Super Systems CarbCALC II User Manual
Page 6
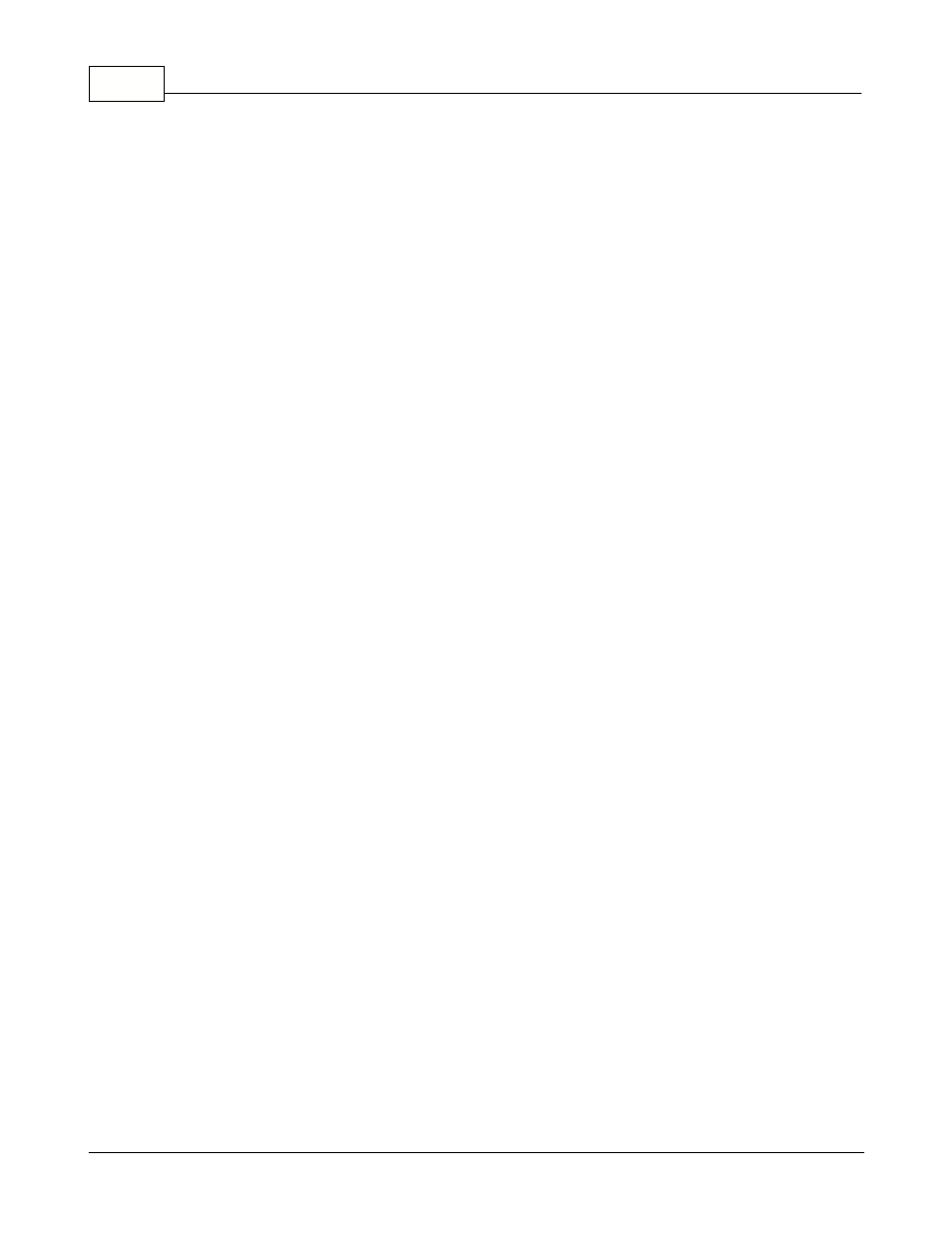
Introduction
CarbCalc II
5
© 2005,2006,2007 Super Systems Inc.
carrier gas similar in composition to Endogas may be produced from methane can be formed from a
nitrogen-methanol blend.
Carburizing Process Variables
The gas carburizing process depends on the control of three principal variables:
·
Temperature
·
Time
·
Atmosphere composition.
Other variables that affect the amount of carbon transferred to parts include the degree of atmosphere
circulation and the alloy content of the parts.
Temperature. The maximum rate at which carbon can be added to steel is limited by the rate of
diffusion of carbon in austenite. This diffusion rate increases greatly with increasing temperature; the
rate of carbon addition at 925°C (1700°F) is about 40% greater than at 870°C (1600°F). The
temperature most commonly used for carburizing is 925°C (1700°F). This temperature permits a
reasonably rapid carburizing rate without excessively rapid deterioration of furnace equipment. The
carburizing temperature is sometimes raised to 955°C (1750°F) or 980°C (1800°F) to shorten the time
of carburizing for parts requiring deep cases. Conversely, shallow case carburizing is frequently done
at lower temperatures because case depth can be controlled more accurately with the slower rate of
carburizing obtained at lower temperatures. For best results, the workload should be heated to the
carburizing temperature in a near-neutral furnace atmosphere. In batch furnaces, parts can be heated
in Endogas until they reach the furnace temperature; then carburizing can commence with the addition
of the enriching gas.
Time. The effect of time and temperature on the Carbon vs Depth profile shows that the carburizing
time decreases with increasing carburizing temperature. In addition to the time at the carburizing
temperature, several hours may be required to bring large work pieces or heavy loads of smaller parts
to operating temperature. For a work piece quenched directly from the carburizing furnace, the cycle
may be lengthened further by allowing time for the work piece to cool from the carburizing temperature
to about 843°C (1550°F) prior to quenching. Similarly, additional diffusion and interchange of carbon
with the atmosphere will occur during cooling prior to quenching.
Carbon Potential. The carbon potential of the furnace atmosphere must be greater than the carbon
potential at the surface of the work piece in order for carburizing to occur. It is the difference in carbon
potential that provides the driving force for carbon transfer into the parts.
Carbon Diffusion. The combined effects of time, temperature, and carbon concentration on the
diffusion of carbon in austenite can be expressed by Fick's laws of diffusion.
Alloy Effects. The various alloying elements found in carburizing steels have an influence on the
activity of carbon dissolved in austenite.
·
Chromium tends to decrease the activity of carbon
·
Nickel tends to raise the activity of carbon
The primary effect of alloys on the diffusion of carbon is their effect on the driving force at the surface
reaction.
The CarbCalcII Model
CARBCALCII is a carbon difussion model for simulation and analysis of gas carburizing process for
low-alloy steels. The interactions of the gas carburizing process cannot be modeled by simple
one-dimensional analysis. In order to accurately predict how a low-alloy steel will react in a controlled
atmosphere process, many factors must be taken into account, including:
·
Alloy steel composition
·
Equilibrium and non-equilibrium gas composition
·
Temperature
·
Atmosphere agitation
·
Surface radius of curvature, concave or convex