Flowserve Worcester Controls Electri-SAFE DataFlo User Manual
Page 4
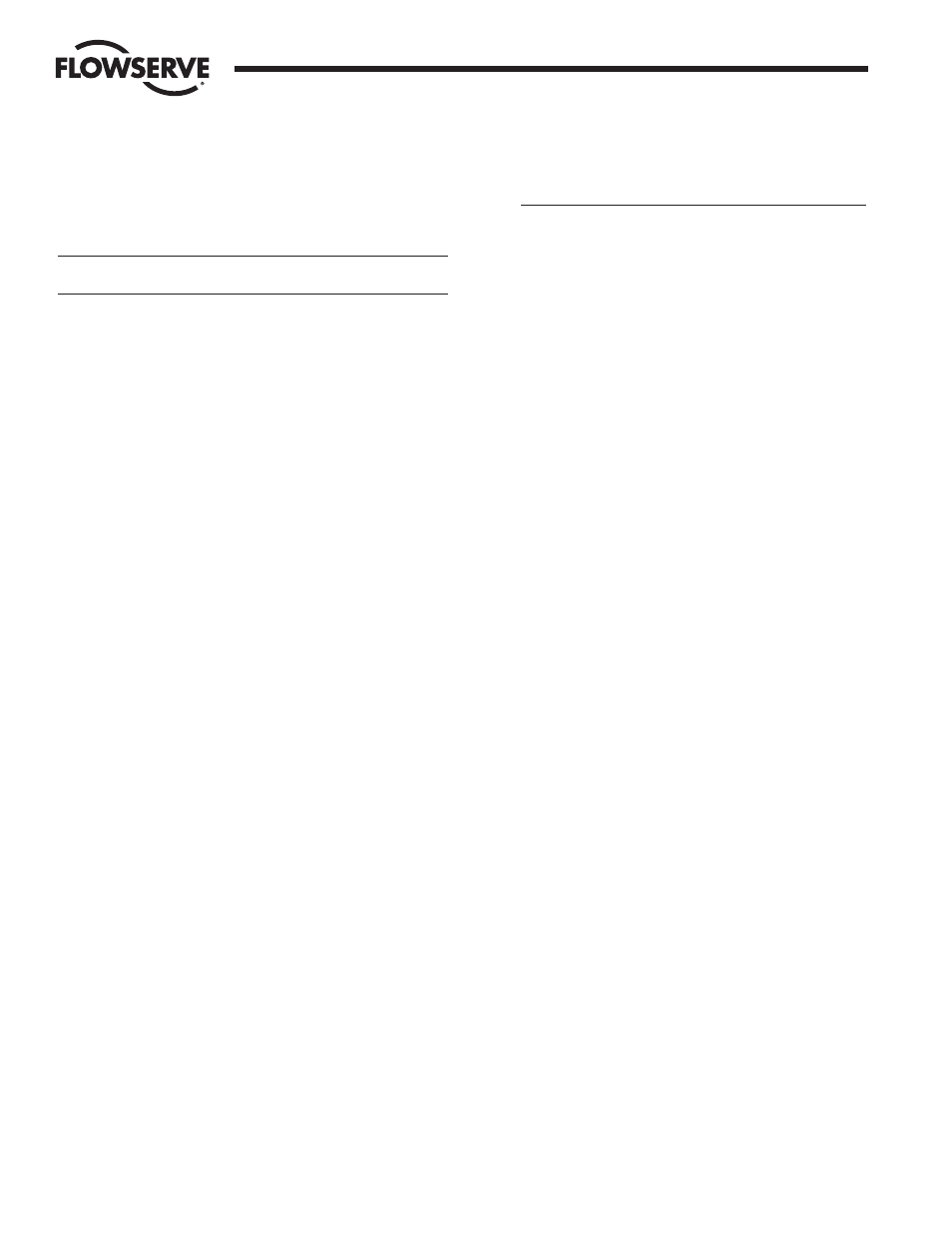
4
Electri-SAFE DataFlo Digital Electronic Positioner
FCD WCAIM2048-01
Flow Control
Worcester Controls
3.0 Wiring of Electri-SAFE Digital
Positioner and Actuator
See wiring diagrams located under positioner and actuator covers and
in figures 4, 5 and 6 in the appendix for customer connections.
CAUTION: Wiring should be inserted only to midpoint of terminal
strip.
3.1 Actuator Wiring
An Actuator Electrical System is made up of two major
components involved in user connections:
1) Actuator
housing
2) Positioner
housing
Incoming power is brought to the Electri-SAFE unit via the
Actuator Housing.
Signal wiring is brought to the Electri-SAFE unit via the Positioner
Housing.
The positioner input power, pump motor and solenoid control
signals (and wires for optional indicating switches) are factory-
wired to the actuator housing terminals (figure 6 in the appendix)
and wired to meet Class-1, Div-1 requirements.
1) The actuator housing contains the CCW over-travel limit
switch, and wiring for the motor, control and fail-safe
solenoid valves. All of the high-voltage input wiring is
connected here.
2) The positioner housing contains the Digital Positioner Board,
power supply, position potentiometer, terminal strips, and
optional indicating switches. Figure 7 in the appendix defines
the location of major electronic components in the positioner
housing. The power supply is factory wired to terminal strip
1-10 (see Figure 4 in the appendix). Wiring from the
positioner terminal strip 1-10 to the actuator terminal strip
1-8 is factory-wired. Signal wiring is brought from the
positioner board to terminal strip A-H in the positioner
housing (see Figure 5 in the appendix).
All field signal connections are at terminal strip A-H in the
positioner housing (see Figure 5 in the appendix).
NOTE: IT SHOULD BE NOTED THAT INSTALLING THIS
ACTUATOR IN A HAZARDOUS AREA REQUIRES THE USE OF
CONDUIT AND SEALS AND OTHER REQUIREMENTS AS
SPECIFIED IN THE NATIONAL ELECTRICAL CODE,
CHAPTER 5.
3.1.1 Minimum Fuse Ratings
See table on this page for minimum fuse rating when over-
current protection is used in motor power circuit.
NOTE: This table shows the minimum rating to prevent inrush
current from blowing the fuse.
Actuator Size
Voltage
Fuse Rating
15-72
120 VAC
10 A
20-72
120 VAC
10 A
3.1.2 Wiring and Installation of Accessories
Refer to installation and wiring instructions, contained in Part
6.0 of this manual and/or respective accessory kit.
4.0 Positioner – General Description
and Modes of Operation
When properly adjusted, the actuator will stop at the full CCW and full
CW positions as a result of having reached one of the respective
limits of the input signal span. The full CCW over-travel limit switch
will be used only as a backup to stop the actuator pump motor should
a failure of an electronic component occur.
4.1 Programming Switches (Key Functions)
There are three switches (keys) on the positioner circuit board
which are labeled SEL (black) for select, DN (white) for down, and
UP (white) for up. These are the keys that are used to calibrate,
program and position the Digital Positioner Board locally.
The UP and the DN switches can be used to advance through the
menu until the desired parameter is reached. At this time, the
display will be flashing between the parameter name and its
current setting. Momentarily pressing the SEL switch will lock in
that parameter’s current setting and allow the user to change it. If
the display is alphabetic such as riSE or FALL for setpoint
direction, momentarily pressing the UP switch will cycle through
the setting options for that parameter. When the desired setting
option is reached, momentarily pressing the SEL switch will set
the parameter to that option and store it in nonvolatile memory. If
the display is numeric, momentarily pressing the SEL switch will
lock in the value with the left most digit flashing. Pressing the UP
switch will increment this digit. Pressing the DN switch will
advance the flashing digit to the next digit to the right. Therefore,
the UP switch is used to set the flashing digit to the desired value
while the DN switch is used to select the flashing digit. Once the
overall value is entered, momentarily press the SEL switch to
store the value in nonvolatile memory.
4.2 Limit Switch Adjustment and Calibration Procedures
4.2.1 Adjustment of Over-Travel Limit Switch
The Positioner has been shipped with a limit switch factory-
calibrated to stop the actuator in the full CCW position
(approximately 92°). It is located in the actuator housing,
behind the flat cover. If it has been determined that the limit
switch requires adjustment, perform the adjustment as
follows: