Flowserve QLQ Vertical Worthington User Manual
Page 32
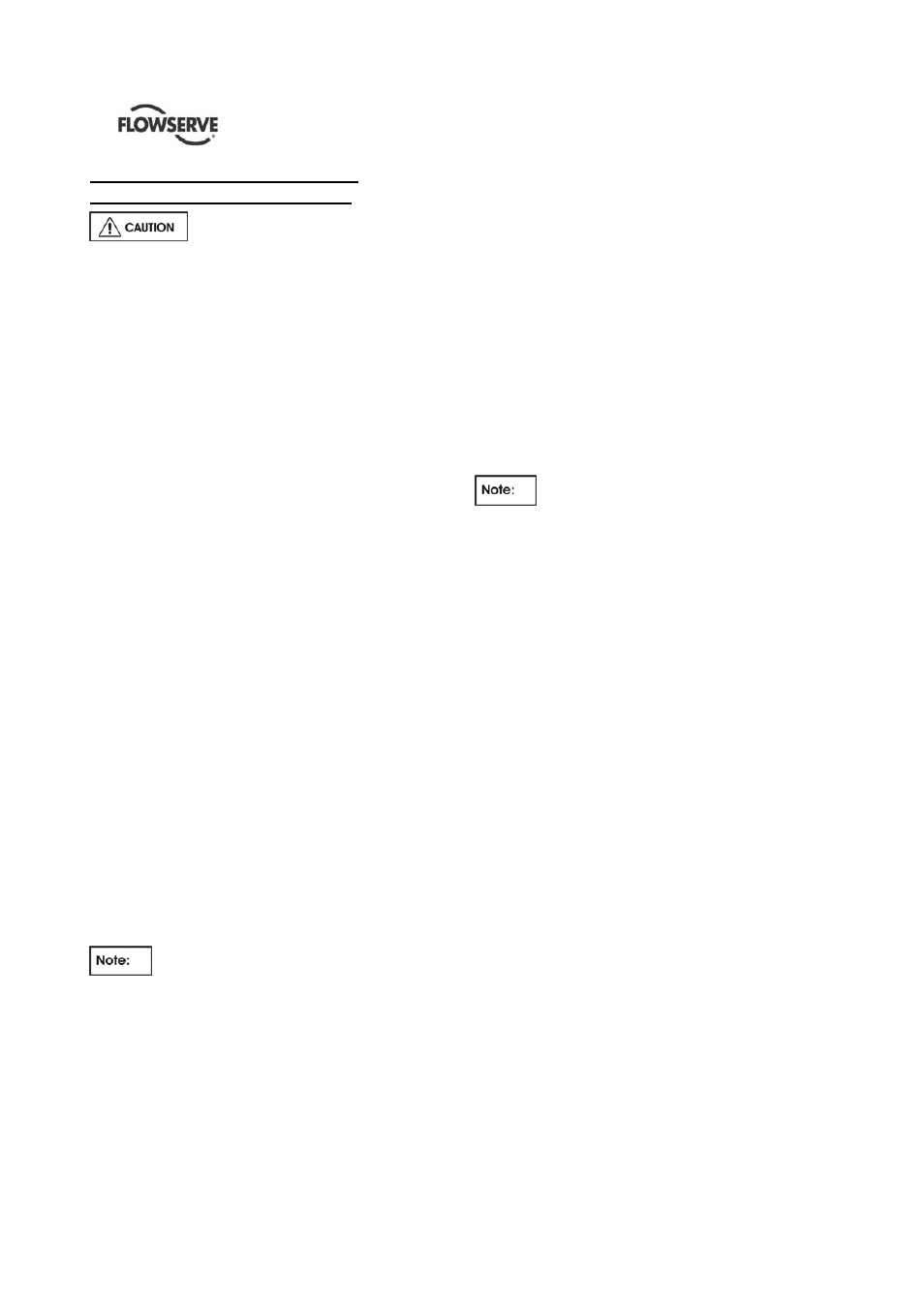
QLQ, QLQC USER INSTRUCTIONS ENGLISH 87900027 – 06/14
Page 32 of 61
5 COMMISSIONING, STARTUP,
OPERATION AND SHUTDOWN
These operations must be carried out
by fully qualified personnel. Turn off power supply for
safety while pump commissioning is in progress.
5.1 Pre-commissioning procedure
The gland is to be filled with grease and flush supply
to be in place. Flush piping to be checked for leaks.
Mechanical seals to be checked for leaks, flush flow
and pressure.
a) Pumps with the enclosing tubes and oil-lubed
bearings must be filled with the proper lubricant to
avoid running dry and to guarantee acceptable
performance of the pump. A separate oil tank is
attached to the pump (see detail in section 5.2.2).
b) For can pumps check all vent connections for
complete filling of the pump. The venting procedure
can take from 10 minutes up to 2 hours, depending
on the kind of fluid (except cryogenic service).
c) Check the direction of rotation of the pump
(Coupling spacer dismantled). Should be counter
clockwise when viewed from the driver end.
d) The pump rotor and the shaft seal must be in
correct axial position.
e) Check the readiness of all auxiliary systems (seal
sys., lubrication system etc.,) for startup.
f) All pipe work including the internal and the auxiliary
pipe work must be connected correctly and must
be absolutely tight. Check the tightness of all
connections of the auxiliary pipe work. The suction
valve must be open, the discharge valve shall be
closed or partially open as required.
g) Turn the pump by hand, if required with the help of
a lever, to check the free rotation of the rotor. The
rotor must turn uniformly and noiselessly. Some
resistance may be felt due to the friction in the
bearings and seals.
h) Check the readiness of the driver for startup. Refer
to the manual for the driver to be sure that all
precautions are in place to energize the motor.
5.2 Pump Lubricants
Re-checking the motor lubrication should
be in accordance with the motor manufacturer’s user
instructions supplied separately with the pump.
5.2.1 Open lineshaft lubrication
Open lineshaft bearings are lubricated by the pumped
fluid on short-coupled units less than 15 m (50 ft.) long
and will usually not require pre or post-lubrication.
Care is to be taken to ensure that the gland or seal is
supplied with the required flush flow.
All open lineshaft pumps where the static water level is
more than 15 m (50 ft.) below the discharge head
should be adequately pre-lubricated before starting the
pump.
Pre-lubrication shall be provided either by pumped
fluid (through a special piping fitted on the discharge
head, to be connected to the discharge piping) or by
clean external source (water or oil) from auxiliary lines
or dedicated tank.
Refer to the specific description on the dedicated
documents of the pump.
It is the responsibility of the User to install a
reliable pre- lube system to achieve the pump pre-
lubrication. Flowserve will not supply these types of
systems or accessories with the pump, unless
otherwise agreed.
5.2.2 Enclosed shaft lubrication
QLQs with the enclosed shafting are lubricated by a
dedicated oil supply system or injection lubricated by
extraneous liquid; usually clean water to meet the
application requirements.
On water pumps, the suction bearing on the bowl
assembly should be repacked when required. Pumps
that pump hydrocarbons or have carbon, rubber,
epoxy or Teflon suction bearings do not have the
suction bearings packed. If the pump will be started
after a longer storage period, the bearings should be
first flushed and cleaned by using a suitable cleaning
agent. It is not necessary to remove the oil sprayed
for short or long-term storage as this will mix up
thoroughly with the lubrication oil.
5.2.2.1 Oil lubricated pumps
The lubricating oil must be available and should be
allowed to run into the enclosing tube in sufficient
quantity to thoroughly lubricate all lineshaft bearings.
The gravity flow system is the most commonly utilized
system for oil.
The oil reservoir (example shown in detail below)
must be kept filled with a good quality light turbine oil
(about 30 cSt) at the operating temperature and
adjusted to feed a minimum of 3 drops per minute per
30 m (100 ft.) of column length, but not to exceed 5
drops per minute.