Worcester actuation systems – Flowserve DFP17 User Manual
Page 22
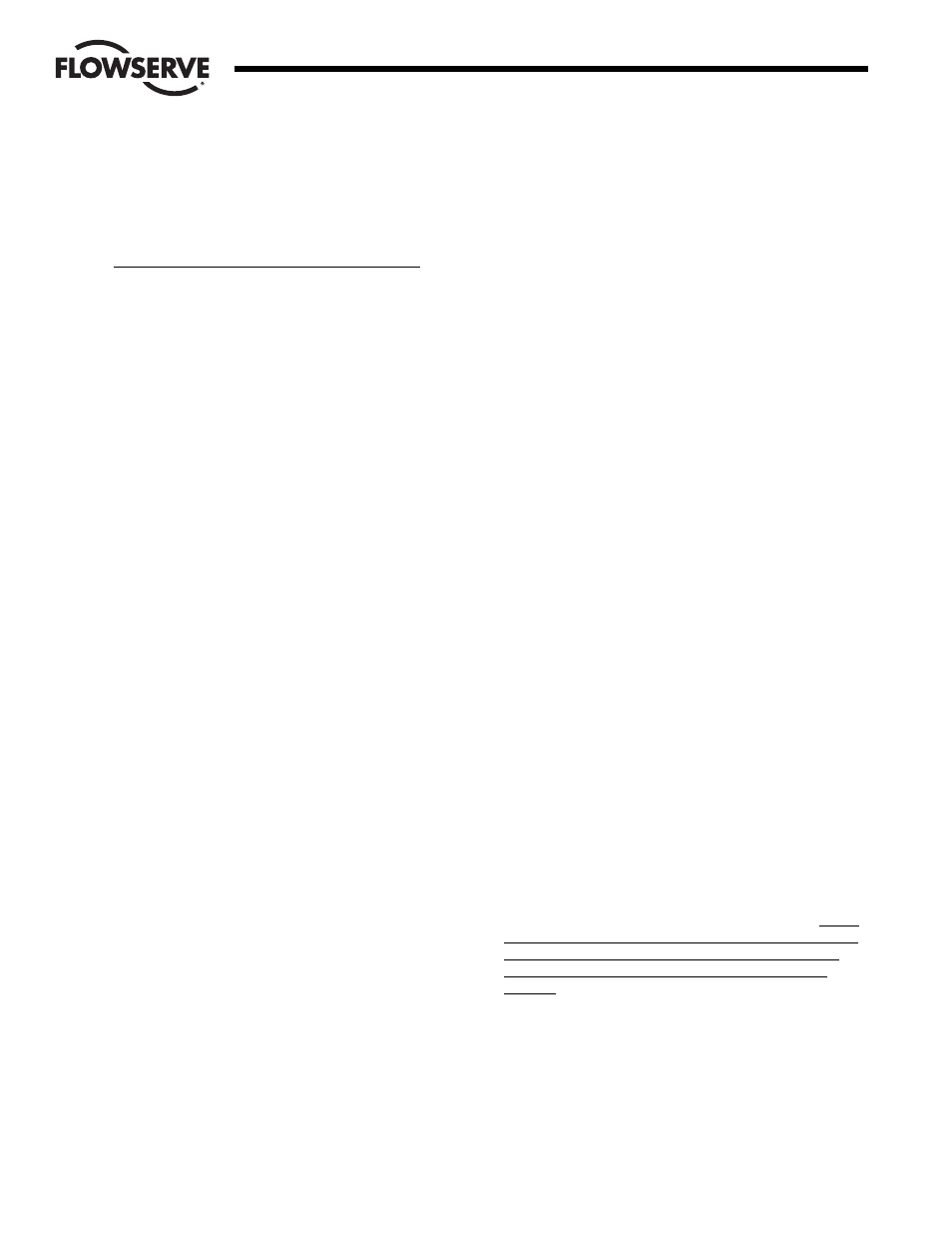
22
DataFlo Digital Electronic Positioner DFP17 Installation, Operation and Maintenance Instructions
WCAIM2037
The 21-point FrE3 and FrE4 curves are set to the following
values when the factory default parameters are loaded
(linear curve):
NOTE: When installed on standard round port valves, these
curves will produce equal percentage flow characteristics.
Parameter
Value
SL 0
0%
SL 1
5%
SL 2
10%
SL 3
15%
SL 4
20%
SL 5
25%
SL 6
30%
SL 7
35%
SL 8
40%
SL 9
45%
SL 10
50%
SL 11
55%
SL 12
60%
SL 13
65%
SL 14
70%
SL 15
75%
SL 16
80%
SL 17
85%
SL 18
90%
SL 19
95%
SL 20
100%
4.8 Calibrating And Programming The Digital Positioner
4.8.1 Programming Switches
There are three switches on the circuit board which are
labeled SEL for select, DN for down, and UP for up.
These are the switches which are used to calibrate and
program the Digital Positioner Board locally.
4.8.2 Programming the Positioner Board
In order to program the positioner board, it is necessary
to enter the programming mode. It is also necessary to
enter the correct security code when asked to do so
before any parameters can be changed. To program one
of the parameters, follow this procedure:
1. Press the SEL switch for about three seconds until the
display shows Pro9 for two seconds and then begins
flashing between CodE and 0000.
2. At this time enter the correct securtiy code as
described in section 4.3.1. When the correct code
is entered, the display will begin flashing between
Addr and some number from 1 to 255. This number is
the address to which the unit has been set. The
positioner is now in the programming mode.
3. At this point, the UP and the DN switches can be used
to advance through the menu until the desired
parameter is reached. At this time, the display will be
flashing between the parameter name and its current
setting. Momentarily pressing the SEL switch will lock
in that parameter’s current setting and allow the user
to change it. If the display is alphabetic such as riSE
or FALL for setpoint direction, momentarily pressing
the UP switch will cycle through the setting options
for that parameter. When the desired setting option is
reached, momentarily pressing the SEL switch will set
the parameter to that option and store it in non-
volatile memory. If the display is numeric,
momentarily pressing the SEL switch will lock in the
value with the left most digit flashing. Pressing the UP
switch will increment this digit. Pressing the DN
switch will advance the flashing digit to the next digit
to the right. Therefore, the UP switch is used to set
the flashing digit to the desired value while the DN
switch is used to select the flashing digit. Once the
overall value is entered, momentarily press the SEL
switch to store the value in non-volatile memory.
4. To restore all the parameters to the factory default
settings as listed in section 4.7, advance to the PrSt
parameter, momentarily press the SEL switch, and
then momentarily press the UP switch. The display
will show yES for several seconds and then again
begin flashing between PrSt and no. The factory
defaults are now installed.
4.8.3 Programming the FrE1, FrE2, FrE3, and FrE4 Curves
There are a total of five curves programmed into the
positioner. These consist of one Lin (linear—not
programmable) curve and four FrE (programmable)
curves. The linear curve is not programmable and is
labeled Lin. The other four curves are labeled FrE1, FrE2,
Fre3, and FrE4. FrE1 and FrE2 are set to 1:25 and 1:50
equal percentage curves respectively as factory defaults.
FrE3 and FrE4 are both set to a linear curve as factory
defaults. FrE1 through FrE4 are each programmable. To
program a curve, it is first necessary to enter the
program mode and then select the FrE curve the user
wishes to edit. When a FrE curve is selected in the main
menu the SL0 SL20 parameters become available
following the PrSt parameter.
4.9 RS-485 Communications
The Digital Positioner Board may be connected to a computer or
PLC via an RS-485 two-wire serial bus. Unless the computer has
an RS-485 port built in, it will be necessary to use an RS-232 to
RS-485 Converter on one of the computer’s serial ports. If there
will be more than one positioner on the serial bus, all positioner
boards except for the last one on the bus must have the 120
ohm terminator resistor removed (see figure 2 for resistor
location). The terminator resistor is in socket pins. The
positioners should be connected to the RS-485 bus in a daisy
chain fashion.
a
CAUTION: Do not connect two units with the same address
to the same RS-485 bus.
Flow Control
Worcester Actuation Systems