Worcester actuation systems – Flowserve DFP17 User Manual
Page 13
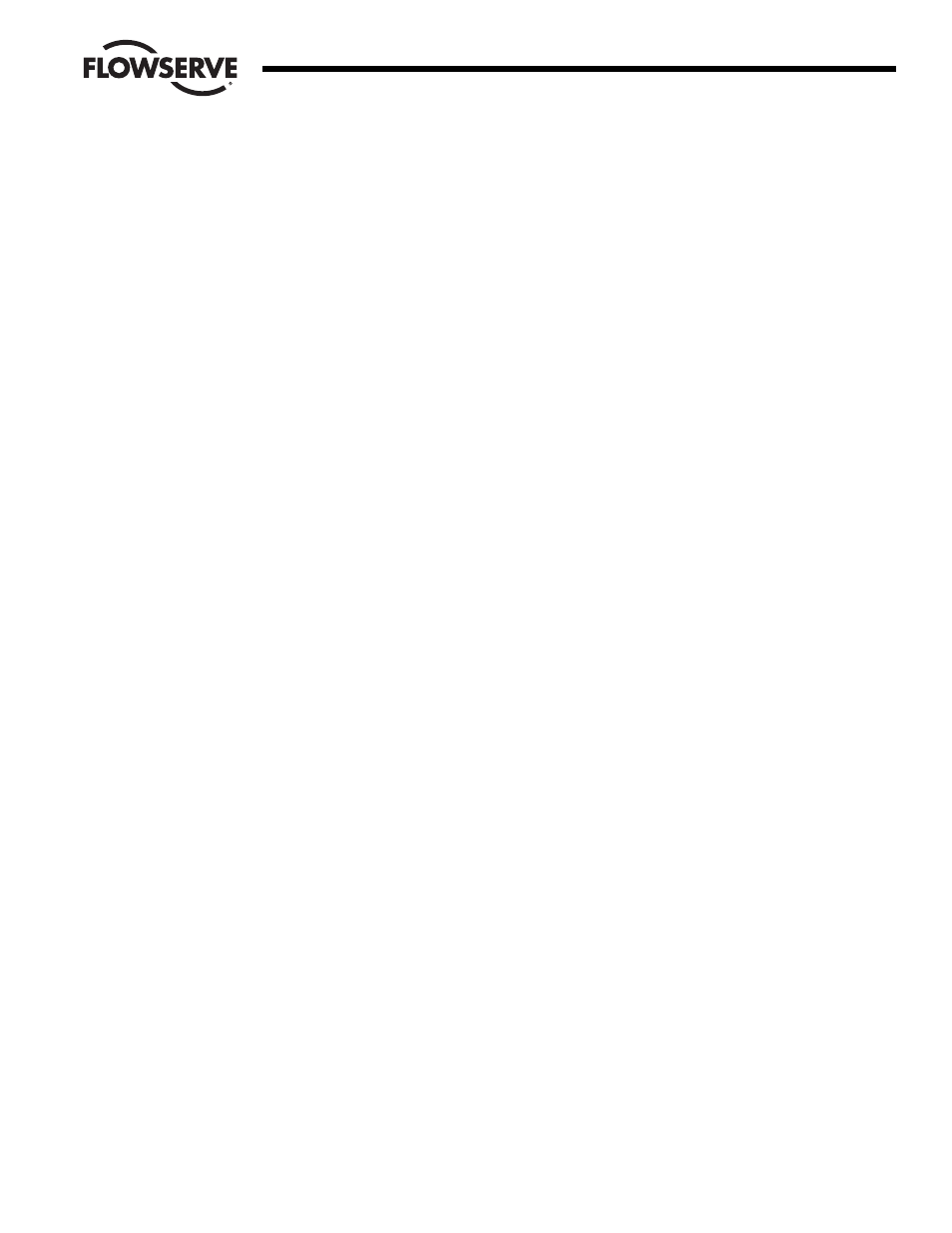
WCAIM2037
DataFlo Digital Electronic Positioner DFP17 Installation, Operation and Maintenance Instructions
13
K. The display will now read a new feedback voltage,
approximately 4 volts. Press and release the SEL key.
L. The display will now flash CAPo and no. Press and
release the UP key. The display will now flash between
CASE and no.
M. Press and release the SEL key and the display will read
SEC and read a voltage between 0 and 5 volts. Set your
input to 4 mA. (The actuator will not move.) The display
will read approximately .8 volts. Press and release the
SEL key.
N. The display will flash between SECC and your set voltage.
Apply 20 mA to your signal input. The display should
read approximately 4 volts. Press and release the SEL
key.
O. The display will now flash between CASE and no again.
Press and release the UP key once. The display will now
flash between CACY and no.
P. Press and release the SEL key once and the display will
flash posn and then Close and the actuator will cycle
close then the display will read open and the actuator will
cycle open. The unit is measuring its cycle time. When
the cycling is done the display will flash CASY and no
again.
Q. The calibration is now complete. Press and hold the SEL
key for three seconds and the positioner will revert back
to the normal run mode and will respond to input signal.
4.1.3 Initial Setup and Adjustments
When properly adjusted, the actuator will stop at the full
open and full closed points as a result of having reached
one of the limits of the input signal span, and the
actuator’s limit switches will be used only in a backup
mode to stop the actuator, should an electronic
component failure occur. The switch cams should be set
2° beyond the normal end of travel.
For the Series 75, 240 VAC Actuator with a 240 VAC
Digital Positioner, the two limit switches do not limit
actuator travel in the event of a component failure, they
are used to switch off the optocouplers (U1, U2) outputs
at the end of CW and CCW strokes instead of directly
switching off the motor. This protects the triacs (Q3, Q4)
by ensuring that they are switched off via their gate
circuit and do not shut off on full power.
a
CAUTION: Do not manually position the actuator
shaft beyond where the limit switches would have
stopped shaft travel.
Actuators with factory mounted positioners will be
shipped with their limit switches properly adjusted to trip
at 13 degrees AFTER the positioner electronics would
normally have shut the actuator off upon reaching the
upper or lower input signal limit.
4.2 General Description of the Digital Positioner
The digital positioner will be used for intelligent control and operation
of an electric valve actuator.
4.2.1 Valve Position Setpoint Input
The valve position setpoint input signal is derived from
either an analog input signal or from a digital RS485
serial input.
4.2.2 Valve Position Feedback
Valve position feedback to the digital positioner board is
from the 1000 ohm potentiometer geared to the actuator
shaft.
IMPORTANT: The feedback potentiometer is calibrated for
only one 90° quadrant of valve operation If the output
shaft is repositioned to another 90° quadrant or if the
output shaft is rotated a multiple of 360° from its original
position, the feedback potentiometer will no longer be in
calibration and must be recalibrated. See sections C and
D of part 1.1.
The Series 75 actuators offer a manual override feature.
Whenever repositioning the valve using the manual
override capability on these actuators, move the valve
only within the 90° quadrant for which the feedback
potentiometer has been calibrated.
4.2.3
Key Features of the Digital Positioner
• Easy push-button calibration of the positioner
• Programmable set-point direction
• Microprocessor-based positioner
• Programmable split range
• High resolution
• Programmable deadband as well as auto adjust
• Cycle count
• Programmable operating parameters
• High, low and deviation alarms
• Four programmable position response curves
• Loss of signal position and time delay
• Local and remote positioner operation
• Loss of power position and time delay
• Electronic travel limits
• ASCII text area in EEPROM (420+ bytes)
Flow Control
Worcester Actuation Systems