Flowserve ISC User Manual
Page 13
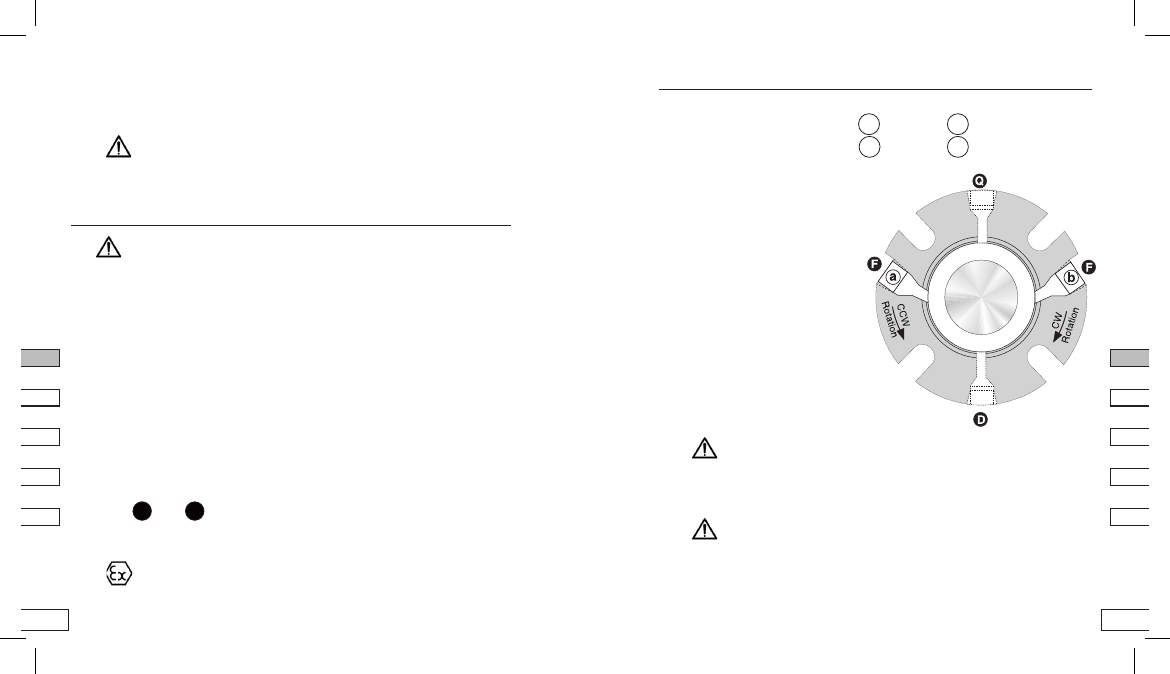
25
pump impeller is reset or when the seal is removed for repairs.
6.0 Turn the shaft by hand to ensure unobstructed operation.
6. See Operational Recommendations before start-up.
Conduct a static pressure test. Do not exceed the max.
pressures.
7. Single Seal Piping and Functional Recommendations
7.
Install an adequate seal flush system. Ensure that piping is
connected to the correct pipe ports to prevent unsafe situa-
tions. The connections on the mechanical seal are properly
marked.
The ISC requires a clean cool environment for maximum seal life.
With a clean cool product, use a bypass flush from the pump
discharge (API plan ) or a bypass flush to the pump suction
(API plan 3). With clean hot products use a bypass flush through
a cooler (API plan 2). With abrasive products or products that
are incompatible with the seal, use a flush from a clean external
source (API plan 32).
7.2 Use flush port that coincides with gland markings and direction of
equipment rotation. Plug extra NPT opposite of flush (see Figure
7).
7.3 Taps
Q
and
D
in the gland are quench and drain ports used for
fluid quenching, ASME Flush Plan 7362. If they are not used, they
should be plugged with pipe plugs.
Escaping leakage must not form an explosive mixture.
24
Shaft rotation from exposed end of gland
Inlet
Plugged Port
Clockwise (CW)
Port
b
Port
a
Counterclockwise (CCW) Port
a
Port
b
7.4 Remove lock outs on
pump and valves.
7.5 Do not start up the equip-
ment dry to check motor
rotation, etc. Open valves
to flood pump with product
fluid. Ensure that the seal
flush system is operating.
Vent air from the casing
of the pump and the seal
chamber before start-up.
It must be ensured that the machine is protected against pen-
etration by dust and / or that dust deposits are removed at
regular intervals so that they cannot exceed a thickness of 5
mm on the surfaces of the faces.
It must be ensured, e.g. in the form of a level monitor, that
the running chamber is completely vented and filled with fluid
in all operating states if it is to minimise the heat generated
by friction and therefore the surface temperature of the seal
elements.
Figure 7