BECKHOFF FC5101 User Manual
Page 74
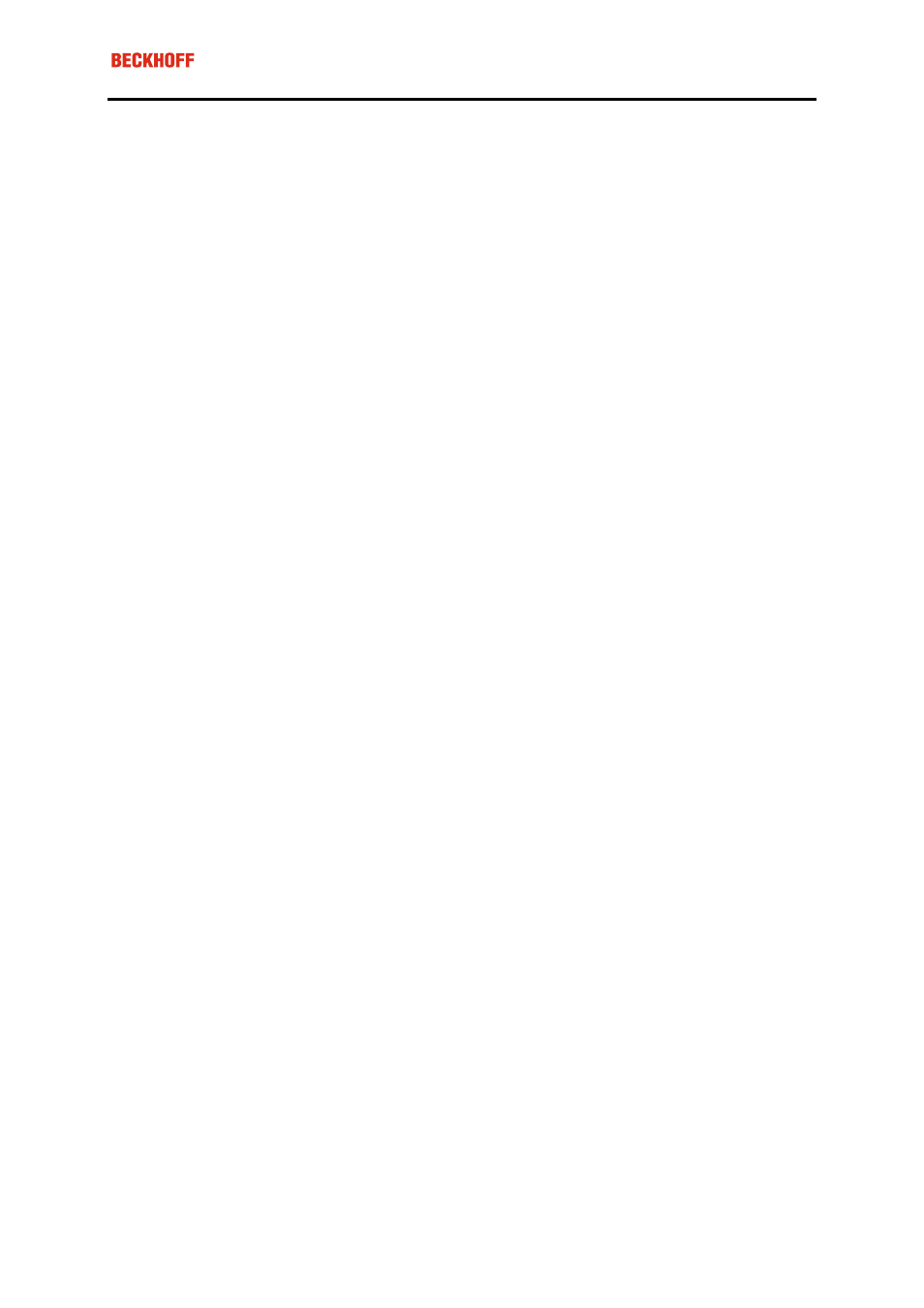
Eiserstraße 5 / D-33415 Verl / Telefon 05246/963-0 / Telefax 05246/963-149
74
Test 3:
Determine the resistance between CAN high and CAN low - at each device, if necessary.
If the measured value is greater than 65 Ohms, it indicates the absence of a terminating resistor or a break in a
signal lead. If the measured value is less than 50 Ohms, look for a short circuit between the CAN lines, more
than the correct number of terminating resistors, or faulty transceivers.
Test 4:
Check for a short circuit between the CAN ground and the signal leads, or between the screen and signal
leads.
Test 5:
Remove the earth connection from the CAN ground and screen. Check for a short circuit between the CAN
ground and screen.
Topology
The possible cable length in CAN networks depends heavily on the selected baud rate. CAN will tolerate short
drop lines - although this again depends on the baud rate. The maximum permitted length of drop lines should
not be exceeded. The length of cable that has been installed is often underestimated - estimates can even be a
factor of 10 less than the actual length. The following test is therefore recommended:
Test 6:
Measure the lengths of the drop lines and the total bus lengths (do not just make rough estimates!) and com-
pare them with the topology rules for the relevant baud rate.
Screening and earthing
The power supply and the screen should be carefully earthed at the power supply unit, once only and with low
resistance. At all connecting points, branches and so forth the screen of the CAN cable (and possibly the CAN
GND) must also be connected, as well as the signal leads. In the Beckhoff IP20 Bus Couplers, the screen is
grounded for high frequencies via an R/C element.
Test 7:
Use a DC ammeter (16 amp max.) to measure the current between the power supply ground and the screen at
the end of the network most remote from the power supply unit. An equalisation current should be present. If
there is no current, then either the screen is not connected all the way through, or the power supply unit is not
properly earthed. If the power supply unit is somewhere in the middle of the network, the measurement should
be performed at both ends. When appropriate, this test can also be carried out at the ends of the drop lines.
Test 8:
Interrupt the screen at a number of locations and measure the connection current. If current is flowing, the
screen is earthed at more than one place, creating a ground loop.
Potential differences
The screen must be connected all the way through for this test, and must not be carrying any current - this has
previously been tested.
Test 9:
Measure and record the voltage between the screen and the power supply ground at each node. The maximum
potential difference between any two devices should be less than 5 volts.
Detect and localise faults
The "low-tech approach" usually works best: disconnect parts of the network, and observe when the fault dis-
appears.
However, this does not work well for problems such as excessive potential differences, ground loops, EMC or
signal distortion, since the reduction in the size of the network often solves the problem without the "missing"
piece being the cause. The bus loading also changes as the network is reduced in size, which can mean that
external interference "hits" CAN telegrams less often.
Diagnosis with an oscilloscope is not usually successful: even when they are in good condition, CAN signals
can look really chaotic. It may be possible to trigger on error frames using a storage oscilloscope - this type of
diagnosis, however, is only possible for expert technicians.
Protocol problems
In rare cases, protocol problems (such as faulty or incomplete CANopen implementation, unfavourable timing at
boot up etc.) can be the cause of faults. In this case it is necessary to trace the bus traffic for evaluation by a
CANopen experts - the Beckhoff support team can help here.
A free channel on a Beckhoff FC5102 CANopen PCI card is appropriate for such a trace - Beckhoff make the
necessary trace software available on the internet. Alternatively, it is of course possible to use a normal com-
mercial CAN analysis tool.