Pinnacle Systems STTS User Manual
Page 34
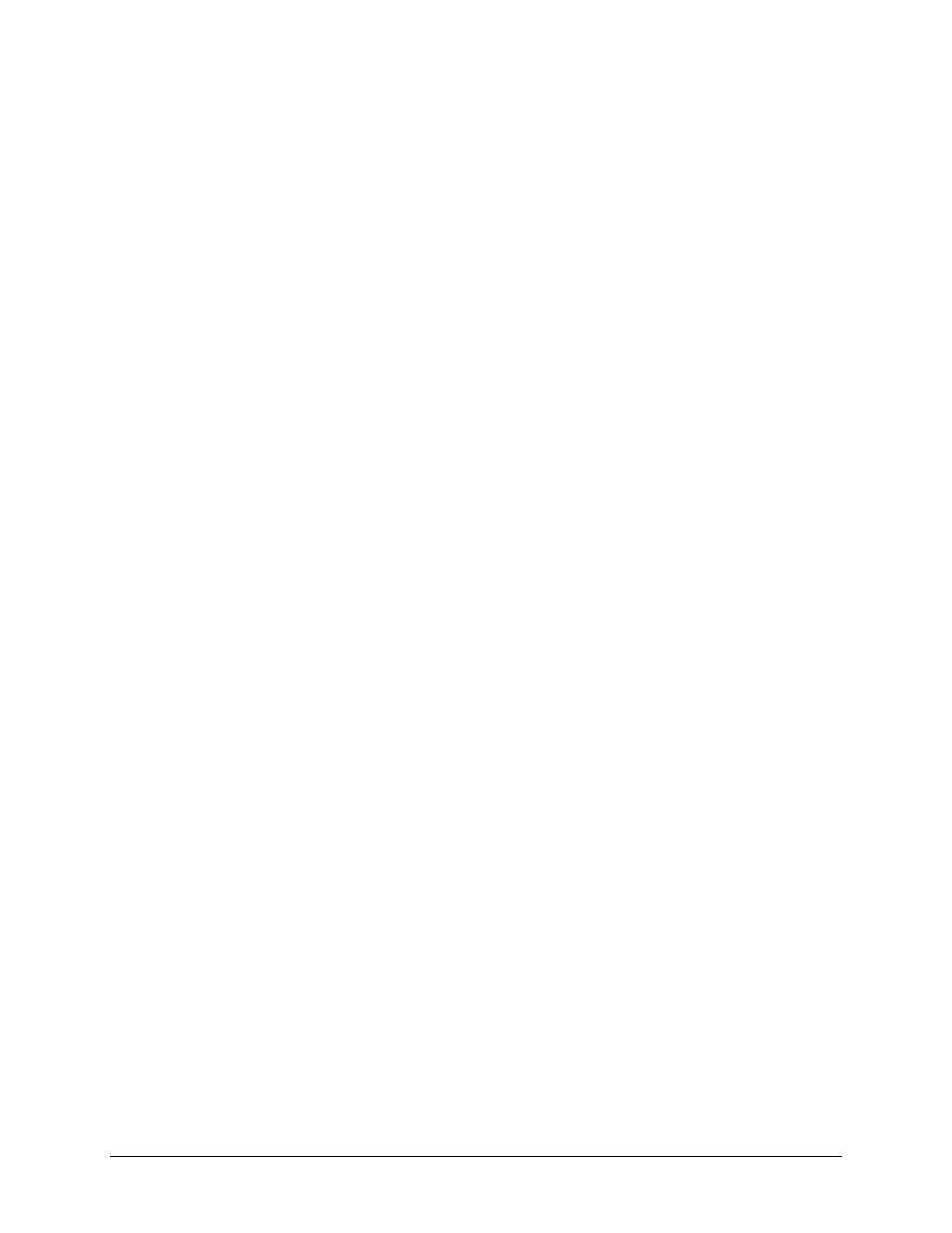
28
2) All other system interconnect Cables. This includes serial interface cables,
transducer cables, and unit power cables.
1.2) RACEWAY LAYOUT GUIDELINES
Once the cables of the system have been classified, the following suggestions should be
followed when possible to guard against coupling noise from one conductor to another in a
raceway. These guidelines apply to cable routing both inside and outside the enclosure.
1) All Type – 1 conductors should be routed in a separate raceway from Type 2 and
3 conductors. Type – 1 conductors may be routed with machine power
conductors of up to 600VAC , if it is done in accordance with all safety codes.
The raceway must be well grounded along its entire length.
2) All Type – 2 conductors must be properly shielded by conduit or bonded sealtite,
where applicable, and routed in a separate raceway. The raceway must be well
grounded along its entire length.
3) Route Type – 2 conductor raceways at least 1 ft (30 cm) from 120VAC Type – 1
conductor raceways, 2 ft. (60 cm) from 240 VAC Type – 1 conductor raceways,
and 3 ft. (100 cm) from 480 VAC Type – 1 conductor raceways when ever
possible.
4) Route Type – 2 conductors at least 3 ft. (100 cm) from any high power electric
device such as motors, generators, transformers, etc. whenever possible.
5) If a Type – 2 conductor raceway must cross Type – 1 conductor raceway, it
should do so at right angles to the Type – 1 raceway.
6) All Type – 3 conductors should be routed external to all raceways or, preferable,
in a raceway separate from any Type – 1 or Type – 2 conductor raceways.
2.0)
GROUNDING GUIDELINES
After the raceway layout has been established, the mounting of the components in the system and the
proper grounding should be done.
Proper grounding is important for safety reasons in electrical installations. With solid-state controls, such
as the STTS Mat Controller, proper grounding procedures (including the elimination of ground loops) has
the added advantage of reducing the effects of EMI interference. A proper grounding path must be
permanent and continuous and must be able to safely conduct all ground-fault currents to earth ground
with a minimum impedance.
2.1)
SHIELDED CABLES
Certain connections such as the safety mat wiring require conduit or bonded sealtite cables to help
reduce the effects of induced EMI noise from other conductors.
It is imperative that the shield is
grounded, but only at one end.
The shield should be grounded at the point that the signal is generated. For example, a transducer cable
should be grounded at the controller because it is the controller that generates the signals that operate
the transducer. If a shield is not grounded, the shield will act as an antenna and will actually help induce
the unwanted EMI noise into the cable! However, if the shield is grounded at both ends of the cable,
there is a potential of a ground loop will be formed that could cause faulty system operation.
If a cable must be spliced somewhere along its length, the splice must be made in
Grounded Metal
Enclosure. The drain wires of the shielded pairs MUST be connected to ensure that the cable is
shielded along its entire length. However, the shields and drain wires of the cable must be isolated from
the enclosure to prevent the possibility of a ground loop.