Worcester actuation systems – Flowserve DFP17 User Manual
Page 19
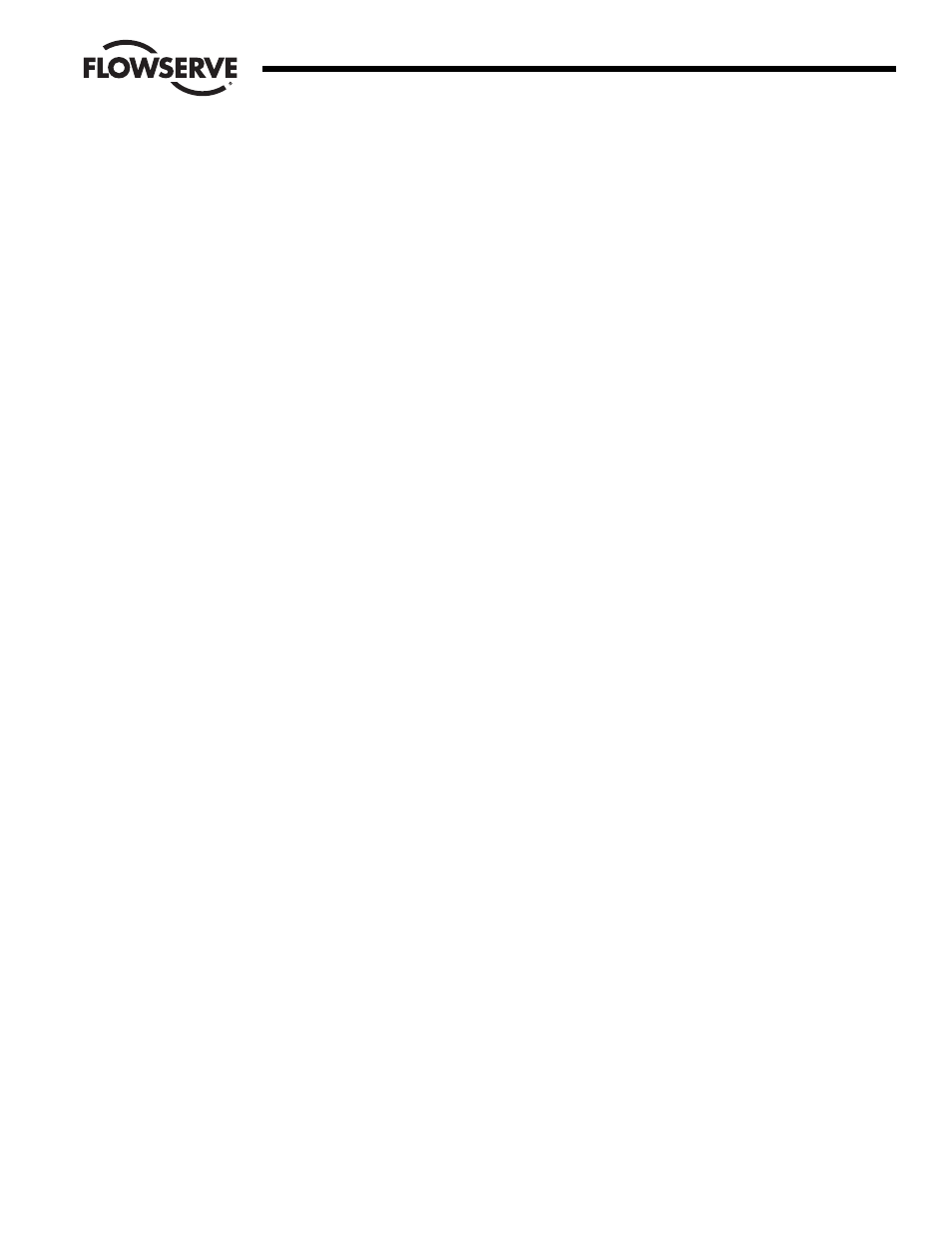
WCAIM2037
DataFlo Digital Electronic Positioner DFP17 Installation, Operation and Maintenance Instructions
19
5. The display will alternate between SEtU and the
voltage resulting from the current signal.
6. To edit, simultaneously press and release SEL and UP
switches then: Adjust the signal source to produce the
higher input reading, e.g., a 20 mA signal. Press the
SEL switch to lock in the full CCW input reading.
Control returns to the Calibration Menu.
B. Position Endpoint Calibration
1. Use the DOWN switch to go to PoC.
2. The display will alternate between PoC and the
feedback voltage value.
3. To edit, simultaneously press and release SEL and UP
switches, then use either the UP or DOWN switches to
manually rotate the actuator to its full CW position.
With the actuator in the full CW position, adjust the
feedback potentiometer for a reading between .200
and .400 volts. Press the SEL switch to lock in the full
CW feedback reading. Control returns to the
Calibration Menu.
4. Use the DOWN switch to go to PoCC.
5. The display will alternate between PoCC and the
feedback voltage value.
6. To edit, simultaneously press and release SEL and UP
switches then: Use the UP switch to manually rotate
the actuator to its full CCW position. If the shaft
rotates too far, use the DOWN switch to bring the
shaft back to the full CCW position. Press the SEL
switch to lock in the full CCW feedback reading.
Control returns to the Calibration menu.
C. Cycle Time Calibration
NOTE: THIS PROCEDURE SHOULD ONLY BE
PERFORMED AFTER A VALID POSITION ENDPOINT
CALIBRATION PROCEDURE HAS BEEN COMPLETED.
1. Use the DOWN switch to go to Cyt.
2. The display will alternate between Cyt and a cycle time
reading.
3. Simultaneously press and release SEL and UP
switches.
If this is selected, the actuator will first go to the fully
CCW position (if is not already there).
The display will than show PoC and the actuator will
travel to the full CW (closed) position and record the
travel time. At that point, the CW time measurement
will begin.
The display will then show PoCC and the actuator will
travel the full CCW (open) position and record the
travel time. At that point, the cycle time calibration is
complete and control returns to the calibration menu.
4.5.2 For Microchip U5 (AC board) or U3 (DC board) Rev.
V2.11 and older only:
Calibration mode is entered from the Run Mode the same
as the program and Local Modes.
The Calibration Mode has three procedures. Any one or
all of the three procedures may be performed. The
procedures are: Position Endpoint Calibration, Input
Signal Calibration, and Cycle Time Measurement. They
are each described separately below.
When first entering the Calibration Mode, the display will
show CAL for one second then will begin alternating
between CodE and 0000. Enter the security code as
described earlier in sections 4.3.1.B. and 4.2.6. After the
code is correctly entered, press the SEL switch to accept
code. A series of menu selections allows the user to pick
which calibration procedures they wish to perform.
After entering the correct security code, the display will
alternate between CAPo and no. This is the menu for the
calibrate position procedure. Pressing the SEL switch will
enter the position endpoint calibration procedure, or
pressing the UP or DOWN switches will select another
procedure.
The menu for entering the input signal calibration
procedure is shown with a display that alternates
between CASE and no. Pressing the SEL switch will enter
the setpoint input calibration procedure, or pressing the
UP or DOWN switches will select another procedure.
The menu for entering the cycle time calibration
procedure is shown with a display that alternates
between CACy and no. Pressing the SEL switch will start
the cycle time calibration procedure, or pressing the UP
or DOWN switches will select another procedure.
A.
Position Endpoint Calibration
1. The display will alternate between PoC and the
feedback voltage value.
2. Full CW position feedback reading:
Use either the UP or DOWN switches to manually
rotate the actuator to its full CW position.
With the actuator in the full CW position, adjust the
feedback potentiometer for a reading between .200
and .400 volts.
Press the SEL switch to lock in the full CW feedback
reading.
After the full CW feedback value has been recorded,
control sequences to the next screen.
3. The display will alternate between PoCC and the
feedback voltage value.
Flow Control
Worcester Actuation Systems