Worcester controls – Flowserve I90 Series User Manual
Page 9
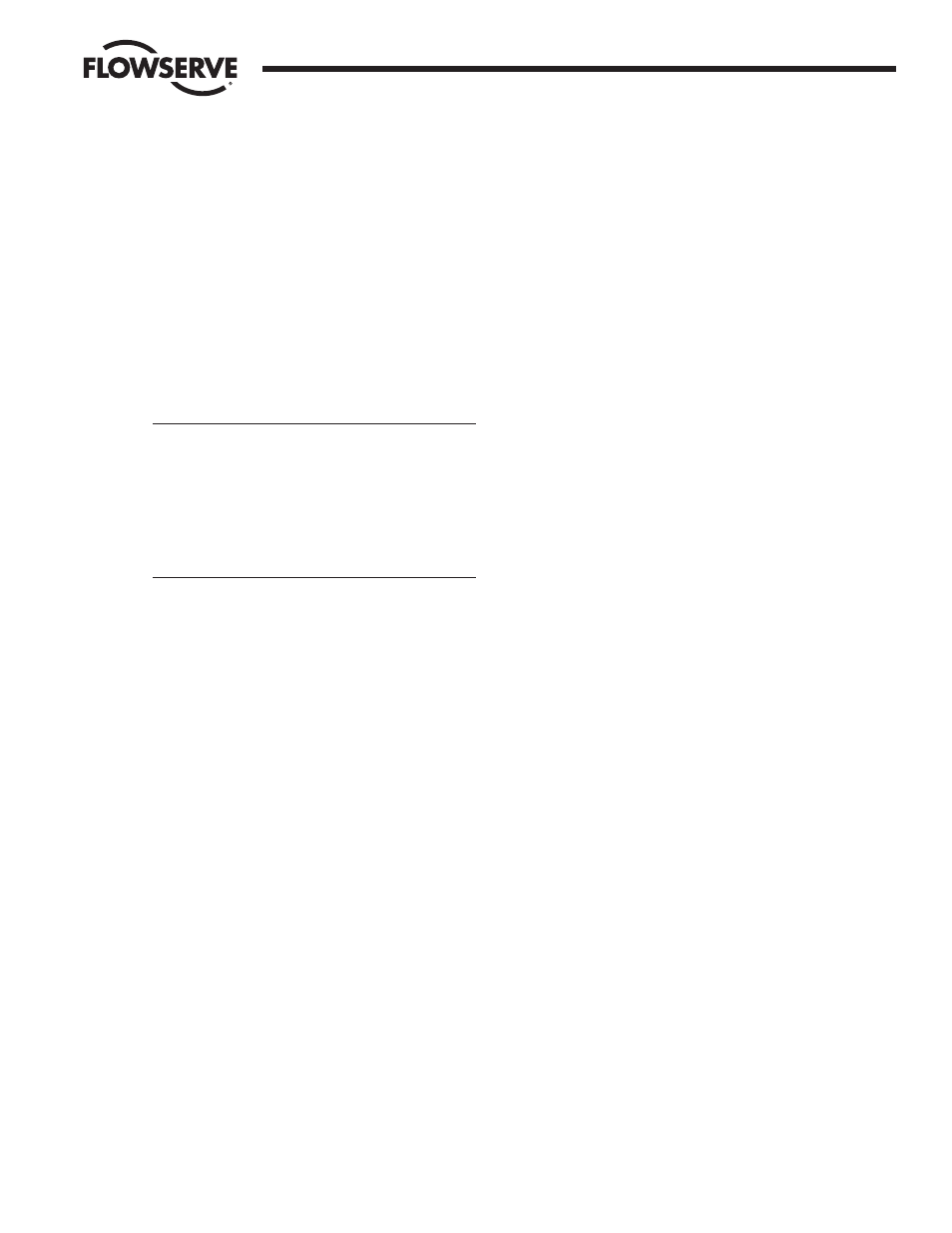
WCAIM2053
Pulsair Loop-Powered Positioner Modular Accessory System (Series I90/L90)
9
4. CALIBRATION
a. Input Signal
The 4 to 20 milliamp input signal is normally calibrated so
that 4 mA equals full closed and 20 mA equals full open.
b. Power Supply
The loop-powered positioner board is powered strictly
from the 4-20 mA input signal. It is therefore necessary
to keep the input current above 3.6 mA to maintain the
power supply to the circuit and allow the digital display to
operate. The calibration parameters are stored in memory
— if power does fail, recalibration will not be required.
c. Self-Calibration Procedure (Refer to Self-Calibration
Flowchart on page 10).
WARNING: DURING SELF-CALIBRATION, ACTUATOR
ADJUSTMENTS OCCUR AUTOMATICALLY.
ADJUSTMENTS MAY ALSO BE NECESSARY TO THE
FEEDBACK LOOP. USE CAUTION TO AVOID TOUCHING
MOVING PARTS — THEY MAY MOVE WITHOUT
WARNING. IN EMERGENCIES, THE ACTUATOR MAY BE
STOPPED BY PRESSING THE “FUNCT” BUTTON. THE
ACTUATOR WILL STOP AND THE POSITIONER WILL
ENTER THE “INIT NON MANUAL” MODE.
This positioner has an automatic calibration program built
in. The only adjustment required is an initial setting of the
feedback potentiometer (“A” pot, if dual pot is installed).
The steps necessary to calibrate the unit are as follows:
1. Connect an air supply (60–80 psi nominal) to the
M.A.S. port labeled “E”. Connect the positive side of
the 4-20 mA source to terminal 1 and the negative to
terminal 2 (reference wiring diagram on inside of
cover and on page 12).
2. Turn on the signal source. Adjust the output for at
least 3.6 mA.
3. At this point, there may or may not be numbers
visible in the LCD depending on whether or not the
unit has been calibrated. If the unit has been
calibrated, the display will be blank and the unit is
ready for operation. If the unit needs to be
recalibrated, then refer to the next section titled
“Recalibrating...”. For local operation, see step 10 of
this section. If the unit has not been calibrated, then
the letter “P” followed by a number between 0.0 and
99.9 will appear. This number represents the position
of the feedback potentiometer in percent of rotation.
4. With the actuator in the full clockwise (CW) position,
the display needs to indicate a reading between P6.0
and P7.5. If the display does not indicate this, then
rotate the face gear until the reading falls in the P6.0
to P7.5 range.
NOTE: It is not necessary to loosen or remove face
gear snap ring to rotate gear.
Hold the “UP” button to drive the actuator to its full
counterclockwise (CCW) position. Verify that the
display indicates between P90.0 and P99.0. If it does
not, then it may be necessary to adjust the feedback
potentiometer so that the offset from 0 and 100 is the
same at each end of travel (i.e., closed=6 open=94).
NOTE: In some cases, it may be necessary to hold the
“DOWN” button to drive the actuator to the open
position until the microprocessor determines the
proper direction of rotation in the next step.
5. The feedback potentiometer is now adjusted and the
unit is ready to calibrate. Hold the “DOWN” button
until the reading on the display indicates between
20.0 and 50.0 percent. (This is done so that the
microprocessor can determine the direction of
rotation for loss of air pressure).
6. Hold down the “FUNCT” button for about 5 seconds
until the display changes and begins flashing between
“yFct” and “nLin,” then release the button.
NOTE: If the menu changes (other words or symbols
appear), momentarily pressing the “DOWN” button
will move back through the menu one item each
time the button is pressed until the “yFct” / “nLin”
display appears.
7. Momentarily press the “UP” button. The display
should begin flashing between “init” and “no”.
8. Momentarily press the “FUNCT” button. The display
should flash “no.”
9. Press and hold the “UP” button (“Strt” will appear in
the display) until the display switches to “run1” and
release the button. The unit has now entered the
self-calibration mode. It will take 1–2 minutes to
complete the calibration program (“run 1”, “run 2”,
etc.), depending on actuator size. At the end of the
self-calibration procedure, the display will begin
flashing “oCay.”
NOTE: The self-calibration procedure can hang up
(stall) during “run 2” if the feedback potentiometer is
adjusted too closely to the end of its range. Factory
specifications call for a potentiometer setting of P4.0
to P13.0; Flowserve recommends a setting between
6.0 and 7.5 to assure trouble-free operation.
If the self-calibration procedure stalls during the
“run 2” phase, there is a procedure that can be
followed. When the self-calibration stalls, there will
be a “d” at the left end of the display and a “U” at
the right end. There will be four vertical lines
between the two letters — three short ones, and one
long one. Turn the face gear such that the long line
moves to the center of the display and becomes a
colon (:). This centers the potentiometer.
Momentarily pressing the “UP” button should cause
the self-calibration procedure to proceed. If this
doesn’t work, then manually set the potentiometer
between P6.0 and P7.5 and run the entire calibration
Flow Control Division
Worcester Controls