Pushbutton, rotary scales >360 degrees, Setup and calibration – MicroE Mercury II 6000V User Manual
Page 10
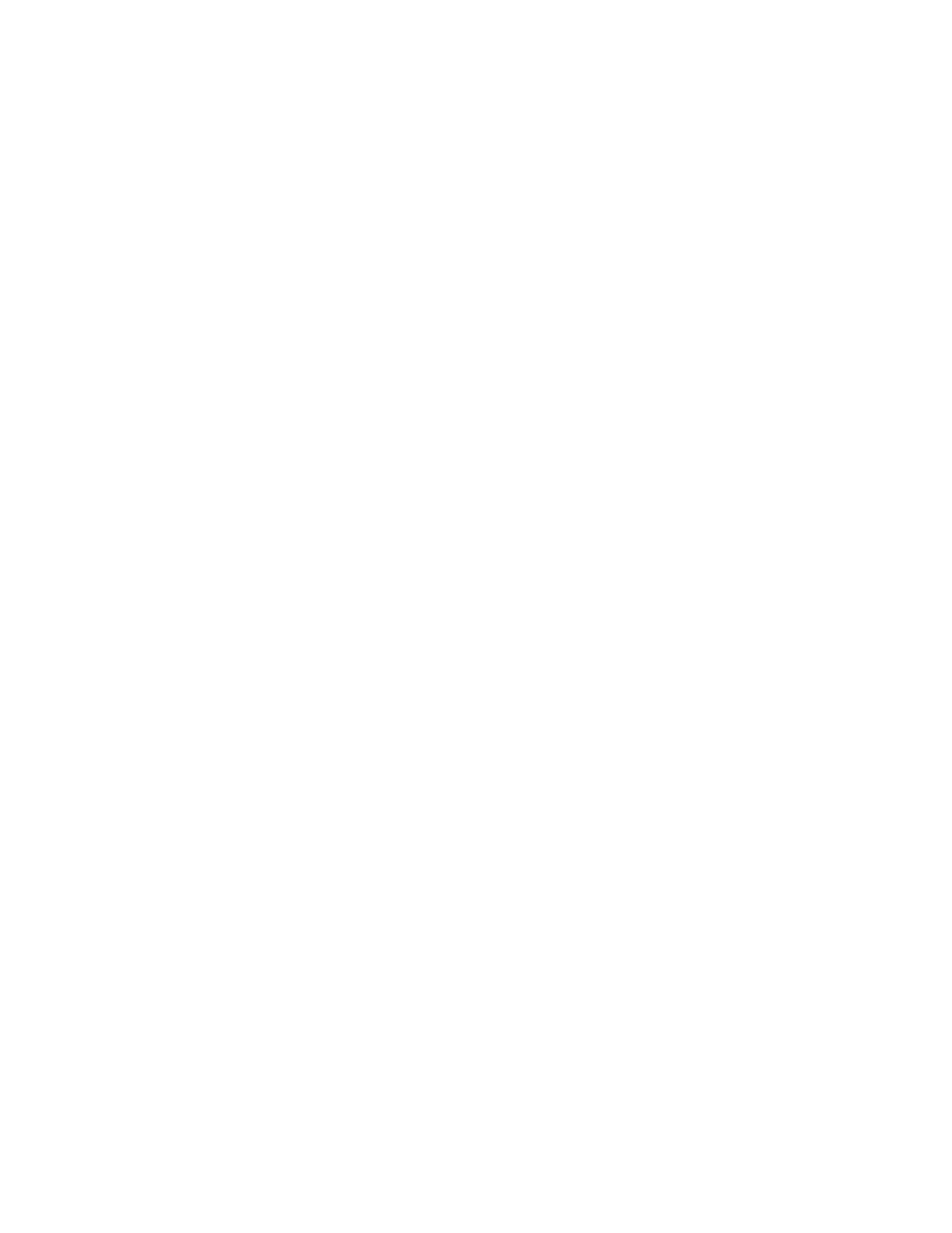
Page 10
Setup and Calibration -
Mercury
II
™
6000 Models – Pushbutton Setup
Section B - Sensor Head Installation, Alignment and Calibration
B2.3
MII6000 Pushbutton Setup -
Setup / Calibration -
Rotary Scales Used in
Applications >360° Without Limit Markers
Setup / calibration must be performed whenever the
sensor is moved or the scale is replaced.
N
No
ottee:: a
allll p
prro
occeed
duurreess b
beello
ow
w m
muusstt b
bee p
peerrffo
orrm
meed
d a
att
≤≤11m
m/
/ss rreella
attiivvee m
mo
ottiio
onn b
beettw
weeeenn tthhee sseennsso
orr a
annd
d tthhee
sscca
allee..
B
B2
2..3
3..1
1
To start calibration, push and hold the Cal.
button for about 10 seconds – until the three
signal LED’s blink twice to indicate that rotary
calibration has been activated.
B
B2
2..3
3..2
2
Move the sensor 50mm to perform Gain /
Offset / Phase calibration. After calibration
both limit LED’s come on steady. Move the
sensor back and forth if your scale has a
circumference of <50mm.
B
B2
2..3
3..3
3
Move the sensor to an area of the scale away
from the index marker. Push the Cal. button
once quickly. The Power/Cal. LED will start
blinking quickly.
B
B2
2..3
3..4
4
Move the sensor over the index up to 20
passes (one pass is a cycle back and forth).
The Power/Cal. LED and both limits LED’s will
start to blink in sets of three.
B
B2
2..3
3..5
5
Move the sensor away from the index and
press the Cal. button once quickly. The
Power/Cal. LED and both limit LED’s will start
to blink in sets of two.
B
B2
2..3
3..6
6
Move the sensor over the index once. The
LED’s will change to Power/Cal. LED and
both limit LED’s blinking just once.
B
B2
2..3
3..7
7
Make a full revolution of the rotary scale
in order to go over the index again in the
same direction. The two passes over the
index must be at least 1000 20μm fringes
apart (equivalent of 20mm linear travel), if
they are not the Alignment Tool will wait
for another pass that is 1000 fringes from
the first.
B
B2
2..3
3..8
8
The encoder is now ready for connection
to the controller for use in servo control.
N
No
ottee:: tto
o sskkiip
p a
annyy p
po
orrttiio
onn o
off tthhiiss cca
alliib
brra
attiio
onn a
annd
d a
annd
d m
mo
ovvee o
onn tto
o tthhee nneexxtt p
po
orrttiio
onn,, p
puusshh a
annd
d hho
olld
d tthhee C
Ca
all.. b
buutttto
onn
ffo
orr ttw
wo
o sseecco
onnd
dss..