35 operation, Operation – Nortec GS Series User Manual
Page 38
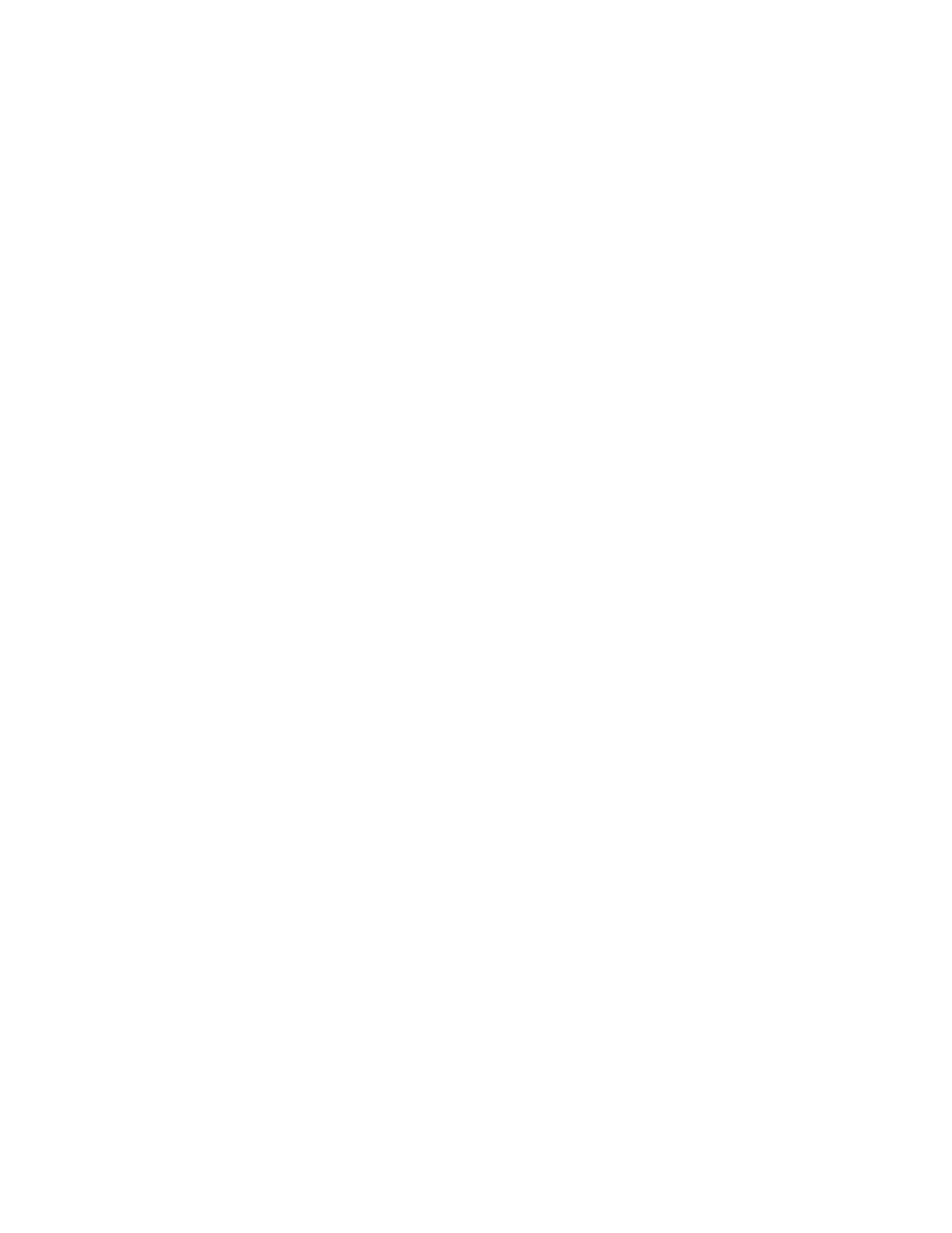
35 | GS Series Installation
Operation
Combustion
The combustion system is based on a fully modulating forced draft combustion air blower(s), a negative
pressure regulated gas valve, and a 100% premix burner. On a call for humidity, the combustion air
blower(s) starts and creates a negative pressure(s) across an orifice located at the air inlet. The blower is
energized to purge the system, and then the hot surface igniter is activated. During this time the electronic
ignition module does a diagnostic check of safety systems including the air proving switch which senses the
negative pressure at the air inlet orifice. After the function of the safety systems has been verified, the gas
valve(s) will open and the gas/air mixture is ignited by the hot surface igniter. If a flame is sensed by the
flame sensor, the gas valve(s) remains open and combustion continues. If a flame is not sensed, the above
sequence is repeated to a maximum of three times after which the ignition module will lock out. The gas
valve(s) maintains a constant ratio air to gas independent of blower speed or external conditions. This air
and fuel is thoroughly mixed in the blower(s) and then forced through the burner ports where ignition occurs.
Hot products of combustion are forced through a baffle inside the heat exchanger and then vented outside.
The heat exchanger has a large flat surface to minimize scale build-up and promote scale shedding to the
bottom of the tank. This self-cleaning action helps to maintain the efficiency of the heat exchanger while the
smooth surfaces allow for easy cleaning when necessary. The heat exchanger has been heat treated to
protect against possible stress-corrosion cracking.
The GS 100 has a single removable combustion chamber/heat exchanger. The combustion system is
duplicated on larger units with multiple chambers inside a common tank.
Water Management
The GS Series of humidifiers is equipped with a unique float chamber water level monitoring device. Two
magnetic floats (one is a backup) measure 5 different water levels in the humidifier for proper operation. The
float chamber and board are located away from the boiling action to increase reading accuracy and reduce
mineral build-up since it is not in the boiling water. The float chamber is connected to the tank under the
water level and above the water level to ensure equalization of pressure between the tank and float
chamber. In addition, cooling water is introduced in the float chamber to reduce scale build-up. The unit also
includes an internal 1” air gap and a vacuum breaker to prevent siphoning effect.
On initial start-up, the solenoid operated fill valve fills the tank. The water level reaches the backup float first
and then the main float. If the backup and main floats do not read the same water level during the
operation of the unit, the unit will shut down on a fault. The unit will continue to fill the unit to the top green
position. The drain pump will then be energized to drain the water level down to just below the bottom red
position and then the fill valve will energize again to fill the unit to the middle yellow position. During this
time the software is performing a test on the fill valve and drain pump.
If a demand signal is present, the unit will then begin the combustion sequence. As the unit operates, the fill
valve with be pulsed to maintain the water level between the yellow and green positions. During steam
production the unit will also check if the floats and drain pump are operational by activating a drain
sequence every 24 hours (adjustable to time of day).