1) latch command (38h) – Yaskawa Sigma-5 User Manual: MECHATROLINK-II Commands User Manual
Page 80
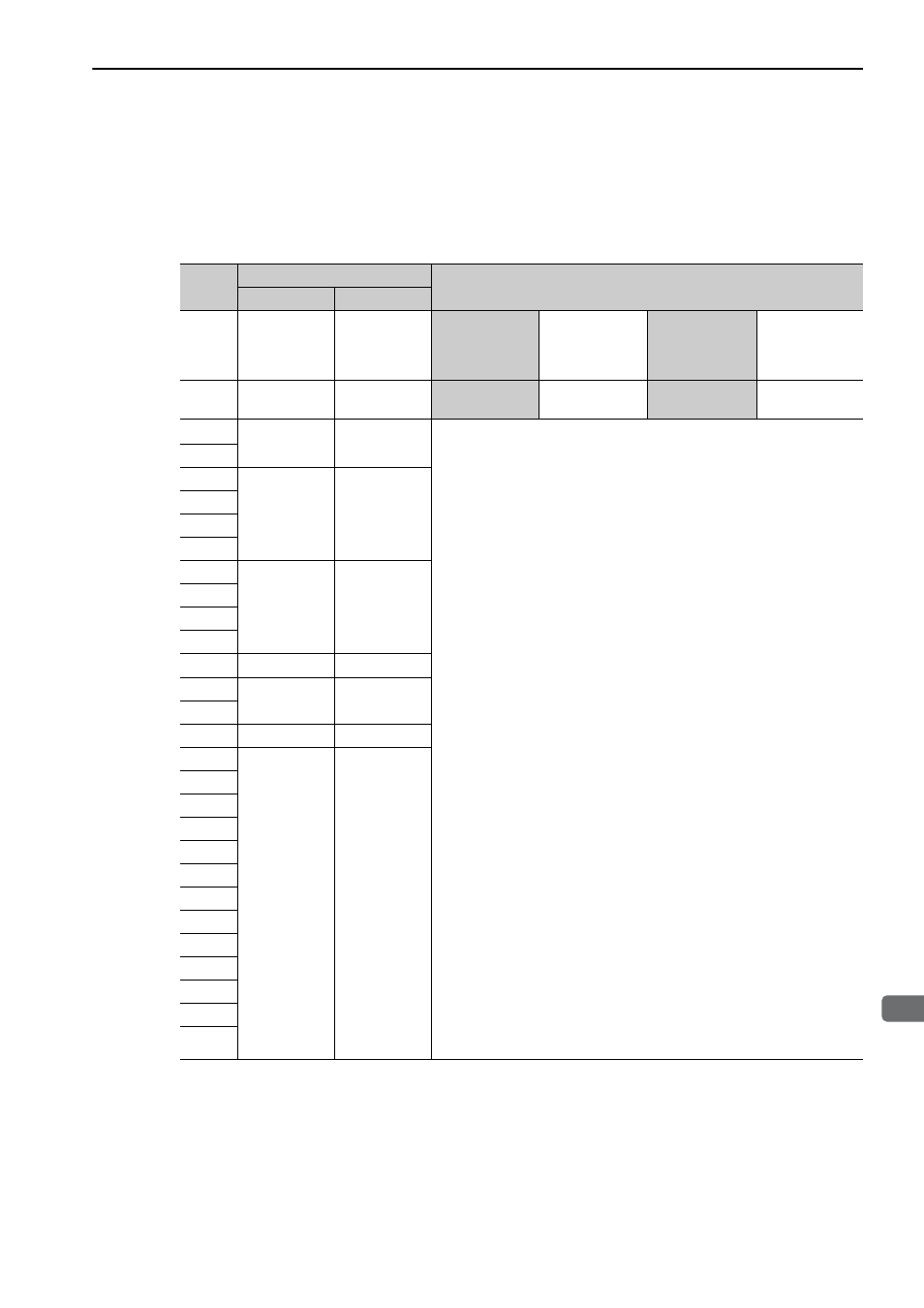
4.2 Motion Commands Details
4-15
4
Motion Commands for Operation
4.2.7 Interpolation Feeding with Position Detection (LATCH: 38H)
(1) LATCH Command (38H)
The LATCH command is used to start interpolation feeding and to latch the current position when the external
signal is input during positioning.
Speed feed forward, torque (force) feed forward, and torque (force) limit can be applied.
Byte
LATCH
Description
Command
Response
1
38H
38H
Phases in
which the
command can
be executed
Phase 3
Synchronization
classification
Synchronous
command
2
LT_SGNL
ALARM
Processing
time
Within commu-
nications cycle
Subcommand
Can be used
3
OPTION
STATUS
• Use LT_SGNL to select the latch signal.
For details on LT_SGNL, refer to 7.1.6 LT_SGNL Specifications.
The position data when the latch signal is input is stored in the feedback
latch position (LPOS) and is forcibly output to MONITOR2 for one com-
munications cycle.
• OPTION field can be used.
• Interpolation feeding is performed by specifying the target position
(TPOS) every communications cycle.
The target position (TPOS) is a signed 4-byte data.
Note: The target position is not an incremental value (travel amount), but
the absolute position in the reference coordinate system.
• The speed feed forward (VEF [reference units/s]) is a signed 4-byte data.
• Either torque (force) feed forward (TFF) or torque (force) limit (TLIM)
can be used. It can be selected by setting Pn81F and Pn002.
- TLIM setting range: 0 to 4000H [maximum motor torque (force)/
4000H]
(If a value between 4000H and FFFFH is set, the maximum motor
torque (force) will be applied as the limit.)
Use the ADJ command to obtain the maximum motor torque (force).
- TFF setting range: A signed 2-byte data [maximum motor torque
(force)/4000H]
• Use DEN (output complete) to confirm the completion of position refer-
ence output.
• When a command in execution is switched to another command, the feed
forward values (VFF and TFF) will be cleared.
• A warning will occur and the command will not be executed in the fol-
lowing cases.
- The command is used in a phase other than phase 3: Command warning
1 (A.95A)
- The command is sent while the servo is OFF: Command warning 1
(A.95A)
- The travel amount (Target position (TPOS) - Current position (IPOS))
exceeds the limit: Data setting warning 2 (A.94B)
- When using SigmaWin or a digital operator for motor operations such
as JOG: Command warning 1 (A.95A)
• Latch time lag
- From reception of the command to latching start: 250
μs max.
- From completion of latching to transmission of a response: One com-
munications cycle max.
4
5
TPOS
MONITOR1
6
7
8
9
VFF
MONITOR2
10
11
12
13
SEL_MON1/2 SEL_MON1/2
14
TFF/TLIM
IO_MON
15
16
WDT
RWDT
17
Subcommand
area
Subcommand
area
18
19
20
21
22
23
24
25
26
27
28
29