3 peakup errors – Research Concepts RC2000A User Manual
Page 107
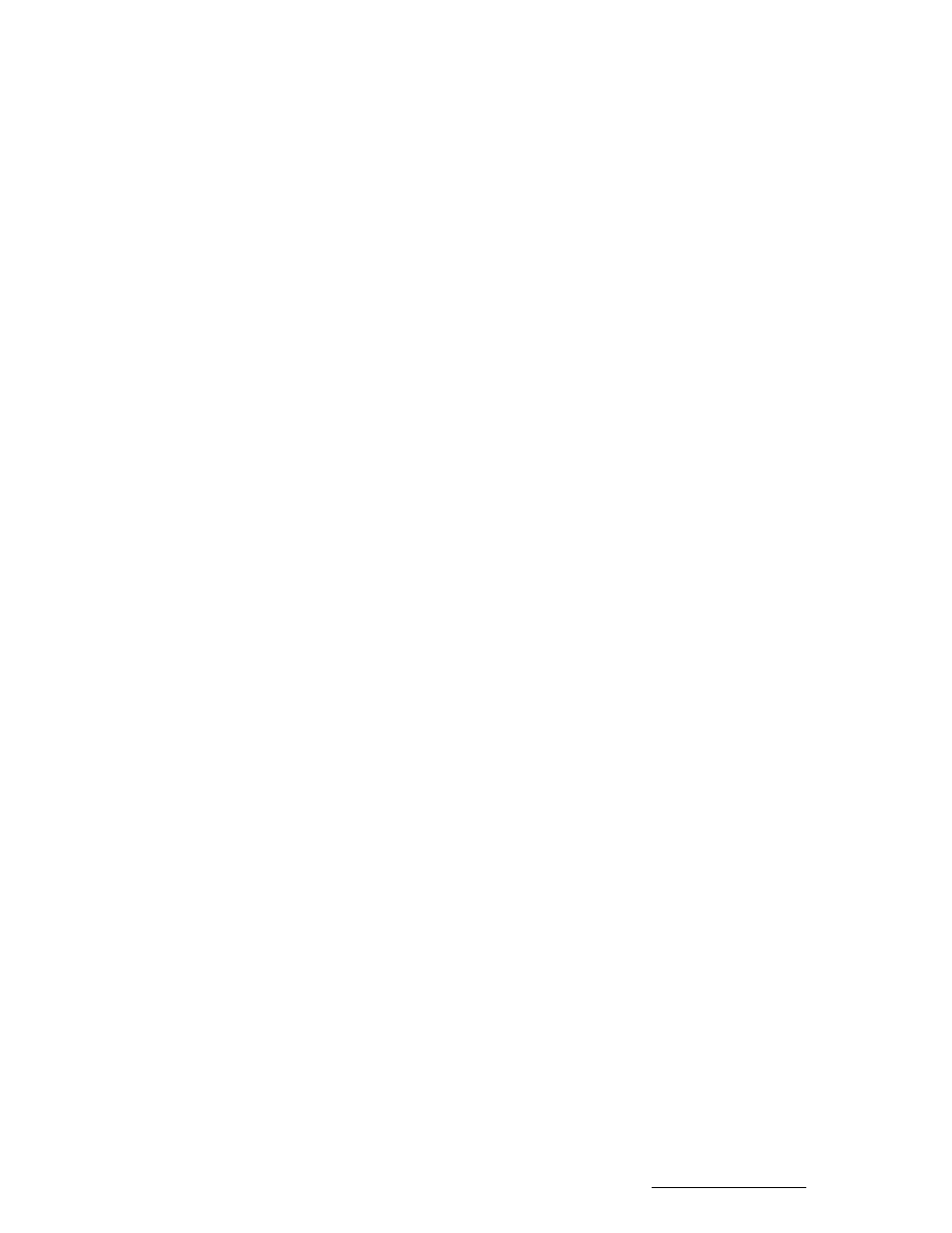
RC2000A Dual Axis Antenna Controller
Appendix I
2.6x Addendum
107
3.3 Peakup Errors
The following error conditions can cause a peakup to terminate prematurely …
Azim Alarm, Elev Alarm, or Pol Alarm … These alarms are generated whenever the controller detects a
fault for an axis. Fault conditions detected include are over-current sense, jammed (or no position pulse
feedback), or runaway. These alarms will be accompanied by a flashing error message on the bottom
row of the controller’s LCD.
Stop Key – If the Stop key is hit the peakup will be terminated. In a similar manner, a mode change in
response to a Mode key or certain serial commands will terminate a peakup.
Azimuth or Elevation Limit – If a peakup step movement will result in the controller moving outside of the
azimuth or elevation limits the terminate the peakup.
Lost Signal Strength – If the received signal strength falls below the threshold for the frequency band
specified the peakup will terminate.
Remote Commands – If a peakup initiated by a remote command received via the serial port is in
progress and another remote command is received which specifies azimuth, elevation, or polarization
movement the peakup in progress will be aborted.
Peak Limit Error – The controller will take up to four steps away from the initial position looking for a
peak. If a peak is not found after 4 steps the controller terminates the peaking operation. A peak limit
error is typically the result of too small of step size. The following section discusses step size selection.
3.4 Poor Peakup Performance – The Importance of Proper Step Size
Selection
The peakup performance is determined by proper selection of the Az/El Step Size CONFIG mode
items. Several factors will govern step size selection including signal fading, the noise voltage present
on the analog signal strength input, and the mount’s mechanical hysteresis (sometimes referred to as
‘slop’).
For a given axis, the pointing accuracy of the antenna can be no greater than one half the step size
used for peaking about that axis. Based on this it would seem that the smallest possible step size, 1
position count, would yield the greatest possible accuracy. In the absence of signal fading, noise on the
controller’s AGC input, and hysteresis, this would be the case.
3.4.1 How Signal Fading, Noise, and Mechanical Hysteresis Affect Peakup
Performance
To see how these factors affect the peaking process it is useful to review the basic peaking operation.
When peaking the antenna, the controller measures the received signal strength by averaging for 3
seconds, moves the antenna by an amount equal to the azimuth or elevation step size for the frequency
band of the current satellite, and then makes another measurement of signal strength by averaging for 3
seconds. If the signal strength measured after the move is greater than the signal strength measured
before the move, the controller assumes that the movement resulted in the antenna being brought
closer to the antenna peak position. Signal fades, noise, and mechanical hysteresis can sometimes
result in the controller measuring greater signal strength when the antenna is moved away from the
satellite. This event is referred to as a ‘bad decision’ by the controller.
Signal Fading
Fading refers to the variation in received signal strength due to atmospheric conditions. The affects of
fading are usually greater at higher frequencies. Moisture in the form of clouds, fog, or precipitation
contribute to fading. The changes in signal strength associated with fading can occur over periods of
time measured in seconds, minutes, or even hours. It is the short term time variations in signal strength
that can cause the controller to make a bad peaking decision.
Research Concepts, Inc. • 5420 Martindale Road • Shawnee, Kansas • 66218-9680 • USA www.researchconcepts.com