7 faults; causes and remedies – Flowserve S-series PolyChem User Manual
Page 47
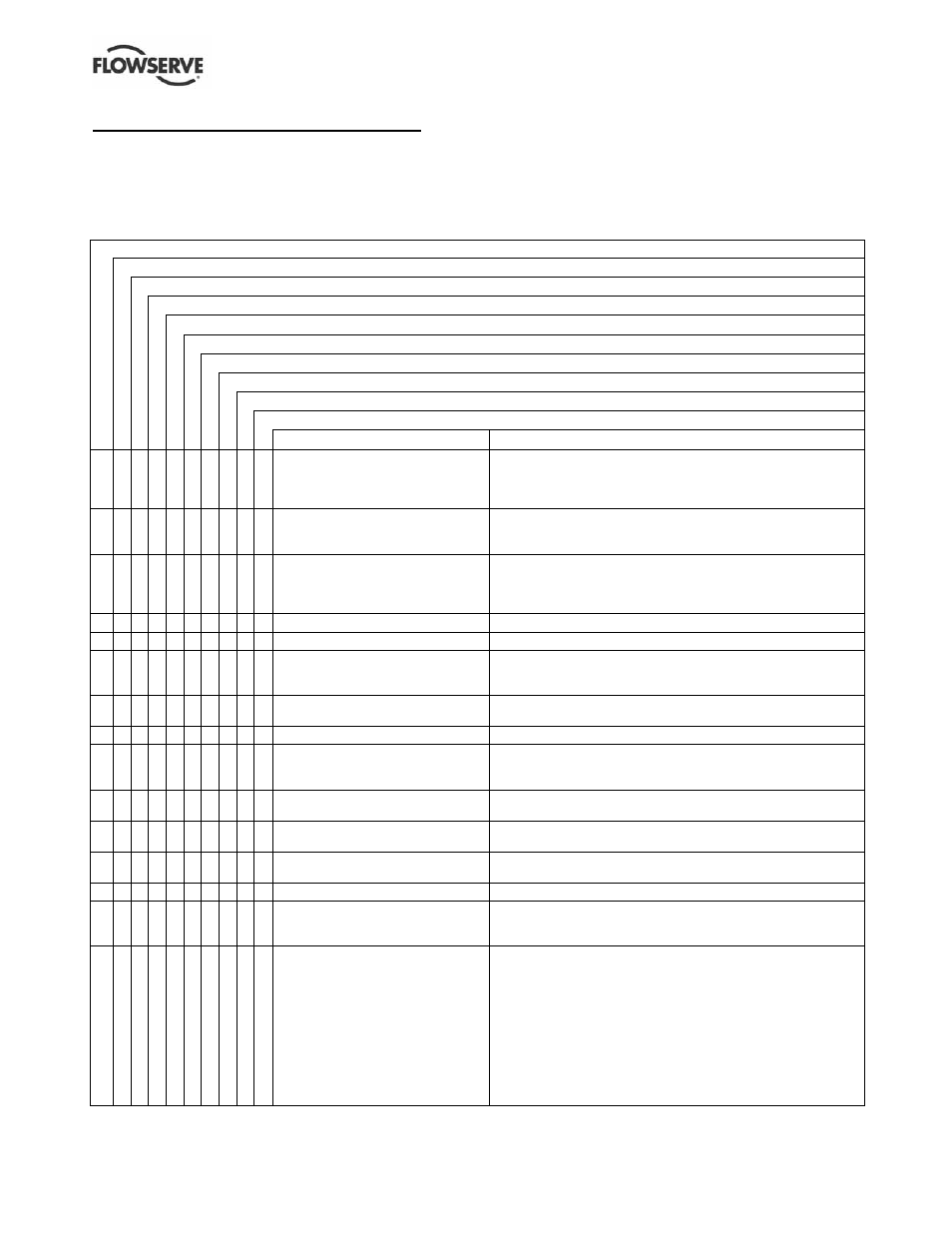
USER INSTRUCTIONS POLYCHEM S-SERIES ENGLISH 71569207 11-08
Page 47 of 52
flowserve.com
7 FAULTS; CAUSES AND REMEDIES
The following is a guide to troubleshooting problems with Flowserve PolyChem pumps. Common problems are
analyzed and solutions offered. Obviously, it is impossible to cover every possible scenario. If a problem
exists that is not covered by one of the examples, then refer to one of the books listed in section 10, Additional
sources of information, or contact a Flowserve sales engineer or distributor/representative for assistance.
FAULT SYMPTOM
Pump not reaching design flow rate
⇓
⇓
Pump not reaching design head (TDH)
⇓
⇓ No discharge or flow with pump running
⇓
⇓ Pump operates for short period, then loses prime
⇓
⇓ Excessive noise from wet end
⇓
⇓ Excessive noise from power end
⇓
⇓
⇓
⇓
⇓
⇓
⇓
⇓
⇓
⇓ PROBABLE CAUSES
POSSIBLE REMEDIES
z
z z z
Insufficient NPSH. (Noise may not be
present.)
Recalculate NPSH available. It must be greater than the NPSH
required by pump at desired flow. If not, redesign suction piping,
holding number of elbows and number of planes to a minimum to
avoid adverse flow rotation as it approaches the impeller.
z
z z
System head greater than anticipated.
Reduce system head by increasing pipe size and/or reducing
number of fittings. Increase impeller diameter. (nb: Increasing
impeller diameter may require use of a larger motor.)
z
z z
Entrained air. Air leak from
atmosphere on suction side.
1. Check suction line gaskets and threads for tightness.
2. If vortex formation is observed in suction tank, install vortex
breaker.
3. Check for minimum submergence
z
z
Entrained gas from process.
Process generated gases may require larger pumps.
z
z
Speed too low.
Check motor speed against design speed.
z
z z
Direction of rotation wrong.
After confirming wrong rotation, reverse any two of three leads on
a three phase motor. The pump should be disassembled and
inspected before it is restarted.
z
z
Impeller too small.
Replace with proper diameter impeller. (NOTE: Increasing
impeller diameter may require use of a larger motor.)
z
z
Impeller clearance too large.
Reset impeller clearance.
z
z z
Plugged impeller, suction line or
casing which may be due to a product
or large solids.
1. Reduce length of fiber when possible.
2. Reduce solids in the process fluid when possible.
3. Consider larger pump.
z
z
Wet end parts (casing cover, impeller)
worn, corroded or missing.
Replace part or parts.
z z
Not properly primed.
Repeat priming operation, recheck instructions. If pump has run
dry, disassemble and inspect the pump before operation.
z
Impeller rubbing.
1. Check and reset impeller clearance.
2. Check outboard bearing assembly for axial end play.
z z
Damaged pump shaft, impeller.
Replace damaged parts.
z
Abnormal fluid rotation due to
complex suction piping.
Redesign suction piping, holding the number of elbows and planes
to a minimum to avoid adverse fluid rotation as it approaches the
impeller.
z
Bearing contamination appearing on
the raceways as scoring, pitting,
scratching or rusting caused by
adverse environment and entrance of
abrasive contaminants from
atmosphere.
1. Work with clean tools in clean surroundings.
2. Remove all outside dirt from housing before exposing bearings.
3. Handle with clean dry hands.
4. Treat a used bearing as carefully as a new one.
5. Use clean solvent and flushing oil.
6. Protect disassembled bearing from dirt and moisture.
7. Keep bearings wrapped in paper or clean cloth while not in use.
8. Clean inside of housing before replacing bearings.
9. Check oil seals and replace as required.
10. Check all plugs and tapped openings to make sure that they
are tight.