9 stopping and shutdown – Flowserve S-series PolyChem User Manual
Page 29
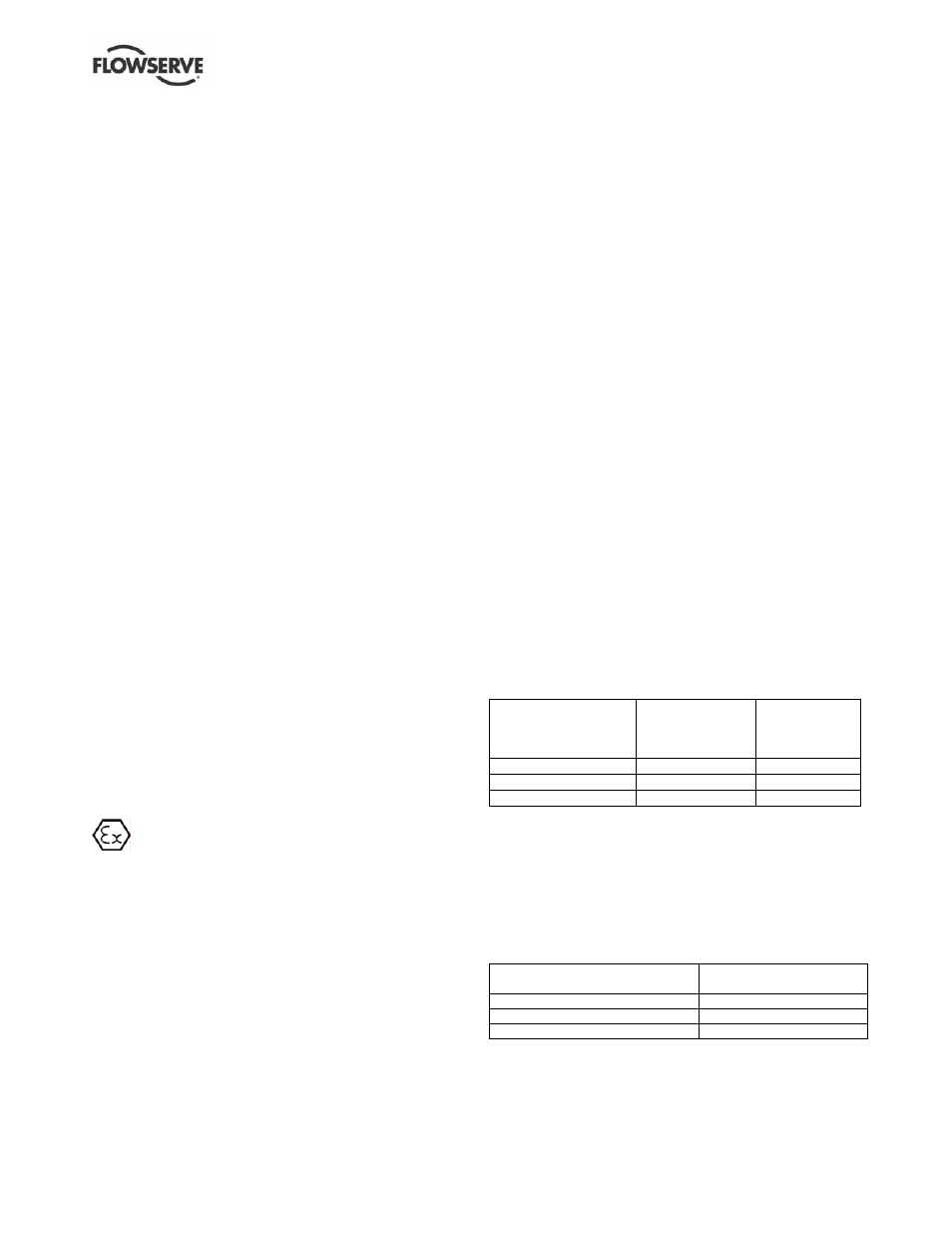
USER INSTRUCTIONS POLYCHEM S-SERIES ENGLISH 71569207 11-08
Page 29 of 52
flowserve.com
Avoid running a centrifugal pump at drastically reduced
capacities or with discharge valve closed for extended
periods of time. This can cause severe temperature
rise and the liquid in the pump may reach its boiling
point. If this occurs, the mechanical seal will be
exposed to vapor, with no lubrication, and may score or
seize to the stationary parts. Continued running under
these conditions when the suction valve is also closed
can create an explosive condition due to the confined
vapor at high pressure and temperature.
Thermostats may be used to safeguard against over
heating by shutting down the pump at a predetermined
temperature.
Safeguards should also be taken against possible
operation with a closed discharge valve, such as
installing a bypass back to the suction source. The size
of the bypass line and the required bypass flow rate is a
function of the input horsepower and the allowable
temperature rise.
5.8.3 Reduced head
Note that when discharge head drops, the pump’s
flow rate usually increases rapidly. Check motor for
temperature rise as this may cause overload. If
overloading occurs, throttle the discharge.
5.8.4 Surging condition
A rapidly closing discharge valve can cause a
damaging pressure surge. A dampening
arrangement should be provided in the piping.
5.8.5 Operation in sub-freezing conditions
When using the pump in sub-freezing conditions
where the pump is periodically idle, the pump should
be properly drained or protected with thermal devices
which will keep the liquid in the pump from freezing.
5.8.6 Bearing monitoring
If the pumps are operating in a potentially
explosive atmosphere temperature or vibration
monitoring of the bearings is recommended.
If bearing temperatures are to be monitored it is
essential that a benchmark temperature is recorded
at the commissioning stage and after the bearing
temperature has stabilized.
• Record the bearing temperature (t) and the
ambient temperature (ta)
• Estimate the likely maximum ambient
temperature (tb)
• Set the alarm at (t+tb-ta+5) ºC ((t+tb-ta+10) ºF)
and the trip at 100 ºC (212 ºF) for oil lubrication
and 105 ºC (220 ºF) for grease lubrication.
It is important, particularly with grease lubrication,
to keep a check on bearing temperatures. After
start up the temperature rise should be gradual,
reaching a maximum after approximately 1.5 to 2
hours. This temperature rise should then remain
constant or marginally reduce with time.
5.8.6.1 Normal vibration levels, alarm and trip
For guidance, pumps generally fall under a
classification for rigid support machines within the
International rotating machinery standards and the
recommended maximum levels below are based on
those standards.
Alarm and trip values for installed pumps should be
based on the actual measurements (N) taken on site
on the bearing housings of the pump in the fully
commissioned as new condition.
The example (N) value is given for the preferred
operating flow region (typically this may extend to 70
to 120 % of the pump best efficiency point); outside
the preferred flow region the actual vibration
experienced may be multiplied by up to 2.
These standard values can vary with the rotational
speed and the power absorbed by the pump. For any
special case, do not hesitate to consult us.
Measuring vibration at regular intervals will then show
any deterioration in pump or system operating
conditions.
Vibration velocity –
unfiltered
Horizontal pumps
≤ 15 kW (20 hp)
mm/s (in./sec)
r.m.s.
> 15 kW (20 hp)
mm/s (in./sec)
r.m.s.
Normal
N
≤ 3.0 (0.12)
≤ 4.5 (0.18)
Alarm
N x 1.25
≤ 3.8 (0.15)
≤ 5.6 (0.22)
Shutdown trip
N x 2.0
≤ 6.0 (0.24)
≤ 9.0 (0.35)
5.9 Stopping and shutdown
5.9.1 Shutdown considerations
Pump sets are normally suitable for the number of
equally spaced stop/starts per hour shown in the
table below. Check the capability of the driver and
control/starting system before commissioning.
Motor rating kW (hp)
Maximum start ups
per hour
Up to 15 (20)
15
Between 15 and 90 (20 and 120)
10
Above 90 (120)
6
Where duty and standby pumps are installed it is
recommended that they are run alternately every
week.