Flowserve FRBH User Manual
Page 36
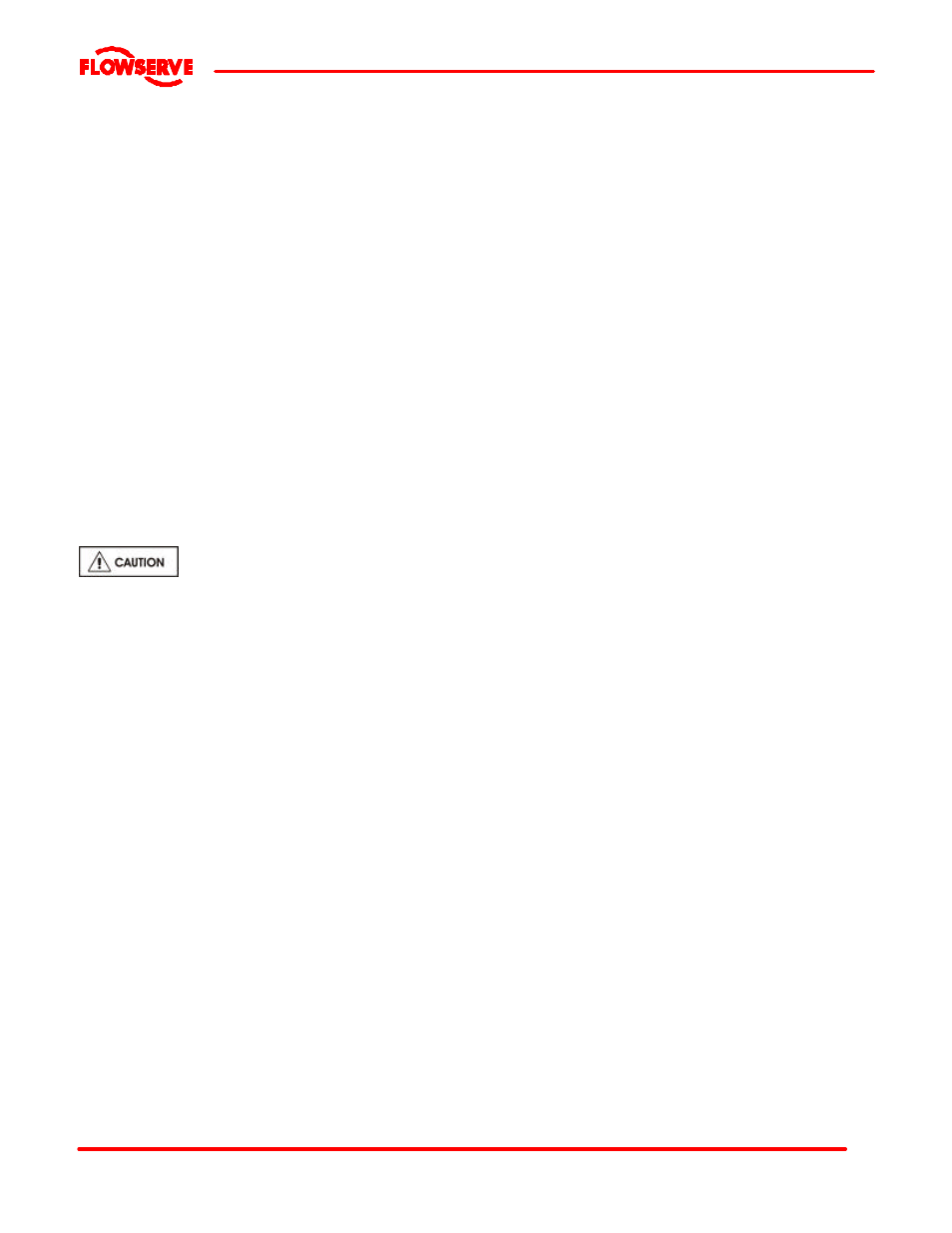
FRBH, FRBHX AND FRBHS USER INSTRUCTIONS ENGLISH 71569178 10-04
Page 36 of 54
®
‘V’ Blocks.
b) Only if necessary remove the line bearing [16] from
the shaft. Bearings removed and reused can easily
be damaged and undetected until pump is put back
in operation.,
6.8.6 Thrust bearings
a) Lay the shaft [6] horizontal and support with wooden
‘V’ Blocks.
b) Remove the thrust bearing clamp ring [37] from the
thrust bearing housing [33].
c) Bend up the locking tab on the bearing lockwasher
[22A] and remove the bearing locknut [22] and
lockwasher [22A].
d) Only if necessary remove the thrust bearings [18]
from the shaft. Bearings removed and reused can
easily be damaged and undetected until pump is put
back in operation
6.8.7 Wearplate
a) The wearplate can be removed from the casing if
required. The wearplate is secured in place using
studs and hex nuts.
6.9 Examination of parts
Used parts must be inspected before
assembly to ensure the pump will subsequently run
properly.
In particular, fault diagnosis is essential to enhance
pump and plant reliability.
6.9.1 Casing, seal housing and impeller
a) Inspect for excessive wear, pitting, corrosion,
erosion or damage and any sealing surface
irregularities.
b) Replace as necessary.
c) Inspect the impeller [2] and the wearplate [181] for
excessive wear or damage. Remove the wearplate
from the casing [1] if necessary.
d) Inspect the casing [1] and stuffing box head [11] for
damage or excessive thinning of wall sections due to
wear or corrosion. Clean the internal surfaces to
maintain pump efficiency.
e) Inspect the stuffing box bushing [63] and remove if
damaged or worn. Clean the internal bore of the
stuffing box.
6.9.2 Shaft and sleeve [if fitted)
a) Replace sleeve if grooved, pitted or worn.
b) Clean the shaft and inspect for evidence of
corrosion, evidence of cracking, fatigue or mechanical
damage. Remove all burrs or nicks paying particular
attention to the areas under the lip seals. Check that
the shaft is straight within 0.002 inch (0.050 mm).
6.9.3 Gaskets and O-rings
After dismantling, discard and replace.
6.9.4 Bearings
a) It is recommended that bearings are not re-used
after any removal from the shaft.
b) The plain liquid lubricated bearings may be re-
used if both the bearing bush and bearing sleeve
show no sign of wear, grooving or corrosion
attack. (It is recommended that both the bush and
sleeve are replaced at the same time.)
6.9.5 Bearing isolators, labyrinths or lip seals
(if fitted)
a) The lubricant, bearings and bearing housing seals
are to be inspected for contamination and
damage. If oil bath lubrication is utilised, these
provide useful information on operating conditions
within the bearing housing.
b) If bearing damage is not due to normal wear and
the lubricant contains adverse contaminants, the
cause should be corrected before the pump is
returned to service.
c) Labyrinth seals and bearing isolators should be
inspected for damage but are normally non-
wearing parts and can be re-used.
d) Bearing seals are not totally leak free devices.
Oil from these may cause staining adjacent to the
bearings.
6.10 Assembly
To assemble the pump consult the sectional drawings,
see section 8, Parts list and drawings.
Ensure threads, gasket and O-ring mating faces are
clean. Apply thread sealant to non-face sealing pipe
thread fittings.
6.10.1 Bearing housing
a) Lubricate the internal bores of the bearing frame [19]
with the same oil or greas e used to lubricate the
bearings.
b) Install the thrust bearing housing [33] in the bearing
frame [19] to ensure a good sliding fit. Remove the
thrust bearing housing from the frame.
c) Install the oil sight gauge [143] and the drain lug in
the bearing frame [19] using Teflon pipe thread
sealant. Install the vent plug [213].
6.10.2 Line bearing
a) Pack the line bearing with grease if the bearings are
being grease lubricated.
b) Lightly lubricate the shaft [6] at the line bearing
position. Install the line bearing [16] on the shaft.
Use an induction heated or hot oil bath to first heat
the bearing [250
°
F recommended], press the
bearing on shaft with the aid of a sleeve designed to