Worcester controls – Flowserve I90 Series User Manual
Page 8
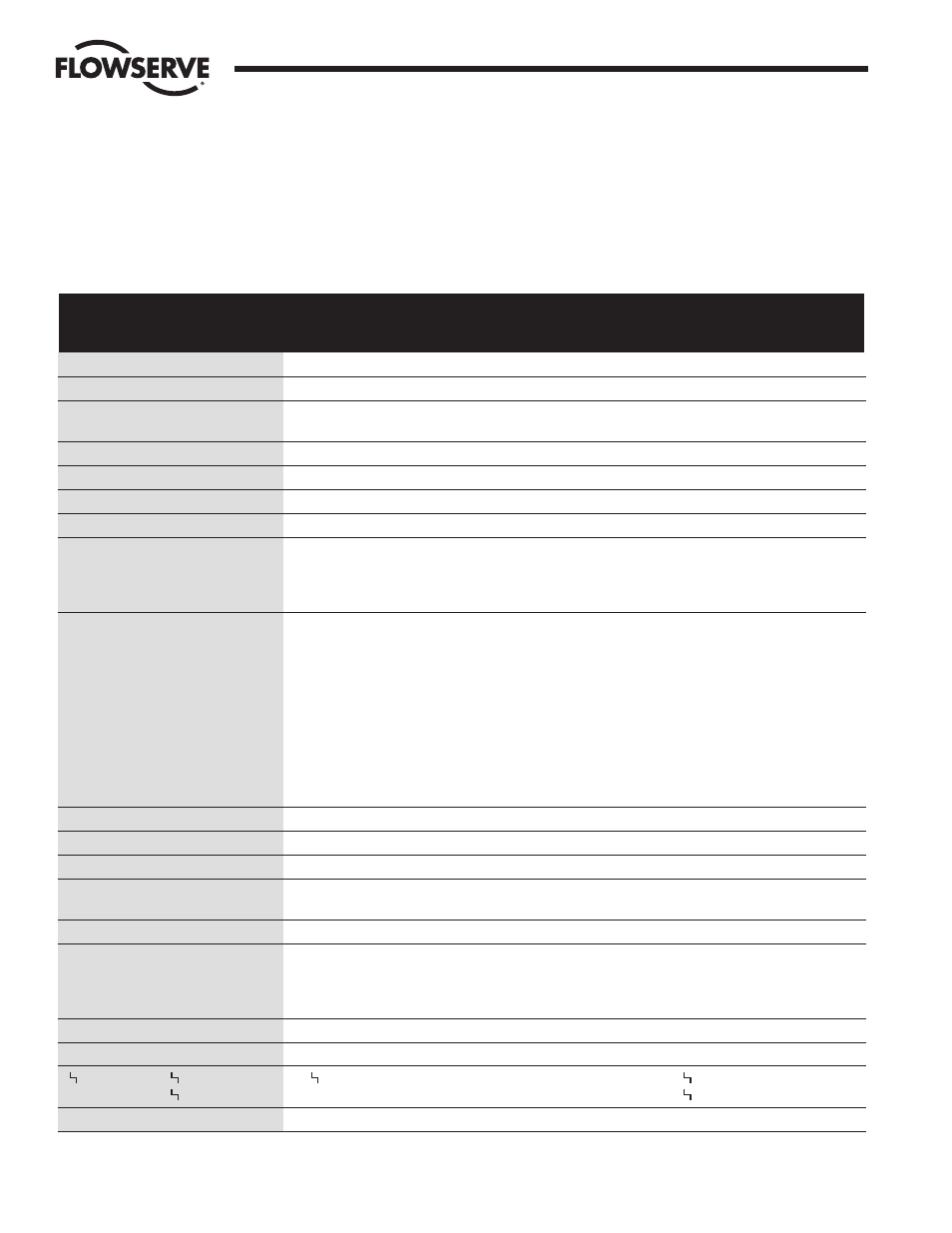
8
Pulsair Loop-Powered Positioner Modular Accessory System (Series I90/L90)
WCAIM2053
The Pulsair Loop-Powered Positioner M.A.S. as provided
by Flowserve accepts a 4-20 mA position input control
signal and uses a 5000 ohm feedback potentiometer (“A”
pot, if dual pot is installed). The 4-20 milliamp signal
also supplies all the power that the circuit and solenoid
valves require to operate — no additional power is
required. A minimum of 3.6 milliamps is needed to keep
the circuitry operating.
b. Controls
Each version of the positioner board is calibrated and
controlled by a set of three push buttons. These buttons, in
conjunction with a system of programming menus, allow
the user to calibrate, adjust and operate all features of the
positioner. An LCD display provides feedback to the user
about the menu selections and settings. The configuration
table below lists the available functions and settings.
Flow Control Division
Worcester Controls
Display
Configuring Settings/
Default
Position
Value
Setting*
Resolution
Meaning
YFct
Lin, nLin
nLin
—
Position feedback function
• Linear/non-linear
init
no/oCay, Strt
no
—
Self-Calibration
SCUr
0 MA, 4 MA
4 MA
—
Setpoint current range
• 0 to 20 mA
• 4 to 20 mA
Sdir
riSE, FALL
riSE
—
Setpoint direction
SPrA
0.0 to 100.0
0.0
0.1 %
Setpoint split range
• Start
SPrE
0.0 to 100.0
100.0
0.1 %
Setpoint split range
• End
tS
Auto, 0 to 40
0
1 s
Setpoint ramp
SFct
Lin
Lin
—
Setpoint function
• Linear
1 : 25
• equal percentage 1:25
1 : 50
• equal percentage 1:50
FrEE
• freely adjustable
SL 0
0.0
0.1 %
Setpoint vertices for freely
0 %
SL 1
28.5
adjustable setpoint function
10 %
SL 2
50.0
20 %
SL 3
62.6
30 %
SL 4
71.5
40 %
Vertices Displayed only
SL 5
0.0 to 100.0
78.5
50 %
when SFct = FrEE
SL 6
84.1
60 %
SL 7
88.9
70 %
SL 8
93.1
80 %
SL 9
96.7
90 %
SL 10
100.0
100 %
dEbA
AUto, 0.1 to 10.0
AUto
0.1 %
Positioner dead band
Ydir
riSE, FALL
riSE
—
Direction of action of manipulated variable
YnrM
MPoS, FLoW
MPoS
—
Manipulated variable standardization, mechanical travel, flow
YA
0.0 to 100.0
0.0
0.1 %
Manipulated variable limit
• Start
YE
0.0 to 100.0
100.0
0.1 %
• End
YCLS
YES, no
no
0.1 %
Tight shutoff of valve
AFct
oFF
oFF
—
Alarms function
• not present
Mi : MA
—
• A1 Min, A2 Max
Mi : Mi
—
• A1 Min, A2 Min
MA : MA
—
• A1 Max, A2 Max
A1
0.0 to 100.0
10.0
0.1 %
Alarm 1 threshold
A2
0.0 to 100.0
90.0
0.1 %
Alarm 2 threshold
Fct
—
Fault alarm output function
•
.H.C.
•
+ H + C
PrSt
no/oCAY, Strt
no
—
Preset (factory setting)
* Certain default settings must be changed to work with rotary actuators. Example: “YFct” must be set to “Lin.”
See section III.A.7 (OPERATION FUNCTION SETTINGS) for more information.