Skutt KilnMaster Kilns Manufactured between 2000 and 2006 User Manual
Page 34
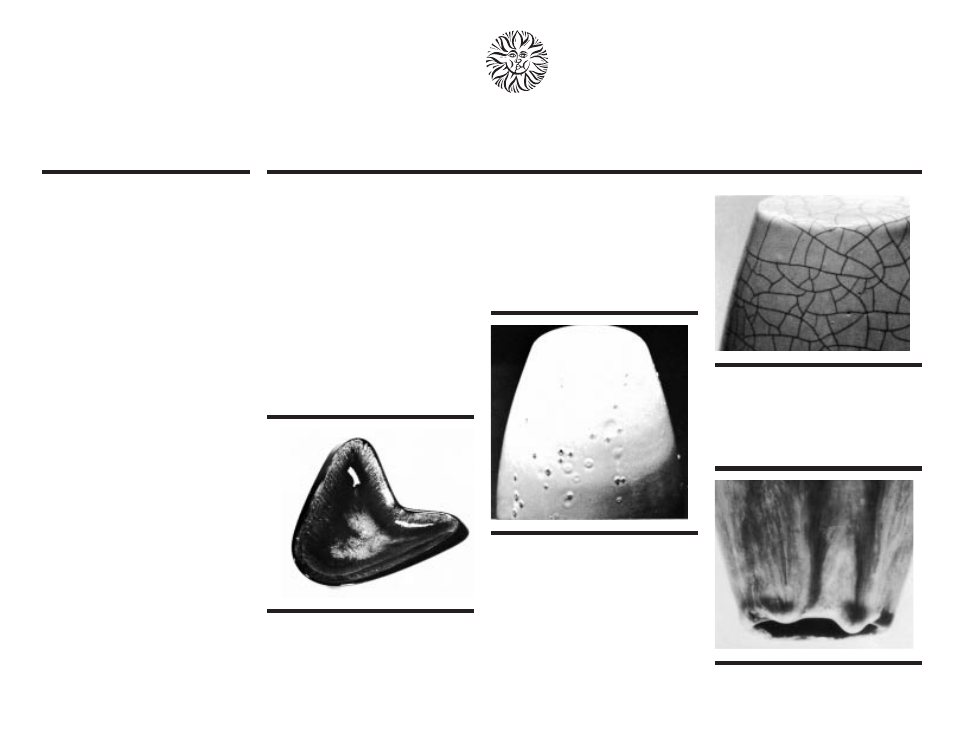
Some segments of the display are dim-
mer than others.
When a few segments of the LED display
become dimmer than the others, the prob-
lem may be the result of age, indicating
the circuit board may soon fail. Another
possible cause is exposure of the controller
to high heat. This situation needs atten-
tion. Do not use the kiln when this prob-
lem is present. Contact your distributor.
The thermocouple is flaking.
Flaking is normal with Type K thermo-
couples, especially when high fired. Use a
soft bristle toothbrush to remove the flakes
and vacuum them from the kiln so they
do not attach to your ware. Remove the
thermocouple element periodically and
check it for thinning.
The end firing temperature is different
now than when I first got my kiln and
the results do not seem quite right. What
should I do?
After about 50 Cone 6 firings, or 150 Cone
04 firings, it is necessary to replace the
thermocouple element. When the temper-
ature seems to drift, it is an indication that
the thermocouple is become thinner and
wearing out. Another possibility is a cone
correlation difference. Fine tuning of firing
temperatures is available. Call the Skutt
factory for instructions.
W
ARE
I
MPERFECTIONS
Common glaze faults
Crawled glaze.
In “crawling”, blank or
bald spots appear in the glaze surface after
firing. Crawling may be caused by having
a dusty or dirty bisque surface, or apply-
ing the glaze heavily. Skin oils from exces-
sive handling of greenware may clog clay
pores, causing the glaze to be repelled.
Hard spots in the clay surface created by
excessive sponging or polishing of the
greenware is also a cause. To salvage such
a piece, apply additional glaze to the bare
spot and refire, or cover the entire piece
with a textured glaze and refire.
Cratered or bubbled glaze.
In this glaze
error, the craters develop as a result of
body gases erupting through the glaze
and “freezing” as the kiln cools. This con-
dition is caused by underfiring. To salvage
such a piece, grind down the high spots,
apply a thin coating of glaze and refire to
a higher temperature.
Pinholes.
Pinholes are tiny indentations in
the glaze surface which are generally no
larger than the point of a pin. This fault
may occur in almost any type of glaze,
and is caused by underfiring. To salvage
a piece, refire at a higher temperature.
Sagging glaze on a vertical surface.
Sagging or running glaze is generally
caused by too heavy an application of
glaze. It is a warning sign that too much
glaze is being applied. Take extra care
with similar pieces.
32
Crawling glaze.
Pinholes, crazing.
Excess glaze.
Craters.