Worcester actuation systems – Flowserve DFP17 User Manual
Page 23
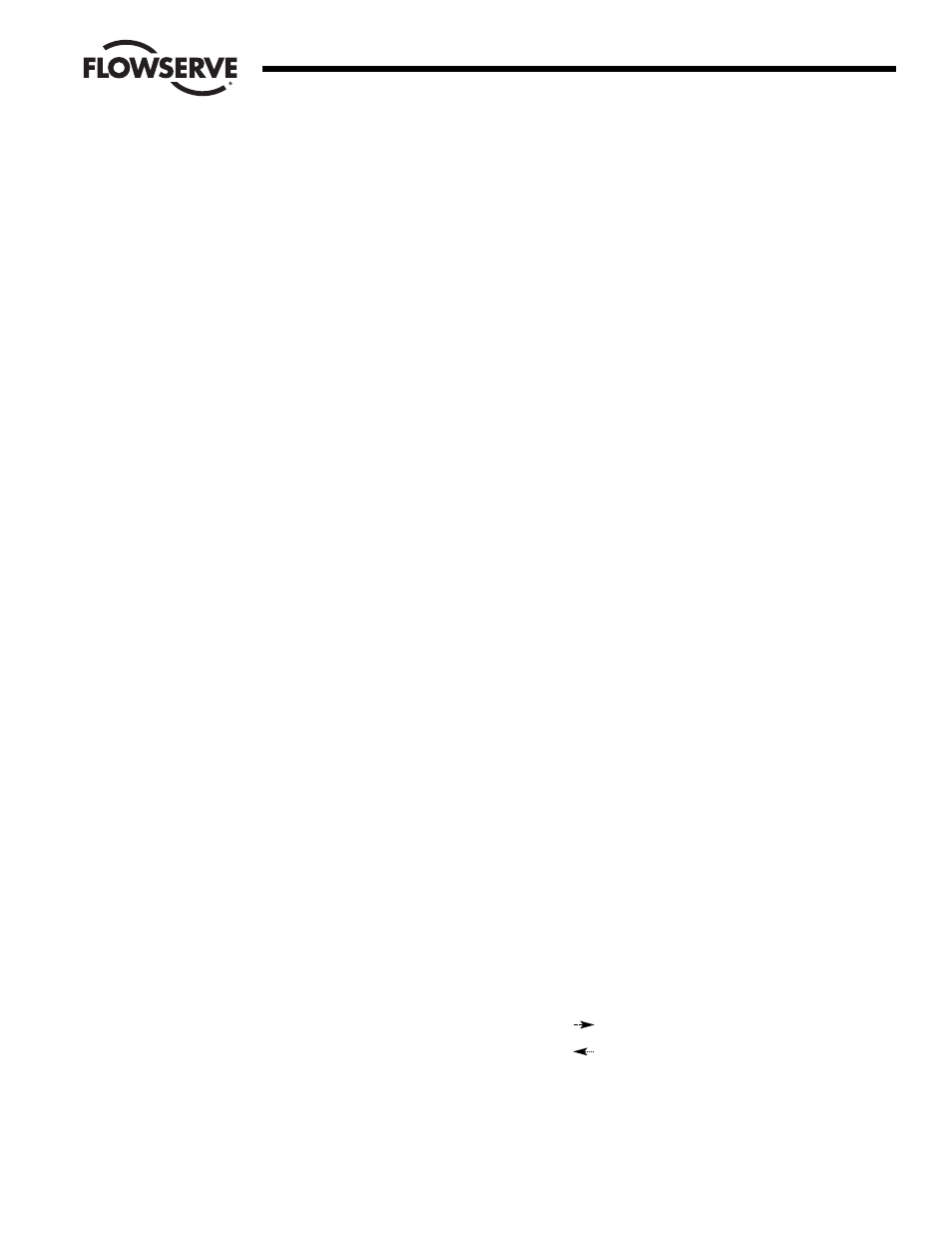
WCAIM2037
DataFlo Digital Electronic Positioner DFP17 Installation, Operation and Maintenance Instructions
23
4.9.1 Packet Communications Software
See the Worcester/McCANNA Packet Communications
specification for the communications protocol
information.
It is on the software floppy diskette in the form of a text
file in the commspec directory and is called
commspec.txt.
4.9.2 RS-485 Connection
The RS-485 Converter must be connected to the
positioner at the TB2 terminal block through the actuator
terminal strip (see Figure 8).
4.9.3 Communications Software
A floppy disc is provided with the software to be installed
on the computer which will allow communication with
the positioner. There are four programs on the floppy—
ICP1.EXE, ICP2.EXE, ICP3.EXE, and ICP4.EXE as well as
several support files. These programs work with COM1,
COM2, COM3, and COM4 respectively. The programs
may be run from the floppy (Flowserve strongly
recommends that one or two backups be made of the
software diskette before using it. Write protect the disks),
or the software may be copied to the computers hard
drive (create an ICP directory and then copy all the files
to that directory).
4.9.4 Serial Port Setup
The serial port to be used must be set up as follows:
Baud Rate
1200 bps to 38.4 kbps
Data Bits
8
Stop Bits
1
Parity
None
The correct communications program to run is based on
the COM port to be used (i.e., ICP1.EXE for COM1).
4.9.5 Monitor Display
Once the program has been started, the following screen
will appear (see Figure 9).
The program will start up looking for address 1. If that
unit exists, communications are established. Otherwise,
to establish communications with the positioner, tap the
space bar. The cursor to the right of the arrow next to the
address parameter will begin flashing. Type in the
positioner address and then hit the enter key (factory
default is 1). The words Reading data... will appear to
the right of the arrow. In about two seconds the screen
will fill with the positioner data. The arrow just to the left
of the Status area indicates whether the positioner is
under control of the analog signal or under the control of
the computer (PC). The F4 key toggles between
computer and analog control of the positioner.
The PC Cmd value in the Status area is the position
output of the computer. This value can be changed with
the left and right cursor keys but will only control
position when the F4 key toggles to PC Cmd. Position
can also be changed by hitting the F12 key, entering the
desired position on the numeric keypad and then hitting
the enter key.
Input is the value of the analog signal being received by
the positioner board and controls position only when the
F4 key toggles to Input.
Output is the value of the 4-20 mA output signal for shaft
position feedback (when this option is installed). Shaft
Pos is the actual readout of the actuator shaft position in
percent of shaft travel.
DB Run is the current setting for positioner deadband.
When shaft motion stops, shaft position should always
be within the deadband of the position command signal.
The Alarms are Over, Under, Dev (Deviate) and Therm
(Thermal). The area immediately under one of these
alarms will light up if that alarm condition exists. The
alarms are defined as follows:
Over - Shaft position is greater than the value set in the
Over-travel Alarm.
Under - Shaft position is less than the value set in the
Under-travel Alarm.
Dev - Shaft has not reached position called for by signal
within the time specified by Deviation Alarm.
Therm - High temperature alarm for DC motor driver IC.
The Calibration Data is a listing of the stroke times
measured during calibration.
The listings under Ver x.xx are the keys required to
control the screen and the positioner.
F2 -
Load a file of all parameters including curve data
from the hard drive and download it to the
positioner (about 40 seconds).
F3 -
Save the data in the positioner to a file on the
hard drive (about 20 seconds).
F4 -
Toggle control of the positioner between the
analog signal and the computer.
F9 -
Enter the positioner response curve edit screen.
F10 - Enter the positioner ASCII EEPROM edit screen.
(Customer information for this unit)
F12 - Enter desired position on numeric keypad then
press enter.
- Increment
the
PC Cmd position output signal.
- Decrement
the
PC Cmd position output signal.
Alt-x - Exit the ICP program and return to DOS or
Windows.
Flow Control
Worcester Actuation Systems