Flowserve 3400IQ Digital Positioner User Manual
Page 15
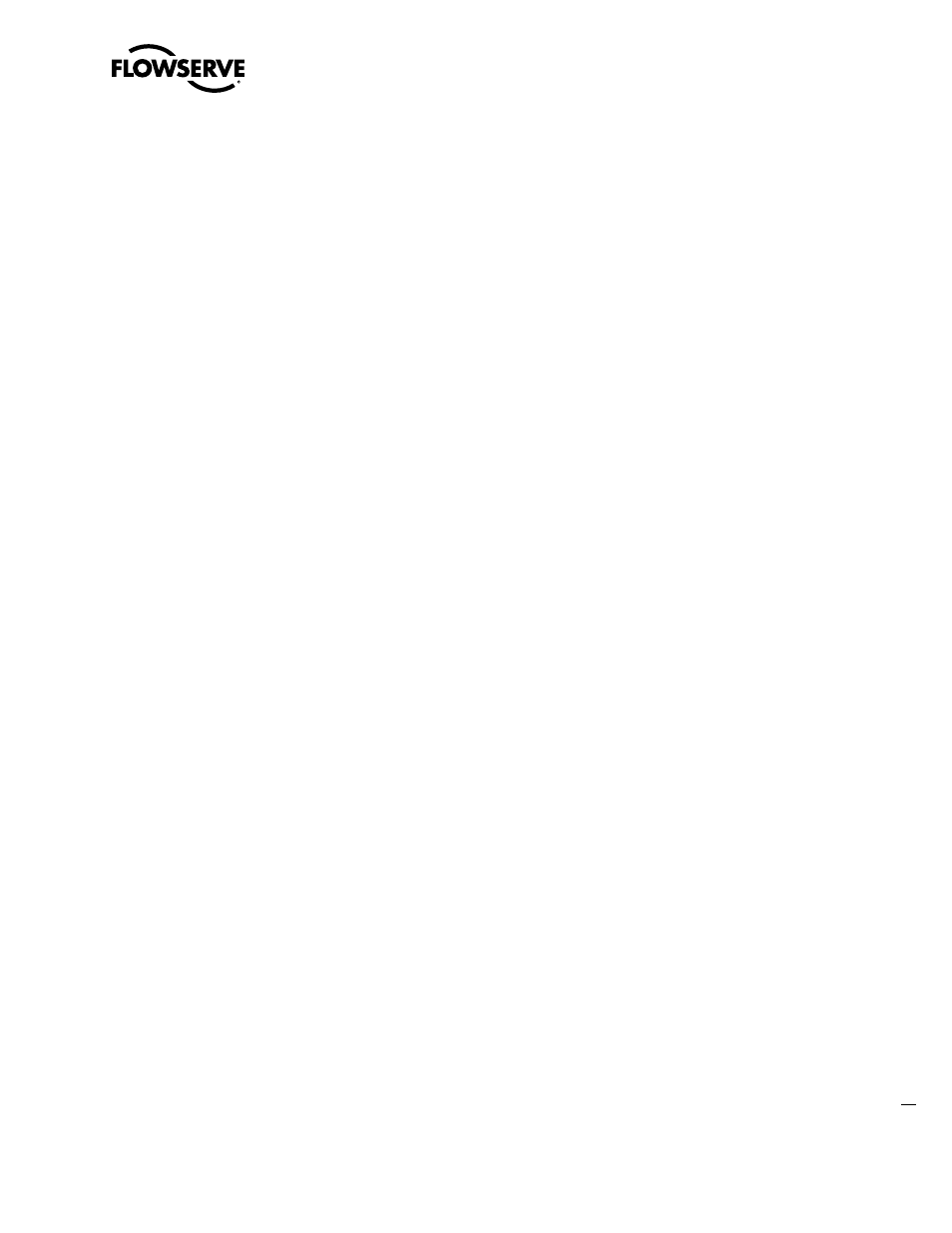
Logix 3400IQ Digital Positioner FCD LGENIM3402-00 – 0/07
flowserve.com
NOTE: Variable names in Figure 1.3 are internal names only and not accessible to the user. They are
for reference use only.
The Logix 3400IQ digital positioner receives power from the two-wire, fieldbus input signal. A digital
signal, sent via fieldbus, is used as the command source. A value of 0 percent is always defined as
the valve closed position and a value of 100 percent is always defined as the valve open position.
Next, the command value is passed through a characterization/limits algorithm block. The positioner
no longer uses cams or other mechanical means to characterize the output of the positioner. This
function is done in software, which allows for in-the-field customer adjustment. The positioner has
two basic modes: linear and custom characterization. In linear mode, the command signal is passed
straight through to the control algorithm in a 1:1 transfer. If custom characterization is enabled, the
command source is mapped to a new output curve via a 21-point, user-defined curve. In addition,
two-user defined features, Soft Limits and MPC (Minimum Position Cutoff; in fieldbus terminology
these are called FINAL_VALUE_CUTOFF_HI and FINAL_VALUE_CUTOFF_LO), may affect the final
command signal. The actual command being used to position the stem is called CMD_USED. The
CMD_USED is the actual positioning command after any characterization or user limits have been
evaluated.
The Logix 3400IQ digital positioner uses a two-stage, stem positioning algorithm. The two stages are
comprised of an inner-loop, spool control and an outer-loop, stem position control. Referring again
to Figure 1.1, a stem position sensor provides a measurement of the stem movement. The control
command is compared against the stem position. If any deviation exists, the control algorithm sends
a signal to the inner-loop control to move the spool, up or down, depending upon the deviation.
The inner-loop then quickly adjusts the spool position. The actuator pressures change and the stem
begins to move. The stem movement reduces the deviation between control command and stem
position. This process continues until the deviation goes to zero. The control algorithm is both
proportional and integral. This algorithm will be further explained later in the document.
A more detailed example to explain the control function follows. Assume the following configuration:
Unit will receive its command from the FBAP
Custom characterization is disabled (therefore characterization is linear)
Soft limits or MPC functions are disabled
Valve has zero deviation with a present input command of 50 percent
Actuator is tubed air-to-open
Given these conditions, 50 percent represents a command of 50 percent. Custom characterization
is disabled so the command is passed 1:1 to the CMD_USED. Since zero deviation exists, the stem
position is also at 50 percent. With the stem at the desired position, the spool valve will be at a posi-
tion in which no air flow is allowed to either side of the actuator. This is commonly called the null or
balanced spool position. Upon a change in the command from 50 percent to 75 percent the posi-
tioner sees this as a command of 75 percent. With linear characterization, the CMD_USED becomes
75 percent. Deviation is the difference between control command and stem position: Deviation =
75 percent - 50 percent= +25 percent, where 50 percent is the present stem position. With positive
deviation, the control algorithm sends a signal to move the spool up from its present position. As
the spool moves up, the supply air is applied to the bottom of the actuator and air is exhausted from
the top of the actuator. This new pressure differential causes the stem to start moving towards the
desired position of 75 percent. As the stem moves, the deviation begins to decrease. The control
algorithm begins to reduce the spool opening. This process continues until the deviation goes to
zero. At this point, the spool will be back in its null or balanced position. Stem movement will stop.
Desired stem position has now been achieved.
•
•
•
•
•