Yaskawa MP2000iec Series User Manual
Page 6
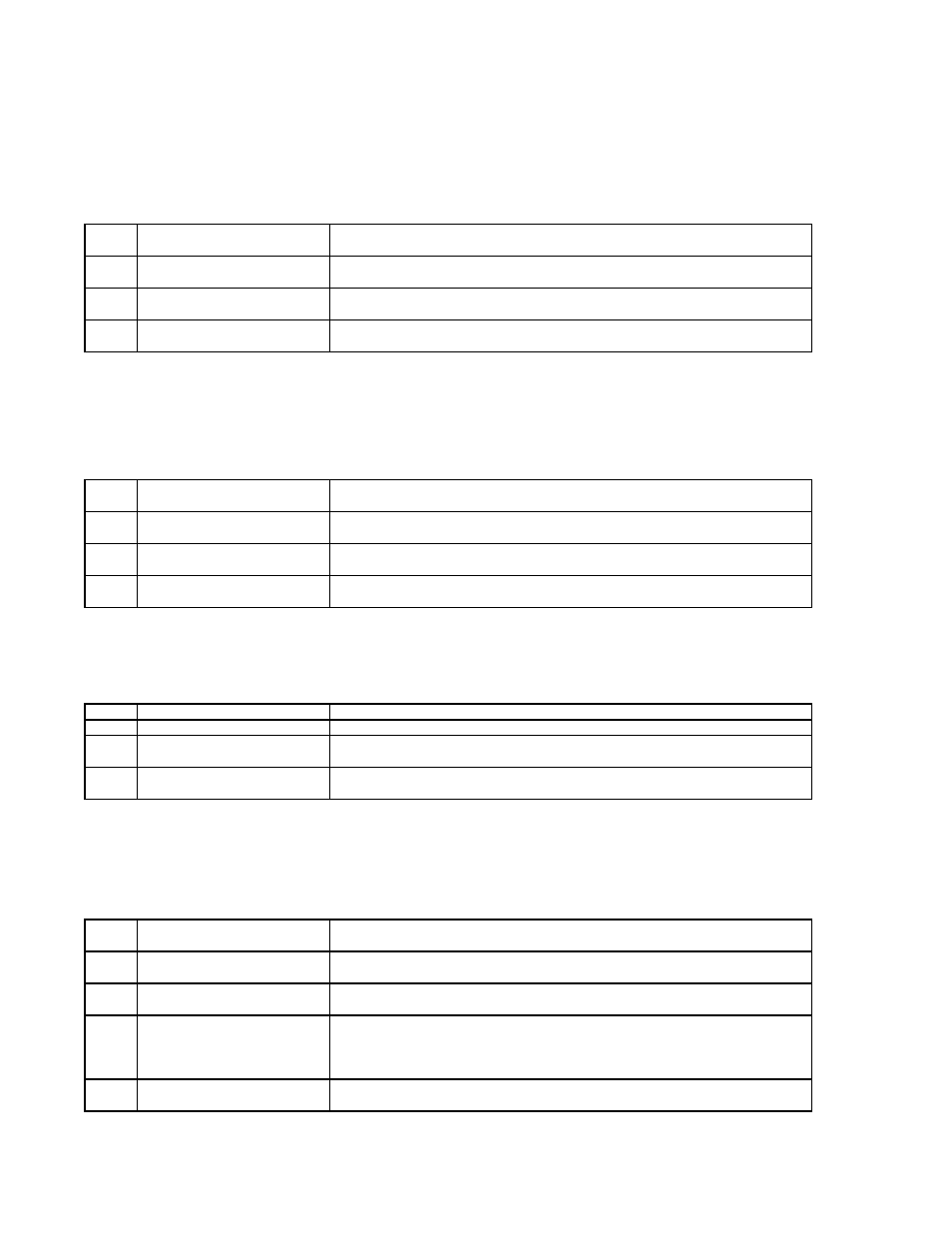
MP2000iec Series QRG Rev 3.3
1.B Clear Alarm A.810 (Initialize Absolute Encoders)
KEY INFORMATION
Alarm A.810 means that the absolute encoder of the servomotor lost the position
during power off because BATTERY power was lost to the servomotor, invalidating
the absolute position.
The alarm can by cleared by: 1) Web Server. 2) Y_ResetAbsoluteEncoder function
block, 3) SigmaWin+ software, 3) Fn008 (Digital Operator).
Step
Description
Detail
1
Login to Webserver
See Procedure. Login: Admin. Password: MP2300S, MP2600, MP3200, MP3300
2
Initialize absolute encoder
Machine Operations. Determine which axis number has the alarm. Drive PN tab,
pull down to select the axis number. Click "abs encoder init" button.
3
Reboot Controller and Sigma5
Servopack
Under "Maintenance" -> reboot, then "Reboot Controller" and "OK" to confirm. Wait
45 seconds for reboot.
4
Zero-Set / Home and machine
calibration
Follow steps according to application programming of machine. Home offsets for
absolute encoder are stored in SRAM of controller .
1.C Clear Alarm A.CC0
KEY INFORMATION
Alarm A.CC0 means that the servomotor's absolute encoder Multi-turn Limit
(Rollover) setting does not match the Multi-turn Limit setting of the servopack
(Pn205). The parameter can be sent from servopack to encoder by: 1) Web Server.
2) Y_ResetAbsoluteEncoder function block, 3) SigmaWin+ software, 3) Fn00C
(Digital Operator).
Step
Description
Detail
1
Login to Webserver
See Procedure. Login: Admin. Password: MP2300S, MP2600, MP3200, MP3300
2
Initialize absolute encoder
Machine Operations. Determine which axis number has the alarm. Drive PN tab,
pull down to select the axis number. Click "Multiturn Reset" button.
3
Reboot Controller and Sigma5
Servopack
Under "Maintenance" -> reboot, then "Reboot Controller" and "OK" to confirm. Wait
45 seconds for reboot.
4
Zero-Set / Home and machine
calibration
Follow steps according to application programming of machine. Home offsets for
absolute encoder are stored in SRAM of controller .
1.D Replace the controller
KEY INFORMATION
MotionWorks IEC software is NOT required
The new controller must match the old in the following areas:
1. IP address , 2. SRAM, 3. Firmware, 4.Project Archive
Step
Description
Detail
1
Set up the controller
See procedure 1.0
2
Load Project Archive
See procedure . Webserver: Project Archive -> "Browse", "Clean Install"
3
Reboot Controller
Under "Maintenance" -> reboot, then "Reboot Controller" and "OK" to confirm. Wait
45 seconds for reboot.
4
Zero-Set / Home and machine
calibration
Follow steps according to application programming of machine. Home offsets for
absolute encoder are stored in SRAM of controller .
1.E Replace a Servopack (Mechatrolink)
KEY INFORMATION:
Step
Description
Detail
1
Install the replacement
servopack
Power supply, motor, encoder, Mechatrolink, IO, holding brake, regen resistors, etc
2
Set the Mechatrolink Address
Note the rotary address switch setting of existing servopack and set the same
address to the replacement servopack.
3
Login to Webserver
See Procedure. Login: Admin. Password: MP2300S, MP3200, MP3300
Expect controller alarm 3301 000b "Pn002 not correctly initialized"
4
Send Drive Parameters
Drive Parameters -> User Parameters, "verify" each axis. Verify compares
parameters in the archive with the current parameters in the servo. "Write" and
"OK" to send parameters from archive to servo. Takes just a couple seconds to
write.
5
Reboot
Under "Maintenance" -> reboot, then "Reboot Controller" and "OK" to confirm. Wait
45 seconds for reboot.
The Servopack parameters can also be written
* From the controller, automatically, according to the controller program
* From MotionWorks IEC project file
* From a previously saved SigmaWin+ parameter file
Page 6 of 15