0 description of positioner – Flowserve Worcester Controls Electri-SAFE DataFlo User Manual
Page 3
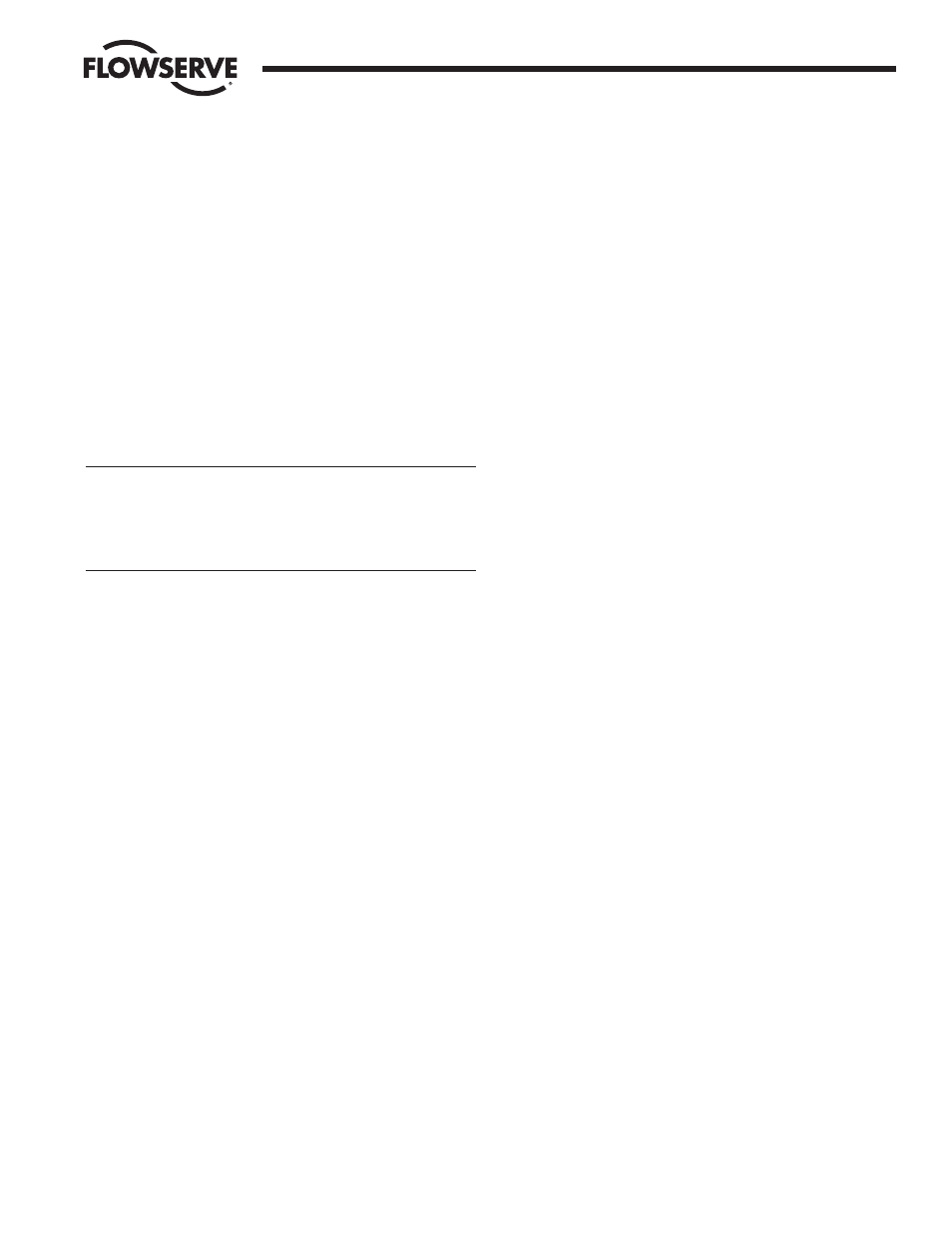
FCD WCAIM2048-01
Electri-SAFE DataFlo Digital Electronic Positioner
3
Flow Control
Worcester Controls
1.0 Description of Positioner
The Worcester/McCANNA Electri-SAFE DataFlo Digital Electronic
Positioner was designed for use with the Worcester/McCANNA Series
72 Electri-SAFE Hydraulic Actuators only.
This Electri-SAFE DataFlo Digital Electronic Positioner provides
positioning of the Series 72 electro-hydraulic actuator for partial
opening of the valve. The positioner operates by receiving a signal
from a remote source to open the actuator to a particular position. A
feedback loop is designed into the electronic board to keep the
actuator at the required position. A resistance potentiometer and gear
are attached to the output shaft to provide accurate position feedback.
A change in the remote input signal will cause the actuator to open or
close to meet the new desired position.
Three switches (keys) are located on the positioner circuit board to
allow for manual operation of the positioner, calibration, function
programming of the microchip, and troubleshooting.
CAUTION: The Electri-SAFE DataFlo Digital Electronic Positioner is
sensitive to electrical noise on signal or supply lines and in the
environment. For maximum positioner sensitivity, the electrical
noise level should be as low as possible. Follow installation,
calibration and adjustment guidelines carefully and use shielded
wire for all low-voltage signals.
The Digital Positioner board is designed to receive a floating current
input signal. This allows several pieces of equipment to be operated
from the same current loop while at the same time remaining
electrically independent of each other. A floating input signal means
that the current input signal should not be referenced to the circuit
board ground. The board power source must have a ground
independent from that of the signal source.
The Digital Positioner board standard setup is 4 mA for full clockwise
rotation (0°) and 20 mA for full counterclockwise rotation (90°).
The 4-20 mA signal input circuit for the Digital Positioner boards is
protected with a 62 mA fuse (F1). The fuse is used to protect the input
circuit from an excessively high voltage. The fuse used in the input
circuit is a Littlefuse PICO II very fast-acting fuse rated at 62 mA.
Quite often when we receive an actuator for repair at Flowserve, we
find that the only thing wrong with the unit is that the feedback
potentiometer is out of calibration. It is very important that the
feedback potentiometer be properly calibrated for correct operation of
the positioner board. Whenever you have a problem with the
positioner calibration, always check the feedback potentiometer
calibration first. This must be done with no power applied to the
circuit board. If the actuator is in the full clockwise position, check the
resistance between the purple and white/black potentiometer leads.
The reading should be 80-90 ohms. If it is not, rotate the face gear
until the proper reading is achieved. If the actuator happens to be in
the full counterclockwise position then check the resistance between
the green and white/black potentiometer leads. If necessary adjust the
face gear for an 80-90 ohm reading.
NOTE: It is not necessary to loosen or remove face gear snap ring to
rotate gear—it is a friction fit. If for any reason the snap ring is to be
removed, do not over-stretch it; use the minimum opening to allow it
to slip over the gear.
2.0 Features of the Electri-SAFE
Electronic Positioner
Circuit Board
2.1 General
Figure 7 in the appendix defines the location of major electrical
components in the positioner housing. The Digital Positioner
Board is factory wired to the terminal strips per Figure 4 and
Figure 5 in the appendix.
The feedback potentiometer leads are factory connected to the
terminal block (TB2) on the Digital Positioner Board.
If a dual potentiometer option is installed, the “B” potentiometer
leads will have to be wired directly to external device. The “A”
potentiometer leads are factory connected to the terminal block
(TB2) on the Digital Positioner Board. Also, note that the “B”
potentiometer has a voltage limit of 30 volts maximum.
2.2 Circuit Board Configurations
The positioner board is factory supplied for one of the seven input
signal options plus a two-wire RS-485 interface.
NOTE: Field changes to the positioner board are not advised.
Consult Flowserve before attempting any modification.
2.3 LED Indicators
Light emitting diodes (LED) marked LD1 (CW) (see Figure 2 in
the appendix) and LD2 (CCW) mounted on the power supply (are
in the output circuits) and when lit indicate which direction the
actuator is trying to drive to. A third LED, LD3 (see Figure 1 in the
appendix), is used to indicate when an alarm condition exists. If
LD3 is lit, the alarm that caused it to light must be determined by
looking at the LCD on the circuit board and finding the alarm
parameter with the UP or DN switch.
2.4 Controls (Override)
There are no adjustable controls provided on the circuit board,
because none are necessary. All parameters are set through the
programming switches (keys) or the RS485 interface. Local push-
button control is provided at the controller by simultaneously
pressing the SEL and UP switches (keys) for three seconds. At
this point the UP and the DN switches (keys) can be used to
manually rotate the actuator shaft. Pressing the SEL switch for
three seconds will return the positioner to the run mode.
2.5 AC Power Control
The AC output circuits are controlled by solid state switches
(triacs Q3, Q4), which will provide trouble-free operation for the
life of the equipment they are used with, AS LONG AS THEY ARE
OPERATED WITHIN THEIR RATINGS.