Yaskawa F7 Drive Technical Manual Orientation User Manual
Page 3
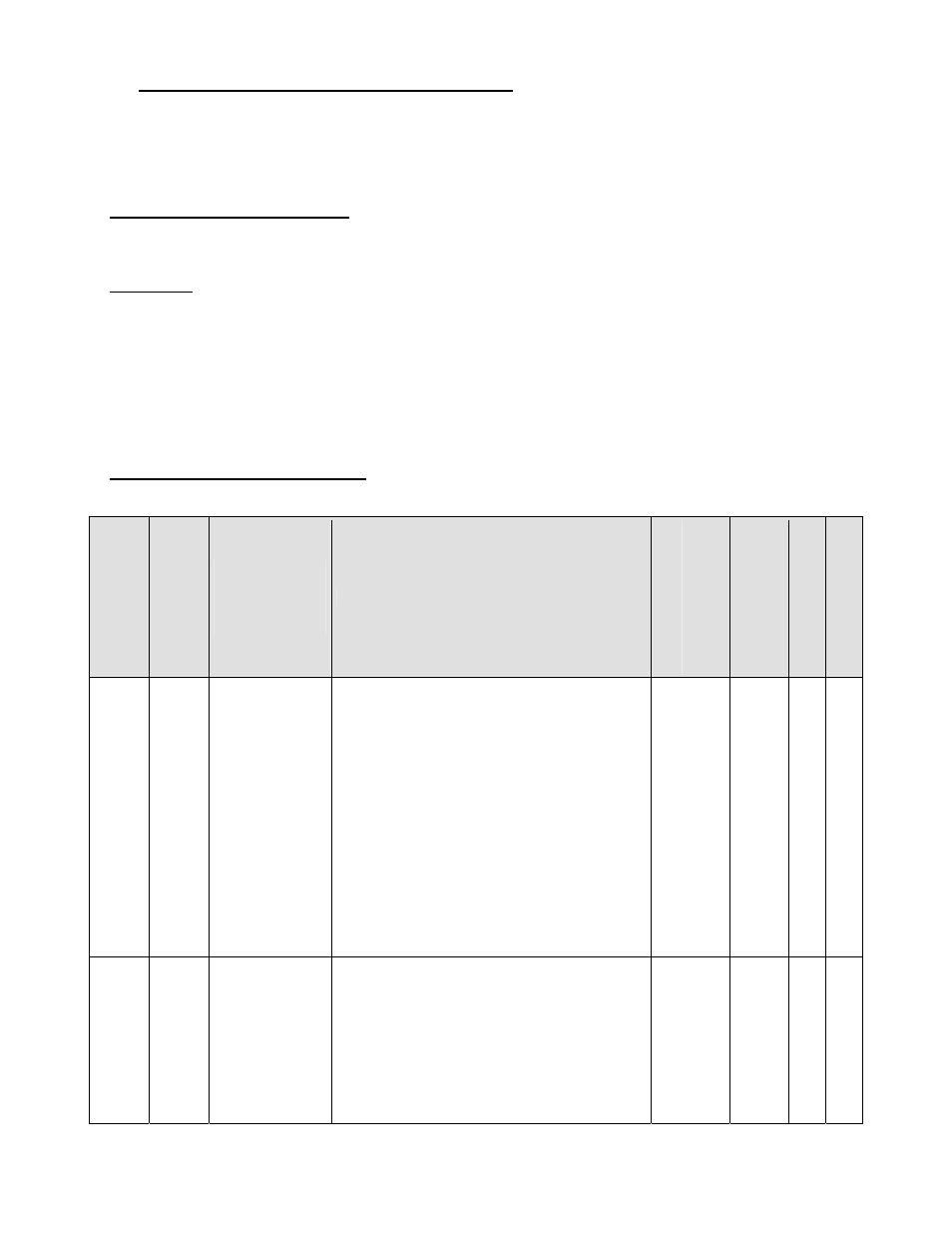
Date: 03/03/06, Rev: 06-03
Page 3 of 16
TM.F7SW.063
1.3 Closed Loop Vector Control with Position Encoder
The closed loop vector control method (A1-02 = 3) can also be used when the motor and the machine part
to be oriented (positioned) are connected through a drive train with a constant ratio. This requires 2
encoders, one mounted on the driven motor, and the other on the machine part to be oriented. A PG-W2
dual encoder feedback option card is required. This method will provide superior performance than the
open loop method.
2.0 Changes from Standard Product
The orientation function is added. The function is active in all control modes (A1-02) and visible in the advanced
access level (A1-01 = 2).
3.0 Limitations
a. The multi-function digital input function Motor 2 Select (H1-XX = 16) cannot be used in all applications of
this software. See parameter P1-01.
b. When any of the 3 multi-function digital input Orientation Command (H1-XX = 80 ~ 82) functions are
programmed, the standard software functions DC Injection Command (H1-XX = 60) and Zero-Servo
Command (H1-XX = 72) are disabled.
c. The orient function is disabled when the drive is in "local" mode by pressing the local/remote button on the
keypad, or by activating the local/remote multi-function digital input, or by setting B1-02 = 0 (drive
sequence from the keypad).
4.0 Related Parameters and Functions
4.1 Parameters
Parameter Number
Modb
us Addr
e
ss
Parameter Name
Digital Operator
Display
Description
Ran
ge
Default
Cha
nge D
uri
ng
Run
Access Level For All
Contro
l Modes
*1
P1-01 600H
PG Channel
Selection
PG Channel Sel
This parameter selects whether channel 1 or
channel 2 of the encoder feedback card will be
used for orientation.
0: Channel 1
1: Channel 2
Note: When using a PG-X2 card, set P1-01 = 0.
Note: This software does not fully support the
multi-function digital input function Motor 2 Select
(H1-0X = 16). When using a PG-W2 card, it is
possible to run 2 different motors/encoders and
switch between them using the programmed
digital input. However, P1-01 will not
automatically switch. Therefore, only 1 orientation
encoder can be used for an application.
0 ~ 1
0
No
A
P1-02 601H
Position Encoder
PPR
Pos. Encoder
PPR
This parameter sets the PPR (pulses per
revolution) of the orientation encoder. The PPR is
the number of actual pulses for one revolution of
the orientation (positioning) encoder.
Note: When operating in closed loop vector (A1-
02 = 3) and P1-01 = 0, set P1-01 = F1-01.
Note: This parameter is set in encoder PPR, not
quadrature encoder counts (counts = PPR x 4).
0 ~ 8192
PPR
1024 No A
*1: Access Level (A1-01): Q = “Quick Start”, A = “Advanced”, F = “Factory”.