Periodic testing of motor and pump, If pe – Flowserve Byron Jackson Type M User Manual
Page 52
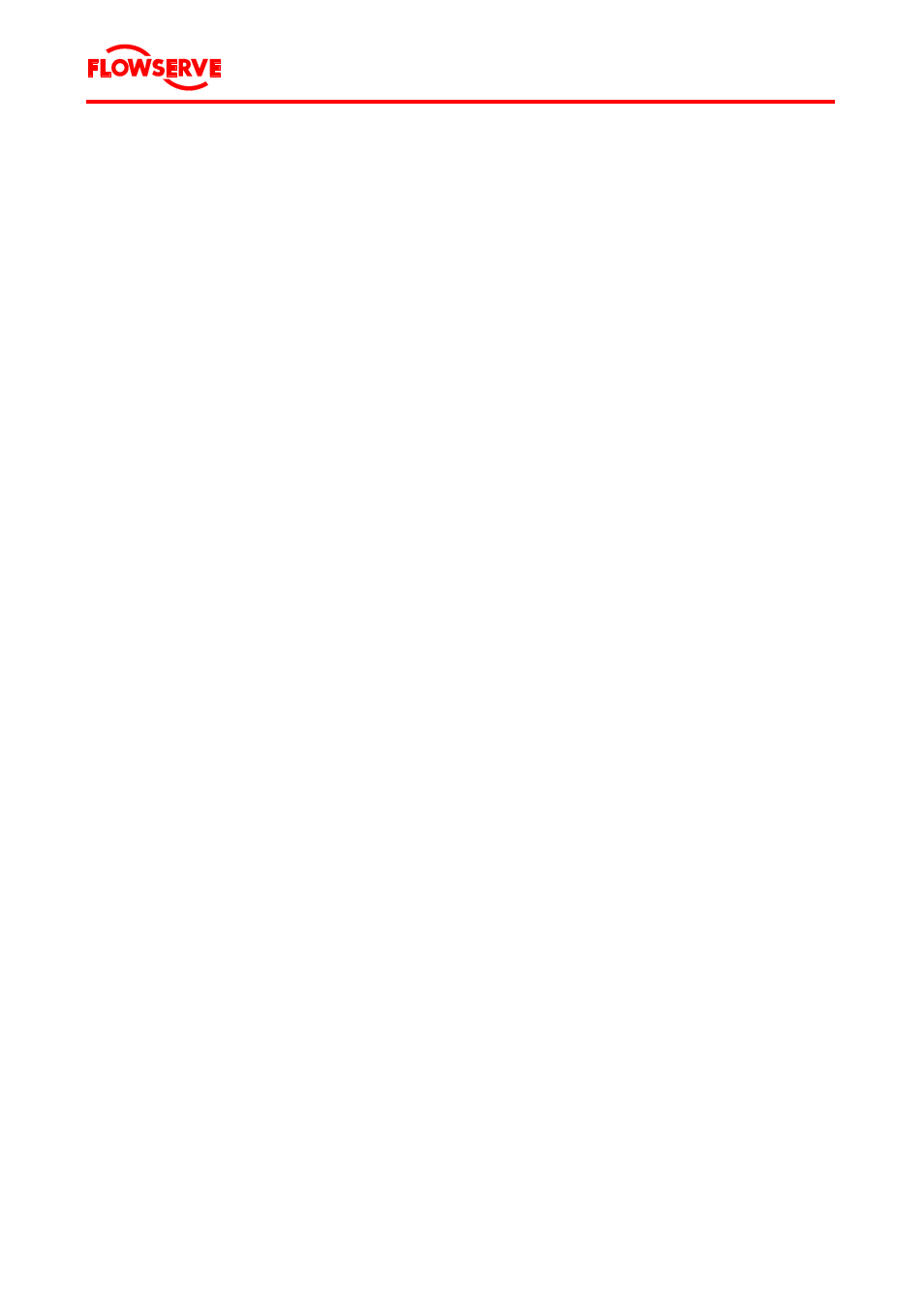
®
Byron Jackson Double Mechanical Seal Submersible Pumping Unit • 1042.293/9 • June
04
Page 52 of 68
6.7 Periodic
testing of motor and
pump
Motivation
As the pump wears, the internal sealing clearances
increase, which results in increased recalculation
flow (or leakage) from the impeller discharge back
to its suction side.
At a fixed differential head, the total flow through
each impeller in a worn pump is the same as in a
new pump, but more of the flow is recirculated flow
that the net flow out of the pump discharge is re-
duced.
To produce the same net flow output as a new
pump, a worn pump must operate at a lower differ-
ential head so that the impellers can operate at a
higher flow rate to make up for the higher recirula-
tion flow. This reduced performance in a worn
pump is the basis for the periodic testing procedure
outlined below.
Scope
Periodic testing or mounting of critical pump bowl
assembly and motor performance parameters such
as head, flow, line voltage, driver current, starting
time, etc., is recommended to establish a reliable
performance record for use in evaluating and pro-
jecting the pumping unit's condition and in estab-
lishing the maintenance requirements for its par-
ticular application. Periodic testing is and important
part of a well-planned maintenance program.
The scope and frequency of periodic testing is pri-
marily a matter of customer decision based on the
severity of pump operating conditions.
A "Periodic Test Record" is provided with each
submersible pump to record the results of periodic
tests.
Operating conditions during test
Periodic test measurements should be taken under
one of the following conditions:
•
Pumping unit operating at a predetermined
test flow.
The test flow used should be the same in
each test and should be greater than 75 % of
the design flow.
•
Pumping unit operating at zero flow (dis-
charge valve closed).
•
Shut-off head reduced by 5 % - 10 %.
CAUTION To prevent possible overheating, do
not run the pump more than
2 minutes against closed valve.
Evaluation
Periodic test data can be used in the following
ways to plan preventative maintenance:
•
Method 1
Plot total differential head measurements at
zero flow and, if practicable, at a fixed test
flow.
Extend (extrapolate) the curve to a future time
when the differential head will be reduced to
an unacceptable value. Plan to pull the pump
before this future time.
•
Method 2
Sometimes, customer flow requirements will
not permit throttling pump flow.
If total differential head and flow can be
measured during normal operation, this data
can be used to plan preventative mainte-
nance. To do so, plot the measured head and
capacity point on the factory pump perform-
ance curve and record the test head as a per-
centage of the performance curve head at the
test capacity. Plot this head versus time, ex-
trapolate and use as in method 1.
•
Method 3
An alternate method would be to plot capacity
(flow rate) as a percentage of performance
curve capacity at test head. Plot this capacity
data versus time, extrapolate and use as head
data used in method 1. Note that in any case,
absolute accuracy of test equipment is not too
important, but repeatability is important to
permit comparison of worn pump performance
with pump performance when new.
Adaptation of maintenance intervals
If direct or projected periodic testing readings show
reduced shut-off head, change maintenance inter-
vals as follows.
•
Shut-off head reduced by < 5 %
No preventative maintenance is indicated.
•
Shut-off head reduced by 5 % - 10 %
Consider and project maintenance to take
place at a time most convenient to the user
providing the fall off in shut-off head would not
exceed 15 % by such time.