Flowserve QLQ Vertical Worthington User Manual
Page 40
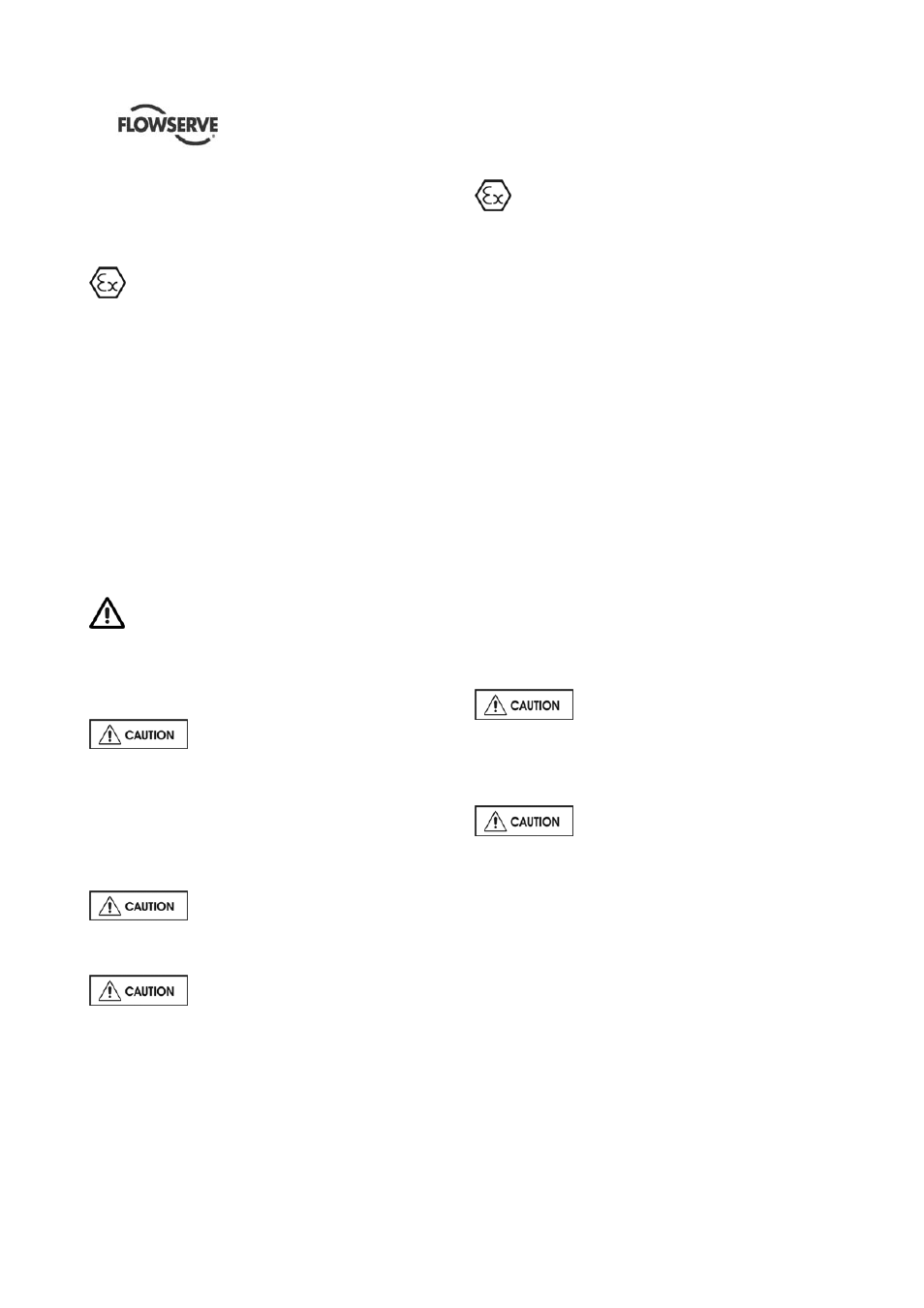
QLQ, QLQC USER INSTRUCTIONS ENGLISH 87900027 – 06/14
Page 40 of 61
5.9.2 Pumps fitted with packed glands
If the pump has a packed gland, there must be some
leakage from the gland. Gland nuts should initially be
finger-tight only. Leakage should take place soon
after the stuffing box is pressurized.
The gland must be adjusted evenly to give
visible leakage and concentric alignment of the gland
ring to avoid excess temperature. If no leakage takes
place, the packing will begin to overheat.
If overheating takes place, the pump should be
stopped and allowed to cool before being re-started.
When the pump is re-started, check to ensure
leakage is taking place at the packing gland.
If hot liquids are being pumped it may be necessary
to loosen the gland nuts to achieve leakage.
The pump should be run for 30 minutes with steady
leakage and the gland nuts tightened by 10 degrees
at a time until leakage is reduced to an acceptable
level, normally a minimum of 40-60 drops per minute
is required.
Care must be taken when adjusting the gland
on an operating pump. Safety gloves are essential.
Loose clothing must not be worn to avoid being
caught by the pump shaft. Shaft guards must be
replaced after the gland adjustment is complete.
Never run gland packing dry, even for
a short time.
5.9.3 Pumps fitted with mechanical seal
Mechanical seals require no adjustment.
Before pumping dirty liquids, it is advisable, if
possible, to run in the pump mechanical seal using
clean liquid to safeguard the seal face.
External flush or quench should be
started before the pump is run and allowed to flow for
a period after the pump has stopped.
Never run a mechanical seal dry, even
for a short time.
5.9.4 Pump and motor bearing temperature
If the pumps are working in a potentially
explosive atmosphere, temperature or vibration
monitoring at the bearings is recommended.
If pump bearing temperatures (such as thrust
bearings) are to be monitored it is essential that a
benchmark temperature is recorded at the
commissioning stage and after the bearing
temperature has stabilized. Typical alarm set:
set the alarm at 80 °C (180 °F) and the trip at 90
°C (194 °F) for high ambient temperature and/or
hot service
When the bearing temperature sensor is provided:
set the alarm at 95 °C (200 °F) and the trip at 105
°C (220 °F)
It is important, particularly with grease lubrication, to
keep a close watch on the bearing temperatures.
After startup the temperature rise should be gradual,
reaching a maximum after approximately 1.5 to 2
hours. This temperature should then remain constant
or marginally reduce with time.
5.10 Stopping and shutdown
a) Stop
the
driver.
b) Close the discharge valve.
c) Switch off flushing and/or cooling/heating liquid
supplies at a time appropriate to the process.
For prolonged shutdowns and
especially when ambient temperatures are likely to
drop below freezing point, the pump and any cooling
and flushing arrangements must be drained or
otherwise protected.
5.11 Hydraulic, mechanical and electrical
duty
This product has been supplied to meet the
performance specifications of your purchase order,
however it is understood that during the life of the
product these may change. The notes on
subsections below may help the user decide how to
evaluate the implications of any change. If in doubt
contact your nearest Flowserve office.