Flowserve ISC User Manual
Page 3
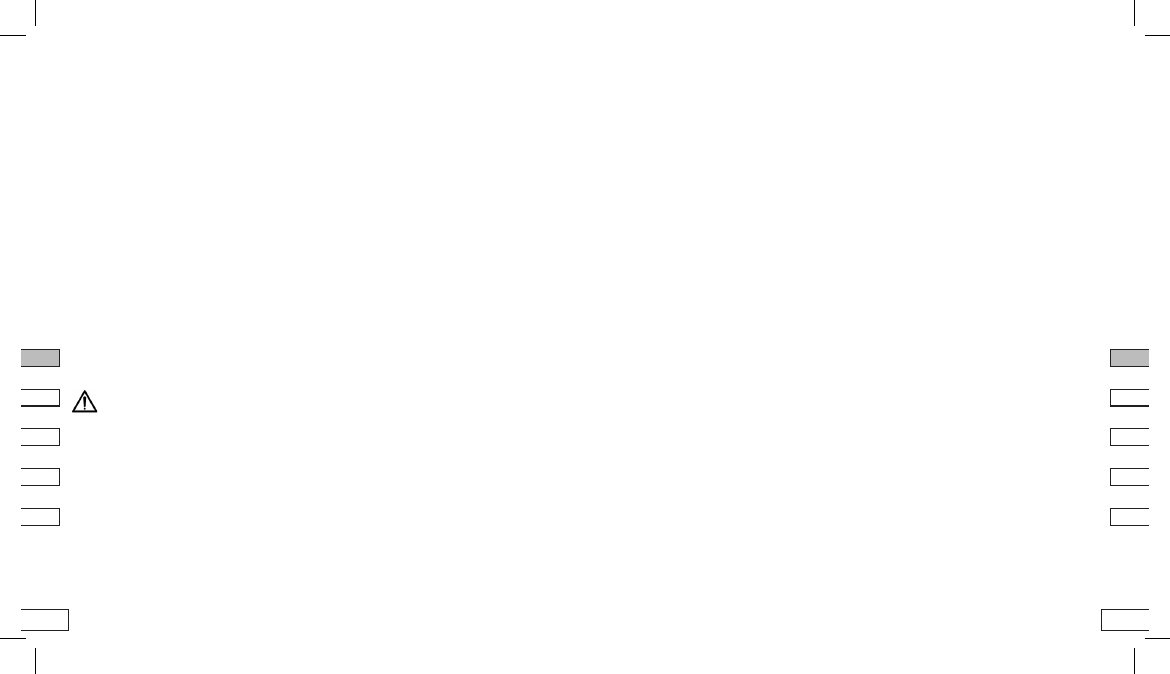
For applications which require information on expected surface
temperatures of the mechanical seal faces, Flowserve document
“ATEX 37 information declaration” is available upon request. This
document allows users to determine typical surface temperatures
based upon seal design, operating conditions and face materials
and may be used by the users to comply with ATEX 999/92/EC
(ATEX 37).
.4 Functional requirements
The proper functioning of a mechanical seal is only achieved once
the following conditions have been met:
• The sealing surfaces are lapped within specification
• Perpendicularity and concentricity between the shaft and the
seal chamber face and bore respectively
• Freedom of movement of the spring loaded components in axial
direction
• Axial and radial shaft movements within Flowserve or OEM tole-
rances whichever is the tightest.
• The seal is run under the conditions for which it was selected.
• The equipment in which the seal(s) is (are) installed is run
within normal parameters (no cavitation, excess vibration etc.)
• Prevention of sedimentation on shaft or sleeve surfaces caused
by for instance crystallisation or polymerisation
• Permanent seal liquid film between the sealing surfaces
!
If these function conditions are not fulfilled, the consumption of
product, for example, is increased and parts of the product can
escape into the atmosphere. Other effects can include high com-
ponent temperatures.
and (depending on the design) a spring-loaded element. The
spring-loaded element can be a spring or a bellows. The seal ring
is sealed against the housing with a secondary gasket, e.g. an
O-ring. The rotating components will consist of a seal ring and
(depending on the design) a spring-loaded element. The spring-
loaded element can be a spring or a bellows. The seal ring is
sealed against the shaft with a secondary gasket, e.g. an O-ring.
A mechanical seal can be supplied as a pre-assembled cartridge
or in separate components. Assembly is done in accordance with
the assembly drawing. A mechanical seal will run in the pumped
product or external source fluid.
To provide lubrication, a film of liquid must always be present
between the seal faces. The sealing surfaces are separated from
each other by the seal liquid film during shaft rotation and in
principle run without contact and thus minimal wear under these
conditions.
.3 Explosion Protection
The ISC mechanical seal is a standard cartridge seal and as such
regarded as a machine element. Machine elements do not need to
comply with Directive 94/9/EC (ATEX 95 product guide) as these
are regarded as an integral part of a larger piece of machinery
(pump, agitator). This has been confirmed by both the EC ATEX
standing committee as well as the European Sealing Association
(ESA).Reference is made to following web-sites:
EC ATEX standing committee:
http://ec.europa.eu/enterprise/atex/rotating.htm
ESA position statement:
http://www.europeansealing.com/statements.html
5
4