Kemppi Pulse TCS User Manual
Page 13
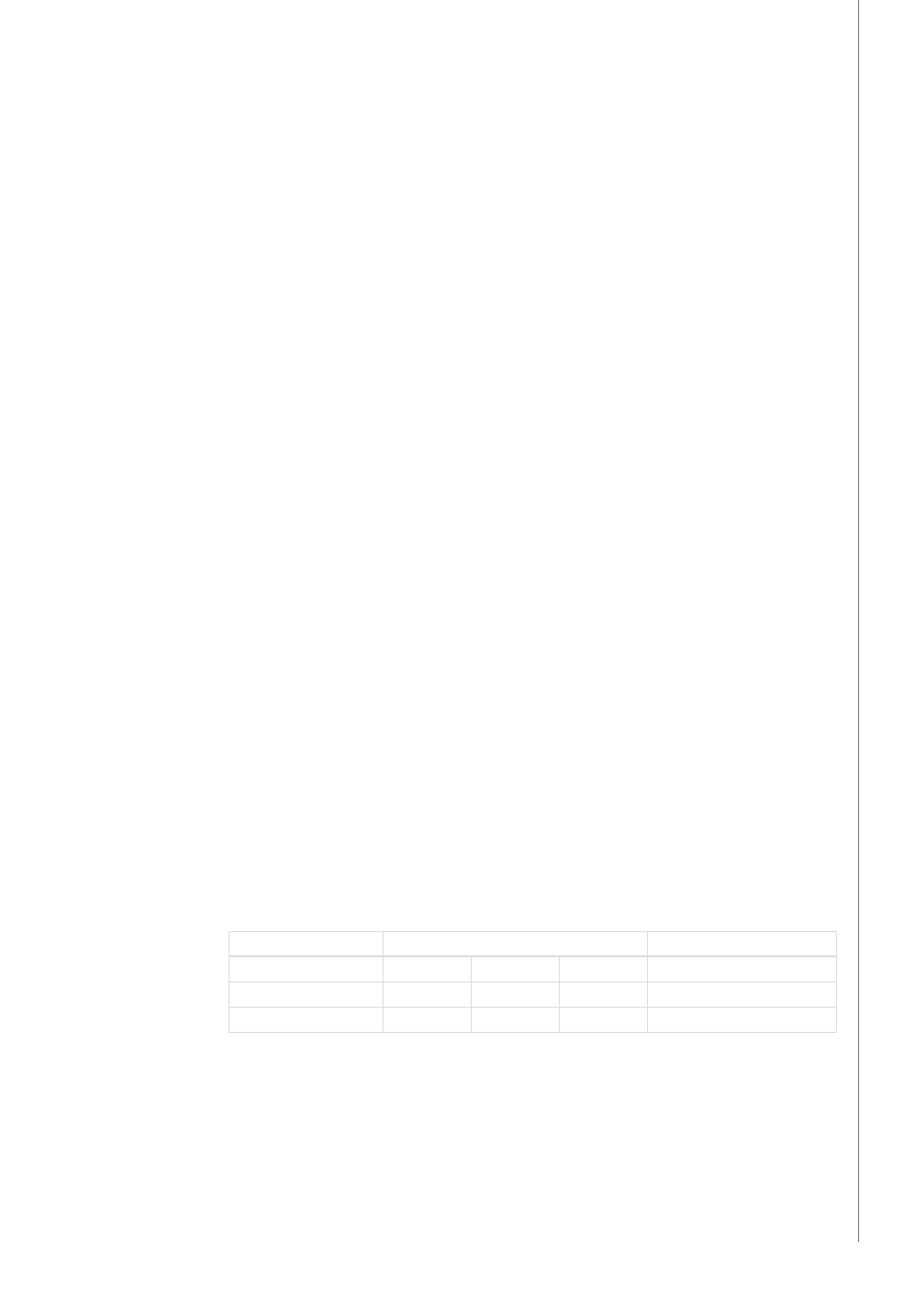
EN
2.12.2 Connecting the control cables
The KempArc Pulse TCS power sources control the behaviour of the wire feeds independently
for each filler wire. This is done through the control cables that run between power sources
and wire feeders.
1.
Connect the control cables to the WIRE FEEDER connection on the back of the KempArc
Pulse TCS control box.
2.
Connect the other end of the cable to the control cable connectors on wire feeders.
2.12.3 Connecting the cooling hoses
The KempArc Pulse TCS system is equipped with KempCool 40 liquid cooling unit. There are
three cooling circuits available: two for each welding gun neck and one for the gas nozzle.
However, not all welding gun brands have liquid cooling in the gas nozzle.
Attach the snap connectors of the cooling hoses to the connectors on the KempCool 40
cooling unit. Blue one for outgoing and red one for incoming cooling liquid.
For more instructions about using the cooling unit, see KempCool 40 operating manual.
NOTE!
There should be two red and two blue hoses in each interconnection cable set, but one pair
of them will remain unused in one of the power sources.
2.12.4 Connecting the shielding gas
Connect the shielding gas hose from the gas supply to the gas snap connectors on the back of
the DT400 and DT400L wire feeders as shown in the picture.
2.13 CONNECTING THE WELDING GUN
The KempArc Pulse TCS delivery package is equipped with a tandem welding gun of the
customer's choice, and with the fixing bracket for fastening the gun to the robot arm.
There are several gun types available, including normal tandem guns and push-pull guns. The
type of tandem welding gun depends on the welding application.
Attach the welding gun to the robot arm and connect the welding gun cables to the Euro
connectors at DT400 and DT400L wire feeders.
2.14 CONNECTING EARTH RETURN CABLES
In KempArc Pulse TCS welding system you have two earth return cables, both of which must
be connected to the work piece.
Kemppi always recommend the use of high quality copper cables with a suitable cross-
sectional area. Cable size should be selected depending on the intended welding application.
However when using pulsed MIG/MAG process or longer cables or higher welding power,
the voltage loss increases, which leads to smaller cross-sectional interconnecting power and
earth return cables will restrict the welding performance of your machine.
• KempArc Pulse TCS: 70 to 95 mm²
The enclosed table shows typical load capacity and voltage loss values of rubber insulated
copper cables, when ambient temperature is 25 °C and the cable temperature is 85 °C.
Cable
Load capacity at duty cycle
Voltage loss / 10 m
100 %
60 %
30 %
70 mm²
355 A
460 A
650 A
0.25 V / 100 A
95 mm²
430 A
560 A
790 A
0.18 V / 100 A
Do not overload welding cables due to voltage losses and heating.
NOTE!
Always check the serviceability of the earth return cable and clamp. Ensure the metal
surface to which the cable is connected is clean from paint and rust. Check the connector to the
power source is fastened correctly.
11
KempA
rc P
ulse
TCS / © Kemppi O
y / 1204