Preconditions at the installation site, Survey of well, Crooked well – Flowserve Byron Jackson Type M User Manual
Page 16: Development of the well, Suction and submergence requirements, Effect of pumping sand, Effect of air or gas
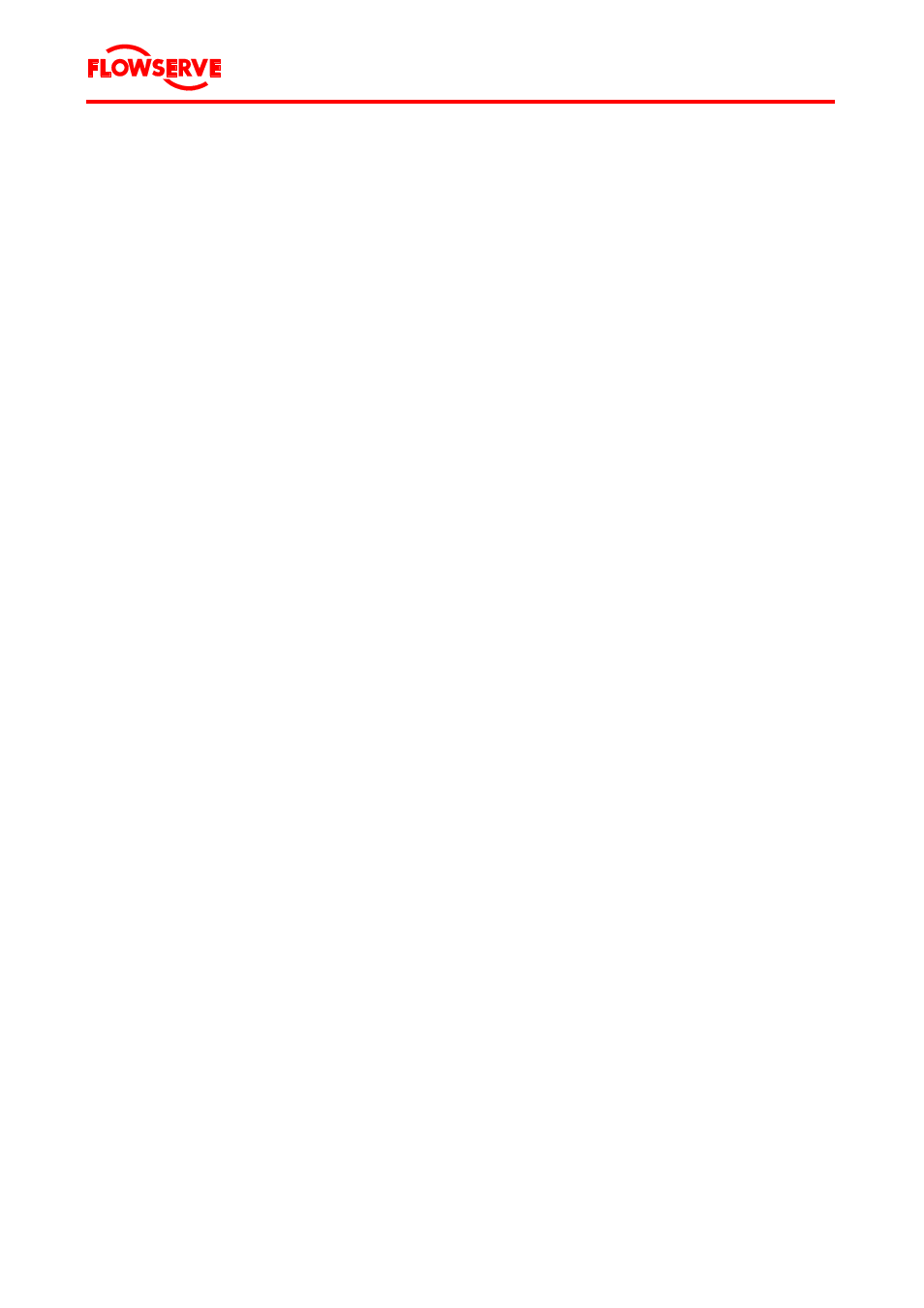
Byron Jackson Double Mechanical Seal Submersible Pumping Unit • 1042.293/9 • June
04
Page 16 of 68
3.4 Preconditions at the installation
site
3.4.1 Survey
of
well
Always sound the well to make sure it is deep
enough to permit installation of the pumping unit
consisting of pump bowl assembly and motor. If
the exact diameter and depth of the well casing is
not known, "cage" the well following the procedure
outlined in Chapter 3.4.2 "Crooked well", Page 16.
Experience indicates that many wells have more
that one string of casing installed and frequently
the lower sections are smaller in diameter than the
surface casing. Be certain the submersible pump-
ing unit will pass into the well freely and hang well
above of the well bottom.
3.4.2 Crooked
well
A well that is known to be crooked and that has not
previously accommodated a pumping unit of com-
parable size must be "caged" before the submersi-
ble pumping unit is installed.
1. Prepare a cage of the same length and di-
ameter as the combined motor and pump
bowl assembly, with 12 m to 15 m (40 feet to
50 feet) of the proper size of riser pipe.
2. Lower the cage into the well to the point at
which the pumping unit is to be placed.
3. If the cage can be lowered to this point with-
out touching the inner wall of the well, the
submersible pumping unit can be installed.
3.4.3
Development of the well
Do not use a new pumping unit to develop the well.
Developing, surging and freeing the well of sand
are considered a part of the well drillers contract
and should be accomplished by the use of a test
pumping unit.
3.4.4
Suction and submergence require-
ments
Pumping the well at a rate at which the pumping
unit breaks suction will cause pump deterioration.
It is suggested that a method be provided for keep-
ing a record of the water level above the suction
inlet.
The minimum submergence recommended is 3 m
(10 feet) of riser pipe submergence below the
maximum well draw-down level, although some
installations may require more submergence.
3.4.5
Effect of pumping sand
Flowserve does not guarantee the pumping unit to
be resistant against the erosive action of sand, silt
or other abrasive materials suspended in water.
Pumping sand will adversely affect the motor be-
cause the vibration produced in a worn pump bowl
assembly will be transmitted to the motor and
could result in a shortened motor life.
3.4.6
Effect of air or gas
The presence of gases in the water may reduce
capacity and head of the pumping unit, thus de-
creasing the hydraulic performance. Further, air or
gas in the water will cause deterioration of materi-
als of the pumping unit sooner than under normal
conditions.
3.4.7
Oxidizing and corrosive effects of
chemicals, air and gases
Even if the composition of the pumped water is
known due to chemical analysis, it is not always
possible to predict the corrosive action of water on
the metals of the pumping unit.
In addition to chemicals, water may also contain
entrained air or gases that have a definite oxidizing
or corrosive action of their own. This action is ac-
centuated by high velocities within the pump.
Such conditions are not recognizable in the chemi-
cal analysis of the water.
Conforming with the Standards of the Hydraulic
Institute of the United States and the practice of all
reliable pump manufacturers, Flowserve does not
guarantee its pumps and motors to be resistant
against corrosive or electrolytic action.
Should you require motors or pumps to perform
under oxidizing or corrosive conditions, contact
Flowserve for further information.