Flowserve QLQ Vertical Worthington User Manual
Page 53
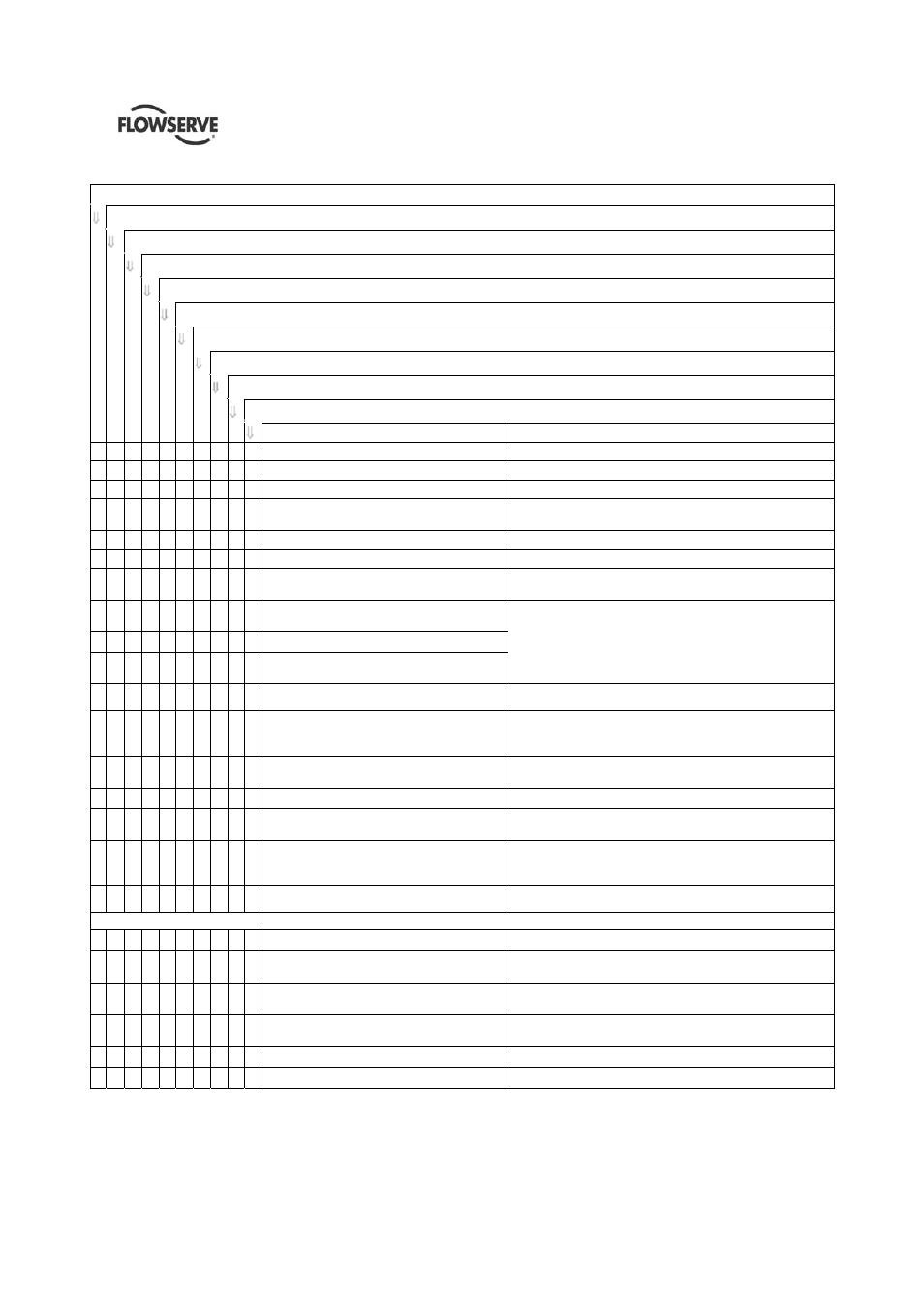
QLQ, QLQC USER INSTRUCTIONS ENGLISH 87900027 – 06/14
Page 53 of 61
FAULT SYMPTOM
P u m p o v e r h e a t s a n d s e i z e s
P u m p w i l l n ot r u n
P u m p v i b r a t e s o r i s n o i s y
M e c h a n i c a l s e a l h a s s h ort l i f e
M e c h a n i c a l s e a l le a k s ex c e s s i ve l y
P u m p r e q u i r e s e x c e s s i ve p ow e r
Mo t o r O ve r l o a d e d
I n s uf f i c i e n t p re s s u re d e ve l o p e d
I n s uf f i c i e n t ca p a c i t y d e l i ve re d
Pu m p ru n s b ut d o e s n o t d e l i ve r l i q u i d
POSSIBLE CAUSES
POSSIBLE REMEDIES
Wearing ring surfaces worn.
Replace worn wear ring/surfaces.
Impeller damaged or eroded.
Replace. or consult Flowserve for an upgrade.
Leakage under sleeve due to joint failure.
Replace joint and check for damage.
Shaft sleeve worn, scored, or running off
center.
Check and renew defective parts.
Mechanical seal improperly installed.
Check alignment of faces/damaged parts/assembly
Incorrect type of mechanical seal.
Consult Flowserve.
Shaft running off center because of worn
bearings or misalignment.
Check misalignment and correct if necessary. If alignment
satisfactory check bearings for excessive wear.
Impeller out of balance resulting in
vibration.
Check. Consult Flowserve for problem resolution ideas
.
Solids/Abrasive particles in liquid pumped.
Internal misalignment of parts preventing
seal ring and seat from mating properly.
Mechanical seal was run dry.
Check mechanical seal/flush supply/pump and repair.
Internal misalignment due to improper
repairs causing impeller to rub.
Check method of assembly, possible damage or state of
cleanliness during assembly. Check and consult
Flowserve, if necessary.
Excessive thrust caused by a mechanical
failure inside the pump.
Check wear condition of impeller, its clearances and liquid
passages.
Excessive grease in ball bearings.
Check method of re-greasing.
Lack of lubrication for bearings.
Check hours run since last change of lubricant, the
schedule and its basis.
Improper installation of bearings (damage
during assembly, incorrect assembly, wrong
type of bearing etc.).
Check method of assembly, possible damage or state of
cleanliness during assembly and type of bearing used.
Remedy and consult Flowserve, if necessary.
Damaged bearings due to contamination.
Check contamination source and replace bearings.
C.
MOTOR/ELECTRICAL
PROBLEMS
Wrong direction of rotation.
Reverse 2 phases at motor terminal box.
Motor Protector open.
Check nameplate for voltage and current rating.
Replace faulty motor protectors.
Line voltage not correct/faulty control
box/wiring/low voltage.
Check wiring diagram.
Blown fuse/breaker open/dead motor/short
or loose connection.
Check/repair or replace fuses/breakers.
Motor running on 2 phases only.
Check supply and fuses.
Motor running too slow.
Check motor terminal box connections and voltage.