2 pump lubricants – Flowserve Mark 3 Sealed Metallic Durco User Manual
Page 36
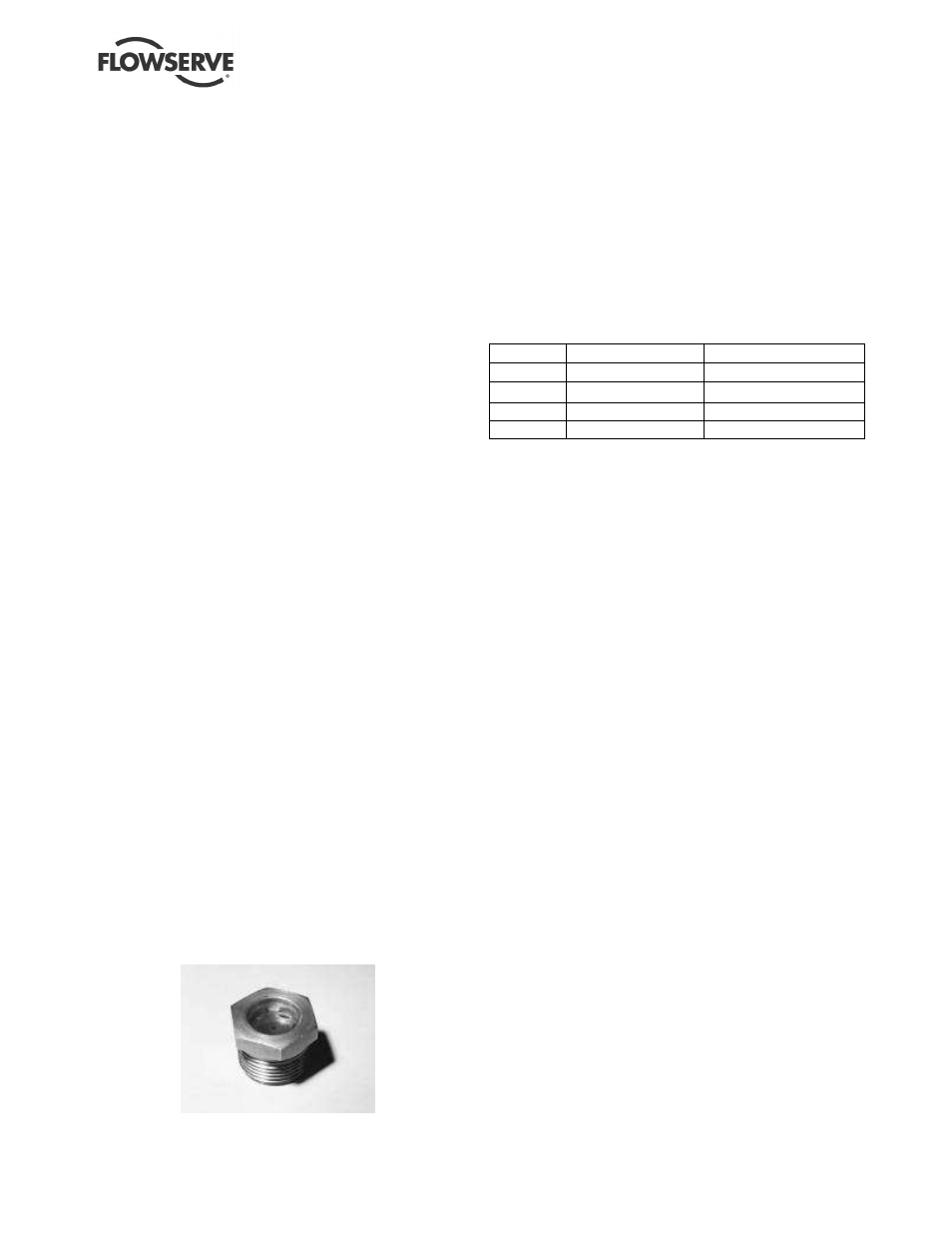
MARK 3 USER INSTRUCTIONS ENGLISH 71569102 01-13
Page 36 of 72
flowserve.com
5.2 Pump lubricants
5.2.1
Oil bath
Oil bath is available on all product lines with the
exception of the In-Line pump. The standard bearing
housing bearings are oil bath lubricated and are not
lubricated by Flowserve. Before operating the pump,
fill the bearing housing to the center of the oil sight
glass with the proper type oil. (See figure 5.2 for
approximate amount of oil required - do not overfill.)
On the Mark 3A design, an optional oil slinger is
available. The oil slinger is not necessary; however,
if used, it provides an advantage by allowing a larger
tolerance in acceptable oil level. Without an oil
slinger, the oil level in the bearing housing must be
maintained at ±3 mm (±
1
/
8
in.) from the center of the
sight glass. The sight glass has a 6 mm (¼ in.) hole
in the center of its reflector. The bearing housing oil
level must be within the circumference of the center
hole to ensure adequate lubrication of the bearings.
See Figure 5.3 for recommended lubricants. DO
NOT USE DETERGENT OILS. The oil must be free
of water, sediment, resin, soaps, acid and fillers of
any kind. It should contain rust and oxidation
inhibitors. The proper oil viscosity is determined by
the bearing housing operating temperature as given
in figure 5.5.
To add oil to the housing, clean and then remove the
vent/breather [6521] at the top of the bearing housing,
pour in oil until it is visually half way up in the sight glass
[3856]. Fill the constant level oiler bottle, if used, and
return it to its position. The correct oil level is obtained
with the constant level oiler in its lowest position, which
results in the oil level being at the top of the oil inlet pipe
nipple, or half way up in the sight glass window. Oil
must be visible in the bottle at all times.
Note that on ANSI 3A™ power ends there is no
constant level oiler and no vent/breather (replaced by
a plug). As stated above, proper oil level is the
center of the “bull’s eye” sight glass [3856]. (See
figure 5.1.)
Figure 5.1
In many pumping applications lubricating oil becomes
contaminated before it loses its lubricating qualities or
breaks down. For this reason it is recommended that
the first oil change take place after approximately 160
hours of operation, at which time, the used oil should be
examined carefully for contaminants. During the initial
operating period monitor the bearing housing operating
temperature. Record the external bearing housing
temperature. See figure 5.6 for maximum acceptable
temperatures. The normal oil change interval is based
on temperature and is shown in figure 5.7.
Figure 5.2: Amount of oil required
Pump
Mark 3
Mark 3A
Group 1
148 ml (5 fl. oz.)
251 ml (8.5 fl. oz.)
Group 2
560 ml (19 fl. oz.)
946 ml (32 fl. oz.)
Group 3
1419 ml (48 fl. oz.)
1419 ml (48 fl. oz.)
Grp 3-HD
n/a
1005 ml (34 fl. oz.)
Grease lubricated pumps and electric motors are
supplied pre-greased.
Where the ambient temperature is very low, special
lubricants are required. Where oil lubrication is
utilized and the ambient is less than -5 °C (23 °F)
ensure the oil pour point is at least 15 °C (27 °F)
lower than the ambient, or use oil class SAE 5W-50
or API-SJ and ensure the upper operating range of
the oil is then not exceeded. IS0 VG 46 oil is
generally selected for an initial lubrication schedule.
Other drivers and gearboxes, if appropriate, should
be lubricated in accordance with their manuals.