Automax logix 3200iq digital positioner – Flowserve Logix 3200IQ Digital Positioner User Manual
Page 29
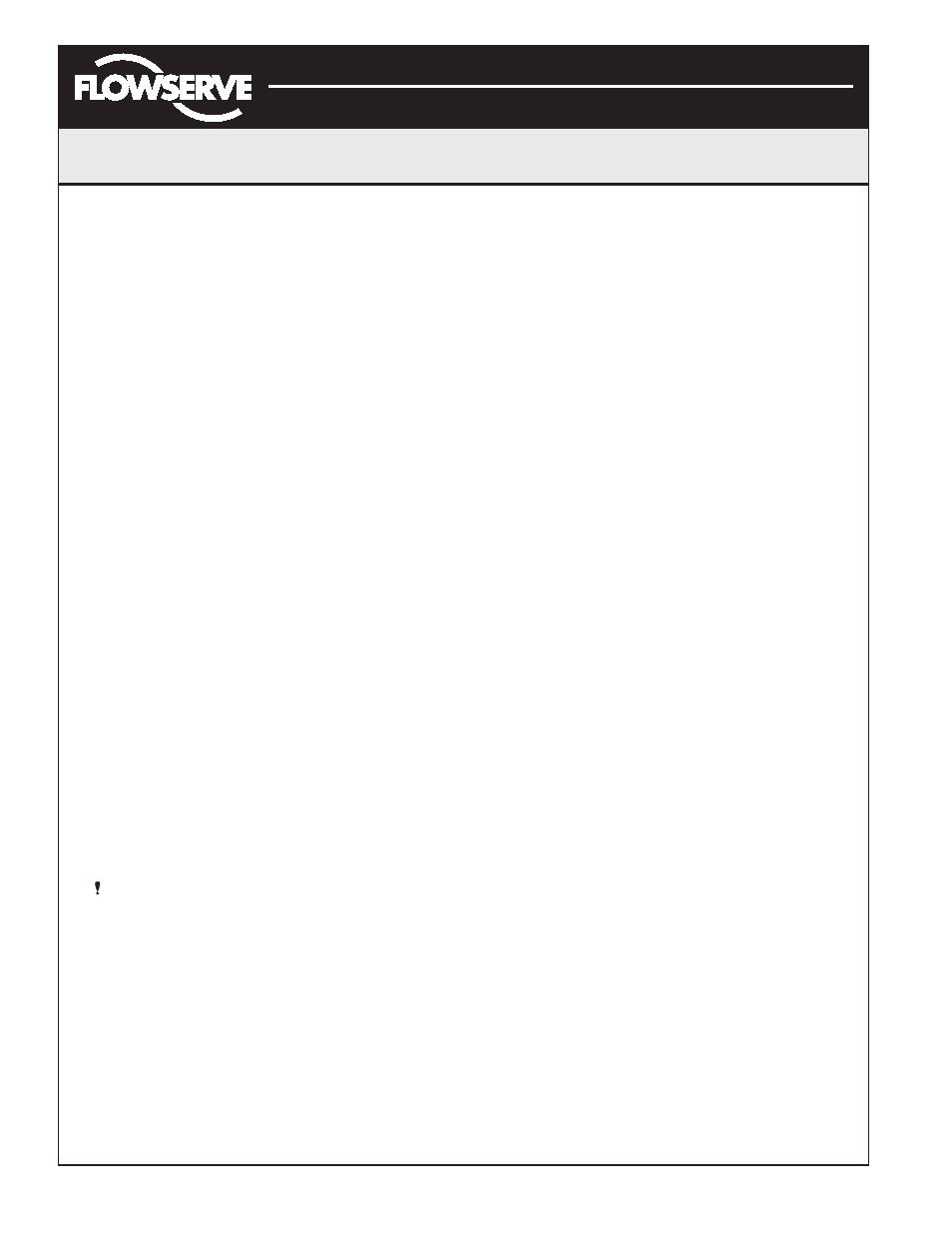
Flowserve Corporation
1350 N. Mountain Springs Parkway
1978 Foreman Dr.
Flow Control Division
Springville, Utah 84663-3004
Cookville, TN 38501
www.flowserve.com
Phone: 801 489 2233
Phone: 931 432 4021
FCD AXAIM3200-00 9/04
Page: 29 of 32
© 2004, Flowserve Corporation, Printed in USA
Automax Logix 3200IQ Digital Positioner
Installation, Operation and Maintenance Instructions
Frequently Asked Questions
Q: My DCS uses 24 VDC, can I run a Logix 3200IQ?
A: A DCS output current card does run from 24 VDC but
the card regulates the actual current output. However,
if the 24 VDC were applied directly across the terminals,
nothing would limit the current and the Logix 3200IQ
Field Termination Board could be damaged. The current
source voltage supply can be anywhere between 10 VDC
to 30 VDC as long as the current is limited in the
4-20 mA range.
Q: I accidentally placed a voltage supply across the
Logix 3200IQ. How do I know if I damaged something?
A: The typical failure in an over-current situation is a short
circuit. Your loop current will be maintained but the Logix
3200IQ control board will receive no power. With power
removed from the Logix 3200IQ, use an ohmmeter to
measure across the terminals. If the reading is a short
(close to zero ohms), the Customer Interface Board must
be replaced. Make sure the positive lead is on the ‘+’
terminal and negative lead is on the ‘-’ terminal when
measuring the resistance.
Q: What is the input resistance of the Logix 3200IQ?
A: The Logix 3200IQ does not have a simple resistive
input. When measuring the voltage across the Logix
3200IQ, it only varies slightly when the current is changed
from 4 mA to 20 mA (9.8 to 10.0 VDC nominal without
HART communications. Add 0.3 V with HART active).
This is because the Logix 3200IQ is an active device.
The resistance at a given current is commonly referred
to as the effective resistance.
Equation 3:
Effective Resistance = (Terminal Voltage)/Current
For example:
at 20 mA: Effective resistance = 9.9 VDC/0.02 A = 495
Ω
The Logix 3200IQ has a specification of 495
Ω
@ 20 mA.
NOTE: You cannot measure across the terminals of an
unpowered Logix 3200 and get the effective
resistance.
Q: How do I know if I need a VHF HART filter?
A: If the current source is interfering with communication,
it will affect both SoftTools and the HART 275/375
handheld. If the positioner communicates to SoftTools or
the HART 275/375 handheld when using a current source
(a 4-20 mA current calibrator, for example) and not the
DCS, it indicates a filter is necessary with that current
source. Some 4-20 mA calibrators that work without a
filter are listed below. If one of these is available, try to
connect with SoftTools or the HART 275/375 handheld
again. If communications are established while using
one of these sources but fails on the original source,
a filter is needed.
Handheld 4-20 mA calibrators which do not require
a filter:
• Altek Model 334
• Rochester Instrument Systems (RIS) CL-4002
• Unomat UPS-II
Q: I set the MPC at 5 percent. How will the positioner
operate?
A: Assume that the present command signal is at
50 percent. If the command signal is decreased, the
positioner will follow the command until it reaches
5 percent. At 5 percent, the spool will be driven fully open
or fully closed, depending on the air action of the valve,
in order to provide full actuator saturation and tight
shutoff. The positioner will maintain full saturation below
5 percent command signal. As the command increases,
the positioner will remain saturated until the command
reaches 6 percent (there is a 1 percent hysteresis value
added by the positioner). At this point, the stem position
will follow the command signal. While in MPC, the Logix
3200IQ LEDs will blink GGGY.
Q: I have MPC set to 3 percent but the valve will not go
below 10 percent.
A: Is a lower soft stop enabled? The lower soft stop must
be less than or equal to zero percent in order for the MPC
to become active. If a positive lower soft stop is written,
this stop will take priority over the MPC feature. When the
lower soft stop is reached, the positioner will blink a
GYYR code.
Q: Will soft stops prevent the valve from going to its
fail position?
A: No.
Q: What is the difference between a model with
Standard diagnostics and a model with Advanced
diagnostics?
A: The model with Advanced diagnostics adds top and
bottom actuator pressure sensors. This allows for more
diagnostic calculations such as loss of pressure, friction,
advanced signatures, and troubleshooting. The pressure
sensors, if present, are also used in the positioner control
algorithm to enhance valve stability.
Q: Can I upgrade from a Standard to an Advanced?
A: Yes. Referencing the IOM, an advanced pressure
sensor board assembly can be purchased. Simply replace
the pressure sensor plug plate with the advanced pressure
sensor board. Using SoftTools or the HART 275/375
handheld, configure the positioner for Advanced
Diagnostics and perform an actuator pressure calibration.