Worcester controls – Flowserve Worcester Controls Electri-SAFE DataFlo User Manual
Page 9
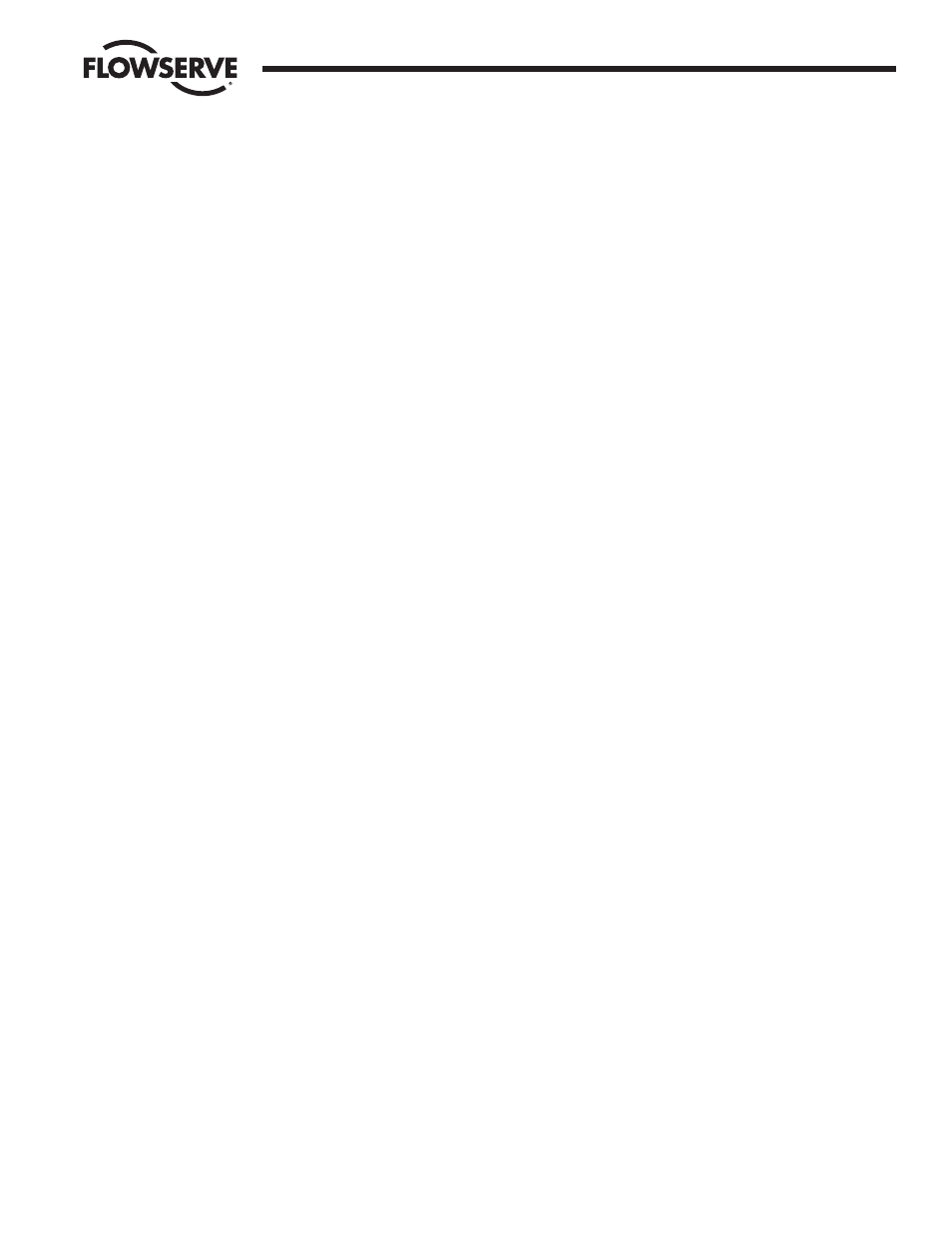
FCD WCAIM2048-01
Electri-SAFE DataFlo Digital Electronic Positioner
9
Flow Control
Worcester Controls
4.4.5 Setpoint Direction (Rise/Fall)
The display will alternately display Sdir and either riSE or
FALL.
Use the UP or DOWN switches to select riSE or FALL.
riSE selects direct acting positioner control where the actuator
rotates in the CCW direction as the setpoint signal increases.
The valve is full CW at the minimum setpoint signal value.
FALL selects reverse acting positioner control where the
actuator rotates in the CCW direction as the setpoint signal
decreases. The valve is full CCW at the minimum setpoint
signal value and full CW at the maximum setpoint signal value.
4.4.6 Setpoint Split Range START Selection
The display will alternately display SPrS and its value.
For a direct-acting positioner, SPrS specifies the START of the
split range input signal for the full CW actuator position, and
must be less than SPrE. For a reverse-acting positioner, SPrS
specifies the START of the split range input signal for the full
CCW actuator position, and must be less than SPrE.
The setting can be anywhere from 0.0 to 99.9% of the input
signal range in 0.1% increments.
Split ranging is useful when more than one valve is used in a
control system. As an example, one actuator can be calibrated
to open for an input signal between 4-12 mA and another to
open for an input signal between 12 and 20 mA.
4.4.7 Setpoint Split Range END Selection
The display will alternately display SPrE and its value.
For a direct-acting positioner, SPrE specifies the END of the
split range input signal for the full CCW actuator position, and
must be greater than SPrS. For a reverse-acting positioner,
SPrE specifies the END of the split range input signal for the
full CW actuator position, and must be less than SPrS.
The setting can be anywhere from 0.1 to 100.0% of the input
signal range in 0.1% increments.
4.4.8 Setpoint Ramp-Time to Open
The display alternately displays OPEn and the selected time to
open.
Times from 0 to 200 seconds can be selected as the time for
the actuator to travel from the full-closed (CW) to the full-
open (CCW) position.
If “0” (or a time less than the CCW travel time) is selected,
the rate of response to a step change in the input signal will
be as fast as the valve actuator can operate. The slowest time
to open is 200 seconds.
4.4.9 Setpoint Ramp-Time to Close
The display alternately displays CLOS and the selected time to
close.
Times from 0 to 200 seconds can be selected as the time for
the actuator to travel from the full-open (CCW) to the full-
closed (CW) position.
If “0” (or a time less than the CW travel time) is selected, the
rate of response to a step change in the input signal will be as
fast as the valve actuator can operate. The slowest time to
close that can be selected is 200 seconds.
4.4.10 Setpoint Curve Function
The positioner translates the setpoint input using a table of
values. The positioner contains a linear table and four 21-
point curves called free curves. By default, the linear
translation table is used (SFn is set to Lin). The four free
curve tables can be edited to allow different translation curves
to be used. By default, free curve #1 (FrE1) is preset to a 1:25
equal percentage response curve, free curve #2 (FrE2) is
preset to 1:50 equal percentage response curve, and free
curves #3 and #4 (FrE3 and FrE4) are each preset to a linear
response curve. All four free curves can be modified. The
table on the next page shows all the tables and the default
free curve values. These values are loaded any time the
parameters are defaulted with the PrSt parameter.
NOTE: Definition of equal percentage: for equal increments of
valve rotation, the C
v
increases by a given percentage over
what it was at the previous setpoint.
The display will alternately display SFc and either Lin or FrE1,
FrE2, FrE3, or FrE4.
This function tells the positioner the desired shaft positioning
characteristic with respect to input signal.
Lin causes the shaft position to vary in a linear fashion as
the input signal changes (i.e., if the signal is at 50 percent,
the shaft position will be at 50 percent of the selected
operating range).
The FrE1-FrE4 curves allow 21 setpoint vertices to be set. In
this way, a custom shaft positioning characteristic can be
entered. There is a vertices set (data point) at 4 mA and then
every 0.8 mA up to and including 20 mA. The vertices are
displayed as SL 0 to SL 20 and will only be displayed when
one of the FrE1-FrE4 curves is chosen as the setting. The SL
parameters can be found in the menu between the PrSt
parameter and the CodE parameter. Use the UP and DOWN
switches to select and change the vertices settings.