Flowserve QLQ Vertical Worthington User Manual
Page 28
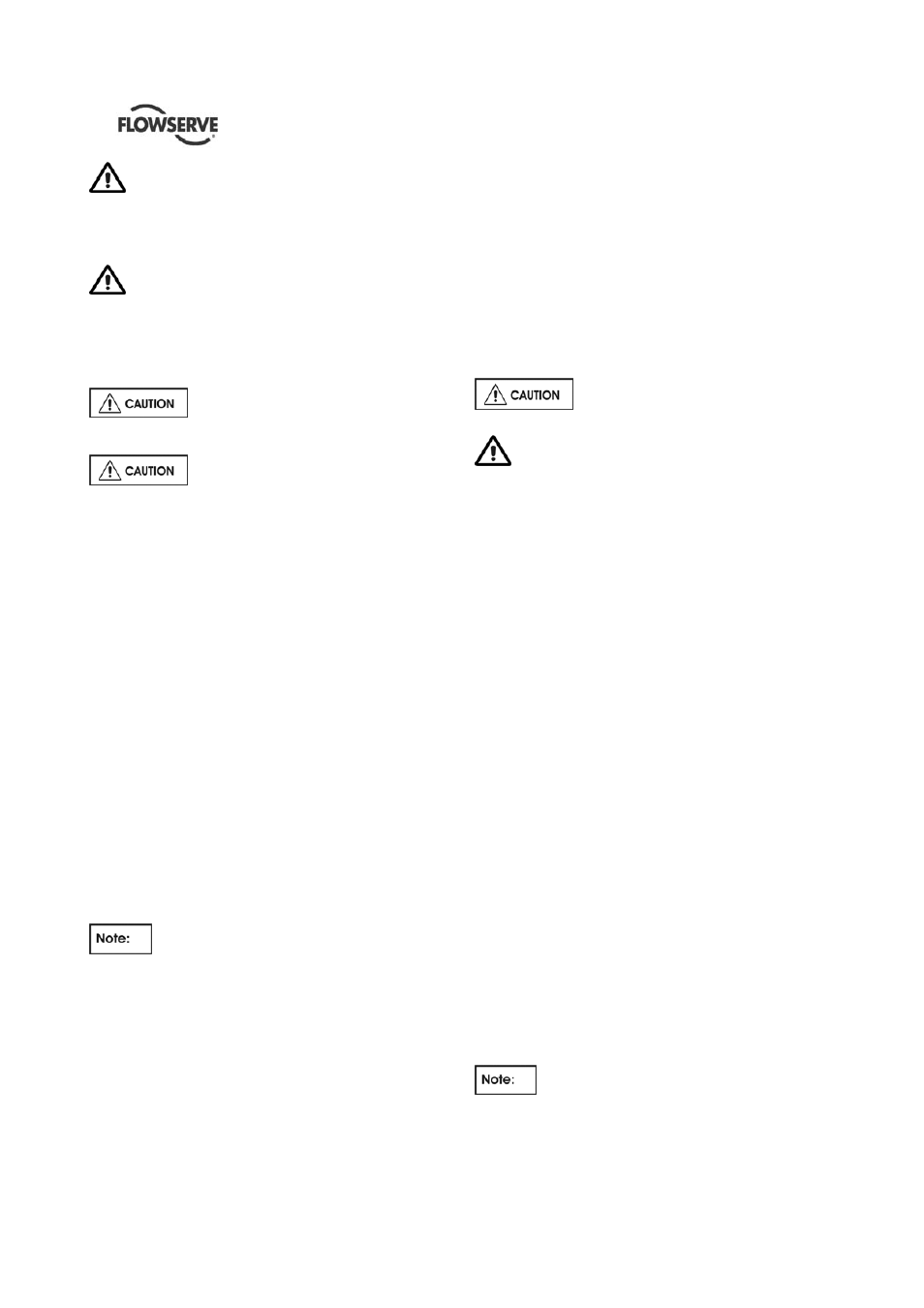
QLQ, QLQC USER INSTRUCTIONS ENGLISH 87900027 – 06/14
Page 28 of 61
Complete piping as below and see sections up
to and including section 5, “Commissioning, startup,
operation and shutdown” before connecting driver
and checking actual rotation.
Once the alignment has been completed,
proceed dowelling the motor stand to the discharge
head.
4.6 Piping
Never use the pump as a support for
piping.
Protective covers are fitted to the pipe
connections to prevent foreign particles or objects
entering the pump during transportation and
installation. Ensure that these covers are removed
from the pump before connecting pipes.
4.6.1 General
These units are furnished for a particular service
condition. Changes in the hydraulic system may
affect performance adversely. This is especially true if
the changes reduce the pressure at the suction or if
the liquid temperature is increased. In case of doubt
contact FLOWSERVE.
Discharge and suction (if installed) piping should be
of ample size, be installed in direct runs, and have a
minimum of bends. Double bends must be avoided in
suction line and a straight run of pipe, equal 8 to 10
times the pipe diameter is desired directly upstream
of the suction nozzle.
In order to minimize friction losses and hydraulic
noise in the pipework it is good practice to choose
pipework that is one or two sizes larger than the
pump suction and discharge. Typically main pipework
velocities should not exceed 2 m/s (6 ft./sec) suction
and 3 m/s (9 ft./sec) on the discharge.
Provision must be made to support piping
external to the pump to prevent excessive nozzle
loads, maintain pump/driver alignment and avoid pipe
induced vibrations.
Take into account the available NPSH which must be
higher than the required NPSH of the pump.
Maximum forces and moments allowed on the pump
flanges vary with the pump size and type. The
maximum allowable values allowed are stated in the
General Arrangement Drawing provided in the
Instruction Manual Book.
To minimize these forces and moments that may, if
excessive, cause misalignment, hot bearings, worn
couplings, vibration and the possible failure of the
pump casing, the following points should be strictly
followed:
Prevent excessive external pipe load
Never draw piping into place by applying force to
pump flange connections
Do not mount expansion joints so that their force,
due to internal pressure, acts on the pump flange
Ensure piping and fittings are flushed
before use.
Ensure piping for hazardous liquids is arranged
to allow pump flushing before removal of the pump.
4.6.2 Suction piping (if applicable)
a) The inlet pipe should be one or two sizes larger
than the pump inlet bore and pipe bends should
be as large radius as possible.
b) Keep the suction pipe free of all air pockets.
(Vent is required).
c) Pipework reducers should have a maximum total
angle of divergence of 15 degrees.
d) The piping should be inclined up towards the
pump inlet with eccentric reducers incorporated
to prevent air locks.
e) Flow should enter the pump suction with uniform
flow, to minimize noise and wear.
f) Except if considerable foreign matter is expected
strainers are not recommended in inlet piping.
Inlet strainers, when used, should have a net
“free area” (see section 4.6.2.1).
4.6.2.1 Suction strainer
In a new installation, great care should be taken to
prevent dirt, scale, welding beads and other items
from entering the pump, as it is particularly important
to protect the numerous close running fits from
abrasive matter present in new piping.
The suction system should be thoroughly flushed
before installing the suction strainer and making up
suction piping to the pump.
The suction strainer should be installed between 5 to
20 pipe diameters upstream from the pump suction
flange.
The open area of the strainer should
have a minimum of a 3 to 1 ratio to the area of the
pump suction.