Flowserve Mark 3 Sealed Metallic Durco User Manual
Page 58
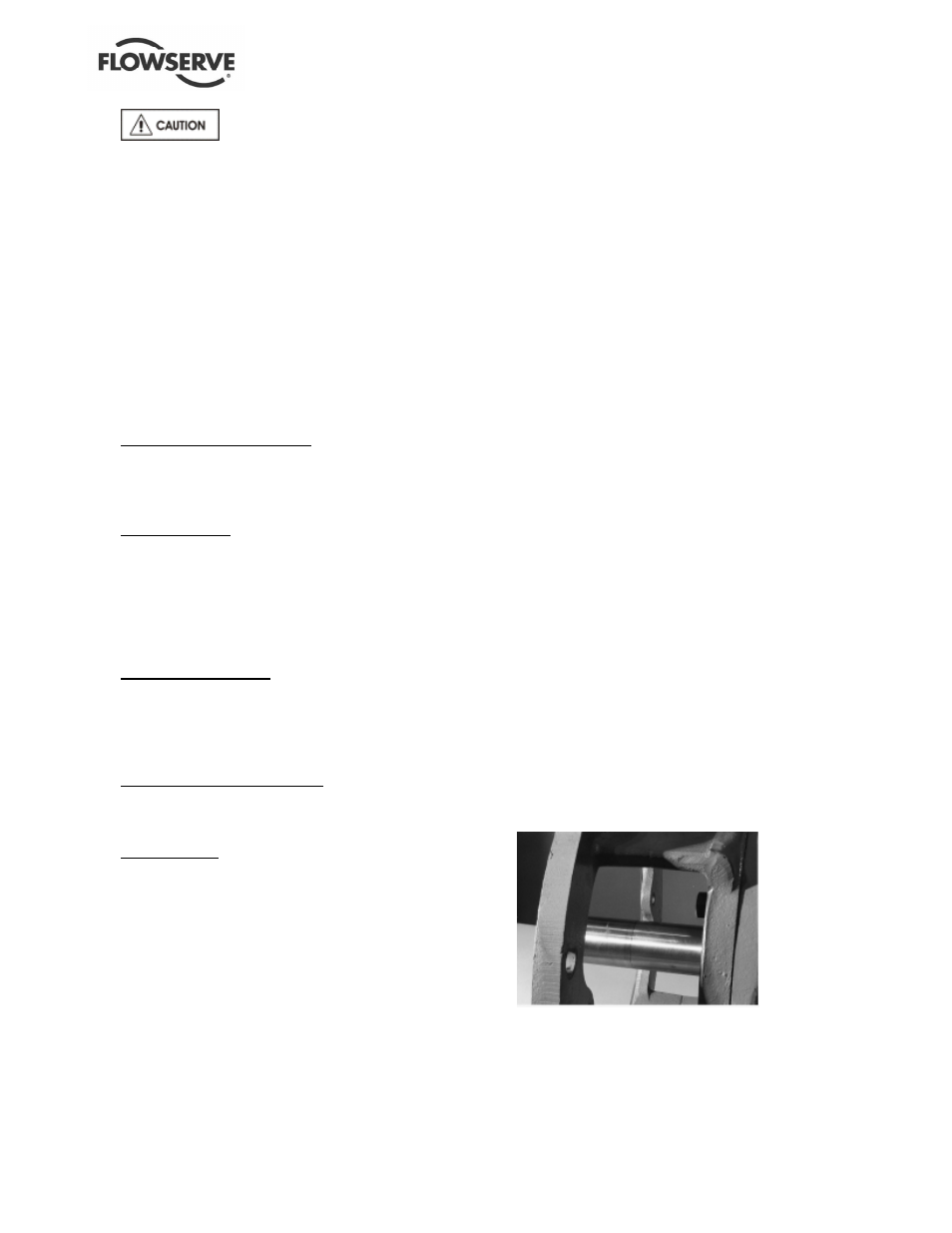
MARK 3 USER INSTRUCTIONS ENGLISH 71569102 01-13
Page 58 of 72
flowserve.com
Never compress the snap ring
unless it is positioned around the shaft and between
the bearings. In this configuration, it is contained
therefore if it should slip off the compression tool it
is unlikely to cause serious injury.
d) The shaft, bearings, and bearing carrier assembly
(figure 6.14) can now be installed into the bearing
housing [3200]. The bearing carrier [3240] should
be lubricated with oil on the O-rings and threads
before installing the assembly into the bearing
housing. Thread the bearing carrier into the
bearing housing by turning it clockwise to engage
the threads. Thread the carrier onto the housing
until the carrier flange is approximately 3 mm (
1
/
8
in.)
from the housing. Install the set screws [6570.3]
loosely.
e) Reinstall any tags, plugs, site gages and oiler.
Mark 3 and Mark 3A design
Install the following items onto the bearing housing;
oil level tag (figure 6.18) and combination Trico
oiler/site gage [3855], vent/breather [6521] and
drain plug [6569.1].
ANSI 3A design
Install the following items onto the bearing
housing; oil level tag (figure 6.18) and site gage
[3855], plug [6521] and magnetic drain plug
[6569.4].
f) On Group 2 and 3 pumps, assemble the bearing
housing adapter [1340] to the bearing housing
[3200]. Be sure to install a new O-ring [4610.1].
Mark 3 In-Line design
The adapter O-ring [4610.1] should not be
installed if there is a drain tap in the adapter
[1340]. This tap is present on pumps with
regreasable bearings and most oil mist
applications.
Mark 3A and ANSI 3A design
Thread the capscrews [6570.5] through the
adapter and into the tapped holes in the bearing
housing.
Mark 3 design
Use the capscrews [6570.5] and hexnuts
[6580.8]. Orient the bearing housing adapter with
the two holes for capscrews [6570.5] on a
horizontal line.
g) If the pump has lip seals, install the deflector [2540].
h) If the pump is equipped with a hook type sleeve
[2400], slip it into place over the impeller end of
the shaft [2100].
6.9.2
Wet end assembly
Cartridge mechanical seals
6.9.2.1
Review the seal assembly instructions and drawings
provided by the seal manufacturer.
a) Install a nose cone on the end of the shaft and
then slide the cartridge seal [4200] onto the shaft
until it lightly touches the bearing housing [3200]
or adapter [1340]. See figure 6.10.
b) Install the rear cover plate [1220] to the bearing
housing (Group 1) or the bearing housing adapter
(Group 2 and 3) by using the capscrews [6570.2].
Now install the cartridge seal gland to the rear
cover plate [1220] using studs [6572.2] and nuts
[6580.2].
c) Install the impeller [2200] as instructed in section
6.6. Care should be taken in the handling of high
chrome iron impellers.
d) Tighten set screws on the seal to lock the rotating
unit to the shaft. Finally, remove centering clips
from the seal.
Component type mechanical seal
6.9.2.2
Review the seal assembly instructions and drawings
(seal set dimension) provided by the seal
manufacturer.
In order to properly set a component seal it is
necessary to first locate the shaft in its final axial
position. This is accomplished in the following
manner.
a) Install the rear cover plate [1220] to the bearing
housing (Group 1) or the bearing housing adapter
(Group 2 and 3) by using the capscrews [6570.2].
b) Install and set the impeller [2200] clearance as
outlined in section 6.6. Put blueing on the shaft/
sleeve in the area near the face of the seal
chamber (rear cover 1220]. Scribe a mark on the
shaft at the face of the seal chamber (figure 6.34).
Figure 6.33
c) Remove the impeller and seal chamber (rear cover)
following the instructions given in section 6.7 and
install a nose cone onto the end of the shaft.