
45.0 %
SL10
50.0 %
18.7 %
13.5 %
50.0 %
50.0 %
SL11
55.0 %
22.6 %
16.5 %
55.0 %
55.0 %
SL12
60.0 %
27.2 %
20.3 %
60.0 %
60.0 %
SL13
65.0 %
33.4 %
25.0 %
65.0 %
65.0 %
SL14
70.0 %
40.0 %
31.1 %
70.0 %
70.0 %
SL15
75.0 %
46.0 %
36.8 %
75.0 %
75.0 %
SL16
80.0 %
53.8 %
45.4 %
80.0 %
80.0 %
SL17
85.0 %
63.2 %
54.4 %
85.0 %
85.0 %
SL18
90.0 %
73.7 %
67.5 %
90.0 %
90.0 %
SL19
95.0 %
86.2 %
85.0 %
95.0 %
95.0 %
SL20
100.0 % 100.0 %
100.0 %
100.0 %
100.0 %