0 technical data, 0 switch option, Worcester controls – Flowserve Worcester Controls Electri-SAFE DataFlo User Manual
Page 17
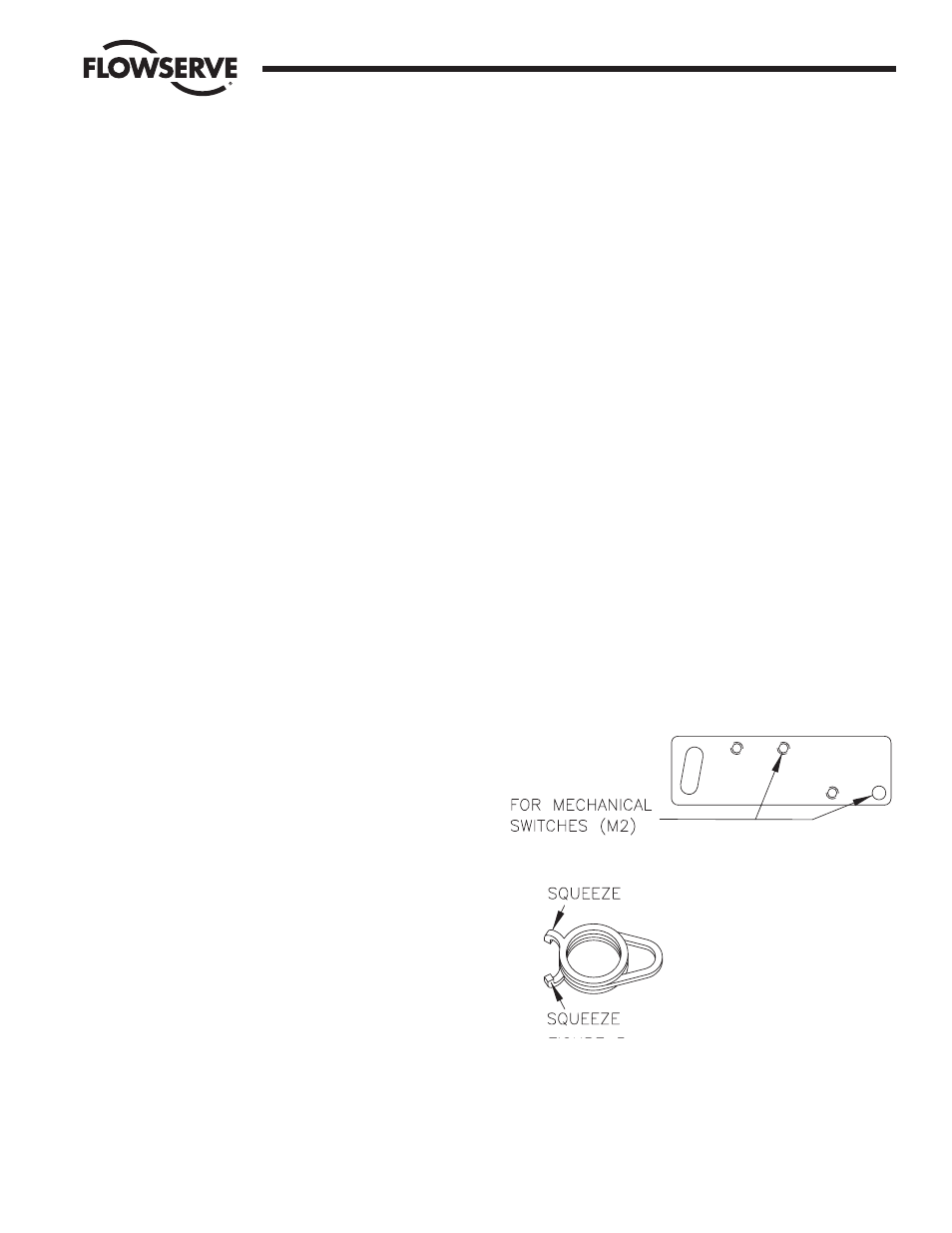
FCD WCAIM2048-01
Electri-SAFE DataFlo Digital Electronic Positioner
17
Flow Control
Worcester Controls
5.0 Technical Data
5.1 Allowable Supply Voltage Range
120 VAC ±10% 50/60 Hz
Power Consumption
3 Watts
5.2 Input Circuit Specifications
Maximum Tolerated Noise Level at Maximum Positioner
Resolution/Sensitivity: Approx. 3.5 mV (16 microamps)
Resistance Input
DP72-1K
Nominal 1000 Ohms
DP72-13
Nominal 135 Ohms
Current Input
DP72-1
1 to 5 milliamps
DP72-4
4 to 20 milliamps
DP72-10
10 to 50 milliamps
Voltage Input
DP72-5V
0 to 5 VDC
DP72-XV
0 to 10 VDC
5.3 Output Circuits Specifications
5.3.1 Motor Driver Circuitry Specifications
Maximum Normal Starting or In-Rush Current
10 amps for 1 second
Maximum Stall Current
8 amps for 1 minute
Maximum Running Current
5 amps (resistive load, 90% duty cycle)
Maximum Running Current
3 amps (inductive load, 90% duty cycle)
Maximum Peak Voltage at Load Circuit
800 VAC
5.3.2 Position Feedback – Current Output
4-20 mA output – will drive 20 mA into a maximum load of
350 ohms.
Maximum Voltage Output: 8 volts
Maximum Load Impedance: 350 ohms
5.3.3 Alarm Output
100 mA maximum at 50 volts DC maximum
5.4 Input Circuit Load Resistances
1 to 5 mA Models
Approx. 1000 Ohms
4 to 20 mA Models
Approx. 220 Ohms
10 to 50 mA Models
Approx. 100 Ohms
0 to 5 VDC Models
Approx. 800 Ohms
0 to 10 VDC Models
Approx. 1100 Ohms
6.0 Switch Option
A mechanical switch option is available in the Electri-SAFE Positioner.
The switches can be used to provide actuator position indication or to
control other equipment.
The option always available (regardless of other options) is:
M2 – Two Single-Pole, Double-Throw Mechanical Switches
The standard switches provided will be standard contact types
suitable for low-power applications (120/240 VAC, 1A). Switches
capable of handling higher currents are available through Flowserve.
An “Adjustment Plate” is used to mount the single-pole mechanical
switches to the base plate. Mechanical switches are mounted to the
adjustment plate and set to a middle position — not rotated towards
or away from the shaft. There are two sets of mounting holes in the
adjustment plate, use the appropriate set as shown below. Their use
will be detailed later.
The cams used to actuate the switches offer unlimited positioning
without the use of tools. These cams are essentially “wrap-springs”
and grip the shaft tightly enough to prevent accidental rotation.
Squeezing together the two small protrusions from the cam, as shown
above, loosens the spring and allows adjustment. Needle nose pliers
may prove to be helpful when installing the cams, but are not required.
Figure 2
Figure 3