Flowserve QLQ Vertical Worthington User Manual
Page 38
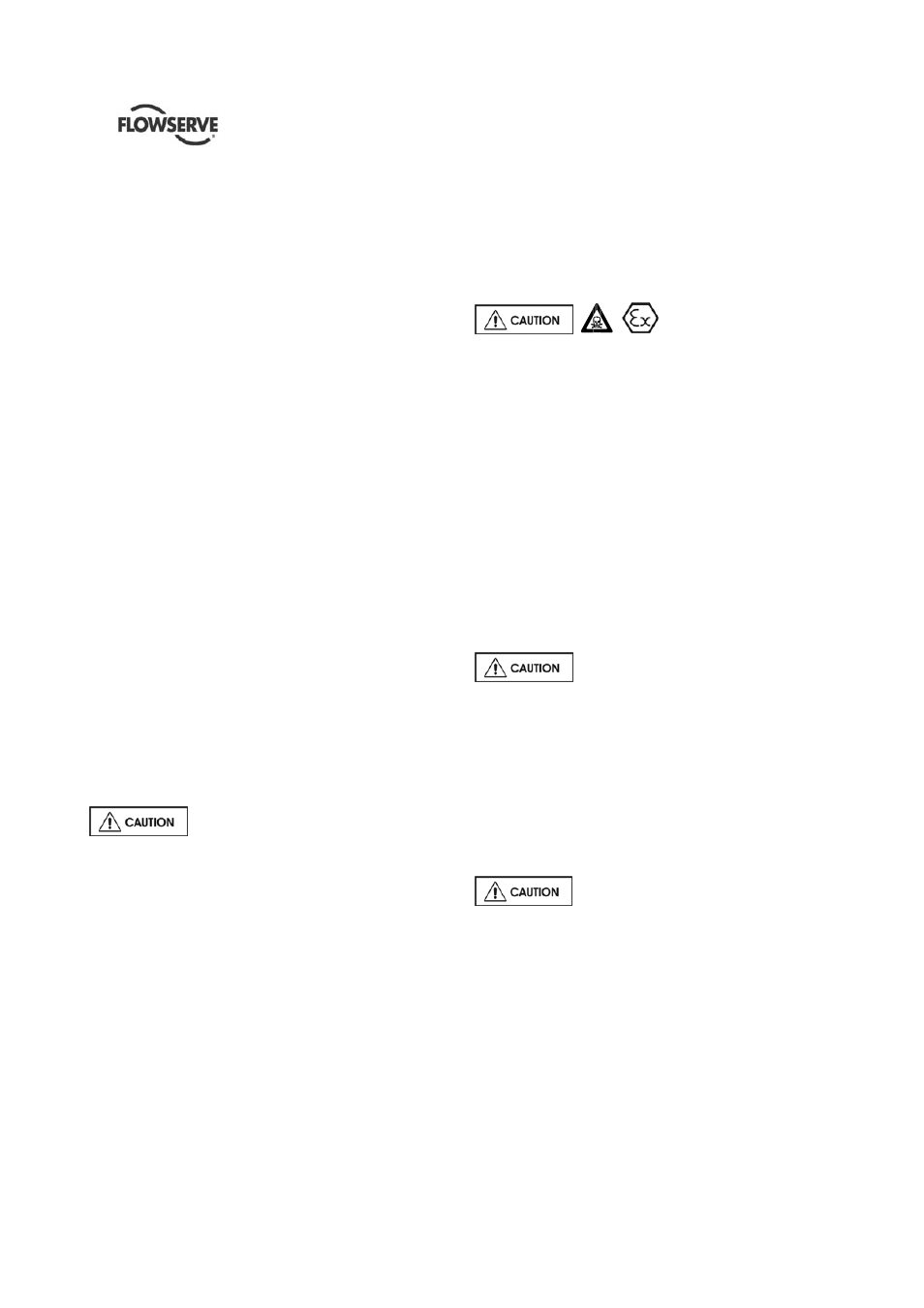
QLQ, QLQC USER INSTRUCTIONS ENGLISH 87900027 – 06/14
Page 38 of 61
After adding two or three rings of packing, or when
proper adjustment cannot be achieved, the stuffing
box should be cleaned completely of all old packing
and re-packed.
5.8.3 Open shaft lubrication before startup
Open lineshaft bearings are lubricated by the pumped
fluid on short-coupled units less than 15 m (50 ft.)
long and usually do not require pre- or post-
lubrication. All open lineshaft pumps where the static
water level is more than 15 m (50 ft.) below the
discharge head should be adequately pre-lubricated
before startup.
5.8.4 Enclosed shaft lubrication before start up
Enclosed lineshaft bearings are lubricated by an
extraneous liquid (usually oil or clean water).
The oil reservoir must be kept filled with a good
quality of light turbine oil (about 30 cSt (mm
2
/sec) at
operating temperature) and adjusted to feed 3
drops/minute for every 30 m (100 ft.) of column.
Injection systems are designed for each installation.
Injection pressure and quantity of lubricating liquid
will vary. Usually 0.45 to 0.90 m
3
/h (2 to 4 gpm) at
0.7 to 0.14 bar (10 to 20 psi) over maximum pump
discharge pressure of clean liquid is required.
For recommended oils for enclosed lineshaft bearing
lubrication under normal operating conditions, please
see tables 5.2.3.1 and 5.2.3.2. If none of the above
oils are available, oil with the following specifications
should be obtained. Turbine type oil with rust and
oxidation inhibitors added, viscosity 30 cSt (mm
2
/sec)
to 37 cSt (mm
2
/sec) at 37.8
C (100 F) with a
minimum viscosity index of 90.
In the case of product-lubricated
bearings, the source of product supply should be
checked against the order. There may be
requirements for an external clean supply, particular
supply pressure or the commencement of lubrication
supply before pump startup.
5.8.5 Initial Starting
a) If the discharge line has a valve in it, it should be
partially open for initial starting. The discharge
valve is intended to add sufficient system
resistance to the pump. Failure to maintain pump
flow rates within the limits of the pump and motor
could result in severe damage.
b) Start pre-lubrication liquid flow on pump if
required.
c) Start flushing of mechanical seal through external
sources, if required.
d) Start the pump and observe the operation. If
there is any difficulty, excess noise or vibration,
stop the pump immediately and refer to the
Trouble Shooting Chart (section 7.0) to determine
the probable cause.
Observe extreme caution
when venting and or draining hazardous liquids.
Wear protective clothing in the presence of caustic,
corrosive, volatile, flammable or hot liquids. Do not
breath toxic vapors. Do not allow sparking, flames or
hot surfaces in the vicinity of the equipment.
Ensure that the unit is vented of all trapped vapor
Open the discharge valve as desired to operate
the unit at its design conditions
Check complete pump and driver for leaks, loose
connections, or improper operation
If possible, the pump should be left running for
approximately one half hour on the initial startup, this
will allow the bearings, packing or seals, and other
parts to "run-in" and reduce the possibility of trouble
on future starts.
If abrasives or debris are present,
upon startup, the pump should be allowed to run until
the pumpage is clean. Stopping the pump when
handling large amounts of abrasives (as is
sometimes present on initial starting) may lock the
pump and cause more damage than the pump is
allowed to continue operation.
Every effort should be made to keep abrasives out of
lines, sump, etc. so that abrasives will not enter the
pump.
In the case of product lubricated
bearings the source of product supply should be
checked against the order. There may be
requirements for an external clean supply, particular
supply pressure or the commencement of lubrication
supply before pump startup.
5.8.6 Frequency of lubrication
The characteristics of the installation and severity of
service will determine the frequency of lubrication.
Lubricant and pump/motor bearing temperature
analysis is useful in optimizing lubricant change
intervals.