Worcester controls – Flowserve Worcester Controls Electri-SAFE DataFlo User Manual
Page 15
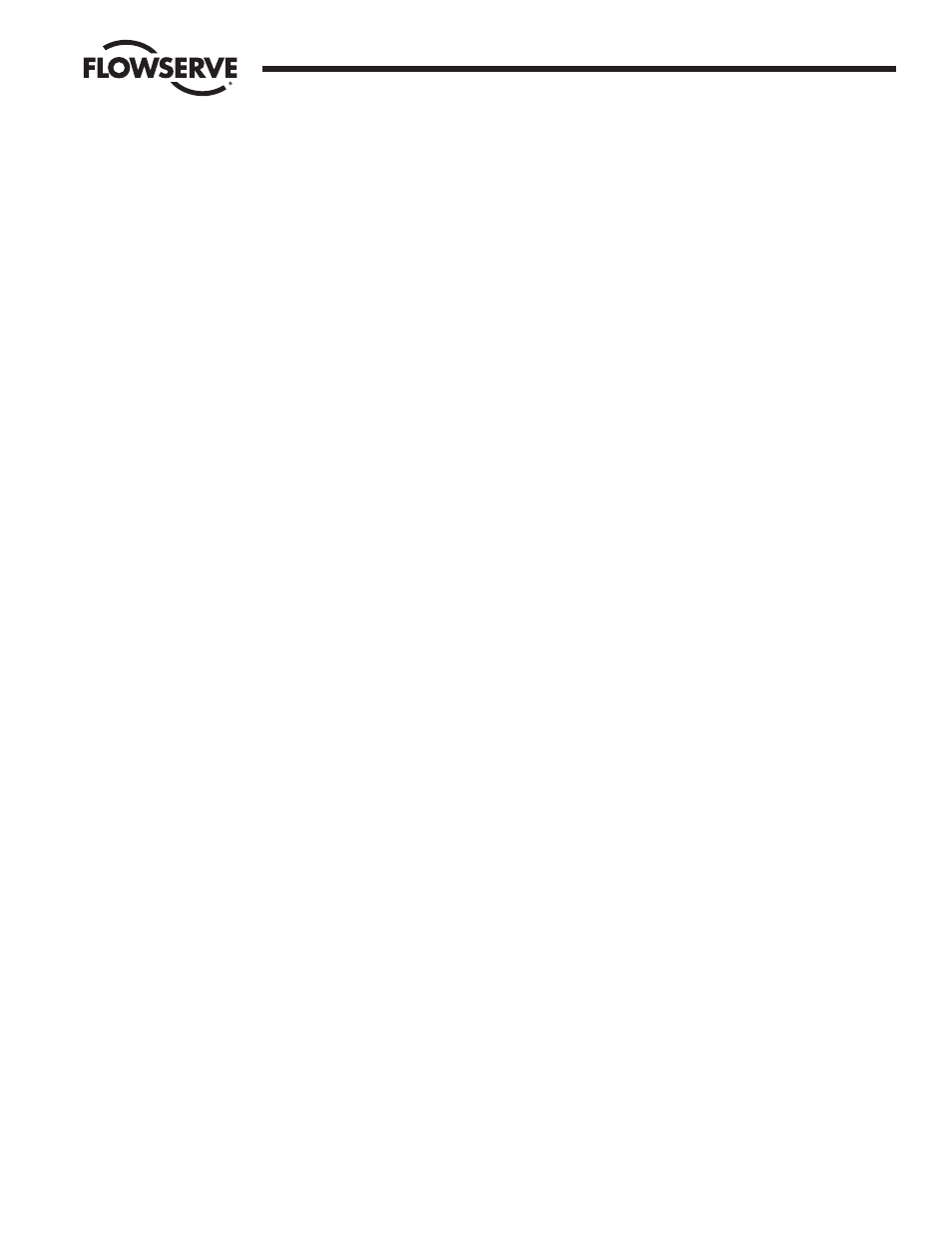
FCD WCAIM2048-01
Electri-SAFE DataFlo Digital Electronic Positioner
15
Flow Control
Worcester Controls
The communication software has been factory-set to default
to communication port-1 “com-1” but can be reset to
communication ports 2, 3, or 4 if required, as shown using
Windows 98 in the following steps. The software baud rate
has been factory set to 38,400 bps to agree with the
positioner factory setting and can also be changed as follows.
After creating a directory and installing the software in your
computer, perform the following:
a) In Explorer, select the Electri-Safe communications
software folder and open it.
b) Select the “ICP.EXE” file, right mouse click and select
“create shortcut” and drag the shortcut to your desktop.
c) Right mouse click on the communication Icon shortcut on
your desktop and select properties.
d) On the properties screen select program and the
“command line” should show the path ending in “EXE”.
e) To change the default baud rate and communication
path—as an example—enter the following.
Change baud rate to 19,200 bps.
Change communication port to port-2.
After “EXE” in the command line, insert a space and enter
19200, insert another space and enter 2.
The command line path should look like the following,
using your directory name.
C:\ directory \ ICP.EXE 19200 2
Note: The baud rate in the positioner has to match the
baud rate set in the software command line.
4.9.5 Monitor Display
Once the program has been started, the following screen will
appear (see Figure 1 on following page):
The program will start up looking for address 1. If that unit
exists, communications are established. Otherwise, to
establish communications with the positioner, tap the space
bar. The cursor to the right of the arrow next to the address
parameter will begin flashing. Type in the positioner address
and then hit the enter key (factory default is 1). The words
Reading data… will appear to the right of the arrow. In about
two seconds the screen will fill with the positioner data. The
arrow just to the left of the Status area indicates whether the
positioner is under control of the analog signal or under the
control of the computer (PC). The F4 key toggles between
computer and analog control of the positioner.
The PC Cmd value in the Status area is the position output of
the computer. This value can be changed with the left and
right cursor keys but will only control position when the F4
key toggles to PC Cmd. Position can also be changed by
pressing F12, entering the desired position on the numeric
keypad and then pressing the enter key.
Input is the value of the analog signal being received by the
positioner board and controls position only when the F4 key
toggles to Input.
Output is the value of the 4-20 mA output signal for shaft
position feedback (when this option is installed). Shaft Pos is
the actual readout of the actuator shaft position in percent of
shaft travel.
DB Run is the current setting for positioner deadband. When
shaft motion stops, shaft position should always be within the
deadband of the position command signal.
The Alarms are Over, Under, and Dev (Deviate). The area
immediately under one of these alarms will light up if that
alarm condition exists. The alarms are defined as follows:
Over – Shaft position is greater than the value set in the Over-
travel Alarm.
Under – Shaft position is less than the value set in the Under-
travel Alarm.
Dev – Shaft has not reached position called for by signal
within the time specified by Deviation Alarm.
The Calibration Data is a listing of the stroke times measured
during calibration.
The listings under Ver x.xx are the keys required to control the
screen and the positioner.
F2 – Load a file of all parameters including curve data from
the hard drive and download it to the positioner (about 40
seconds).
F3 – Save the data in the positioner to a file on the hard drive
(about 20 seconds).
F4 – Toggle control of the positioner between the analog
signal and the computer.
F9 – Enter the positioner response curve edit screen.
F10 – Enter the positioner ASCII EEPROM edit screen.
(Customer information for this unit)
F12 – Enter desired position on numeric keypad then press
enter.
[Right Arrow] – Increment the PC Cmd position output signal.
[Left Arrow] – Decrement the PC Cmd position output signal.
Alt-x – Exit the ICP program and return to DOS or Windows.