Flowserve 3400IQ Digital Positioner User Manual
Page 33
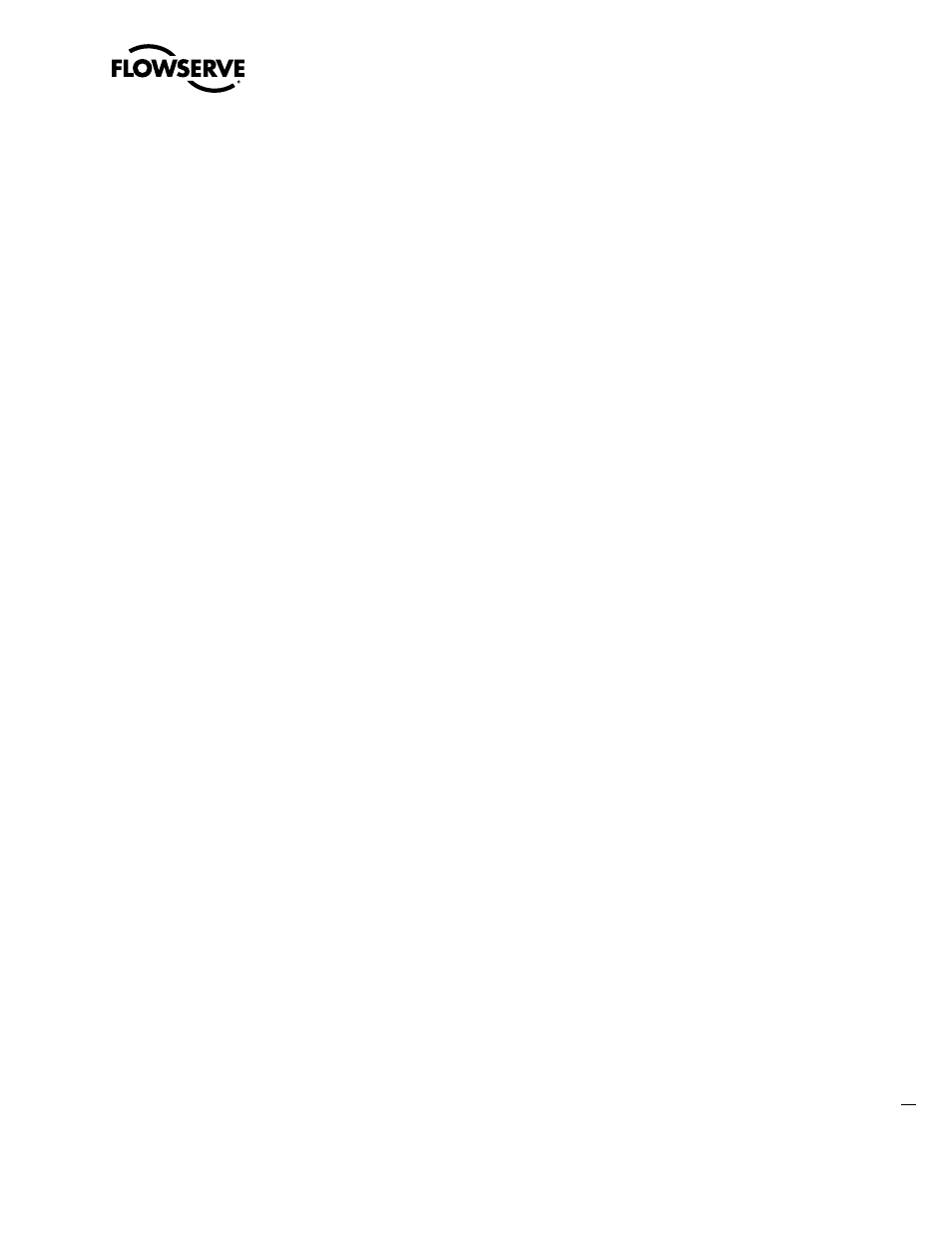
33
Logix 3400IQ Digital Positioner FCD LGENIM3402-00 – 0/07
flowserve.com
Linear vs. Rotary The positioner has two configuration settings: Linear and Rotary. In order to
get better resolution, stem position sensor gains are adjusted based on the angle of rotation of the
linkage. The linear setting allows for linkage rotation up to 65°. The rotary setting allows for linkage
rotation up to 95°. These settings only determine the angle of sensor rotation and do not affect
control parameters. If a positioner is set to linear linkage and a red LED blinks after calibration, the
most common cause is that the sensor movement was greater than 65°. This can occur if the roller
pin was placed in the wrong hole on the follower arm or the stem clamp is placed too high. The
take-off arm should always be level with the stem clamp on linear mountings.
The Logix 3400IQ positioner has an electrical measurement range of 130°. That is, the electronics
will sense stem position over a 130° range of travel of the follower arm. On a rotary valve, the typical
rotation is 90°. When installing a Logix 3400IQ positioner on a rotary valve, the 90° valve rotation
must be centered within the 130° electrical range. If mechanical movement falls outside the electrical
measurement range, the positioner can have a dead band at one end of travel in which valve move-
ment cannot be sensed.
Question: How do I know if the rotary linkage is centered within the 130° electrical range?
Answer: The slot in the take-off arm has enough clearance around the roller pin to move the follower
arm slightly. Move the valve to the fully closed position. At this position, move the follower arm within
the slot clearance. If the valve does not respond to the movement; linkage adjustment is necessary.
Repeat this test at the fully open position.
To adjust the stem position linkage, use the A/D feedback variable viewed using AD_RAW_FB param-
eter. Set TEST_MODE bit ‘Enable diagnostic Variable access.’ With the valve in its mechanical fail
position (i.e. no pressure applied), slightly move the follower arm while watching the A/D feedback. If
the number does not change, the arm is not centered in the electrical range. (The number will bounce
one or two counts due to noise at a fixed position and should not be considered a change, it should
move greater than 10 to 20 counts if the linkage is centered correctly). Rotate the take-off arm, if
necessary, to bring the linkage in range. This procedure is only necessary on a rotary mounting. For
Linear mountings, the red LED will blink if 65° travel is exceeded. Refer to the Calibration section for
further information on stroke calibration errors.
Default Configuration
An FBAP containing default configuration parameters is resident in the firmware of the device and is
loaded on power-up. By using the NI-FBUS Configurator (or other fieldbus configuration) application,
the user can create or make changes to a FBAP for the device’s process application.
Device Configuration
Configuring the Logix 3400IQ digital positioner results in:
Function blocks that execute according to a user-defined schedule
Measurements that are processed according to various user-configured parameters found within
function blocks
An output published on the fieldbus network according to a user-defined publishing schedule.
Device Configuration Example
A sample printout of a typical device configuration for the Logix 3400IQ digital positioner is given in
Appendix A, Sample Configuration Record.
LAS Capability
The Logix 3400IQ digital positioner is capable of operating as the Link Active Scheduler (LAS). The
LAS is a fieldbus device which controls traffic on the network, such as controlling token-rotation and
coordinating data publishing. This fieldbus function is active in only one device at any given time on
a network. Devices which can be designated as the LAS may be an operator station or a field device.
•
•
•