3 manufacturer specific parameters, 1 pnu 1000: instrument id, 2 pnu 1001: manufacturer specific error register – BECKHOFF AX2000 PROFIBUS DP communication profile User Manual
Page 24: Error register, Instrument id, Manufacturer specific parameters, Pnu 1000: instrument id, Pnu 1001: manufacturer specific error register, Beckhoff
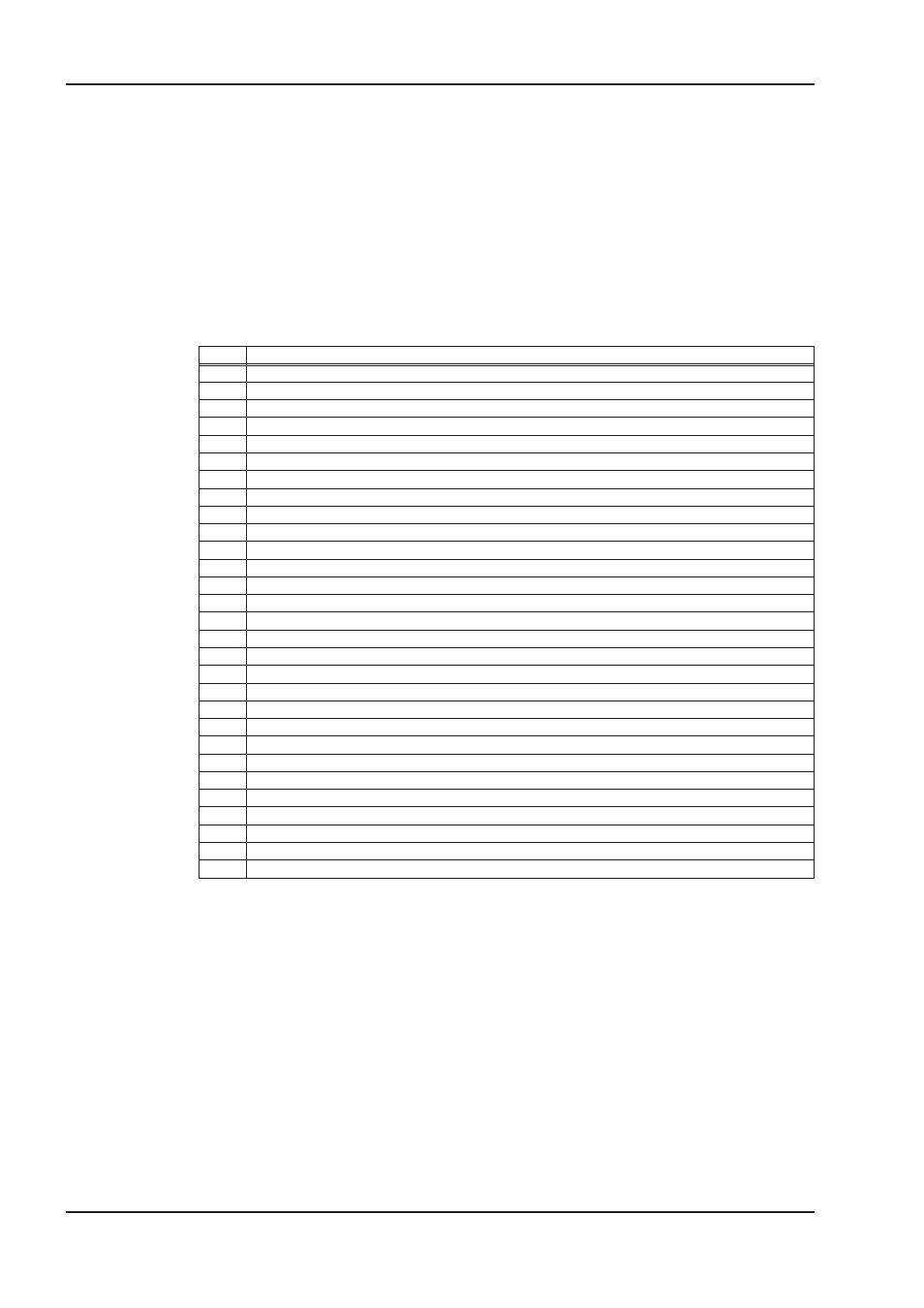
4.2.3
Manufacturer specific parameters
4.2.3.1
PNU 1000: instrument ID
The instrument ID consists of four ASCII characters, with the contents “Sxyz”.
- x
stands for the servoamplifier family
- yz
stands for the current level of the output stage
4.2.3.2
PNU 1001: manufacturer specific error register
The assignment of the error register can be seen in the following table. The explanation of the indi-
vidual errors can be found in the assembly & installation instructions for the servo amplifier.
Bit
Description
0
Error F01:
Heatsink temperature
1
Error F02:
Overvoltage
2
Error F03:
Following error
3
Error F04*:
Feedback
4
Error F05:
Undervoltage
5
Error F06*:
Motor temperature
6
Error F07*:
Auxiliary voltage
7
Error F08:
Overspeed
8
Error F09*:
EEPROM
9
Error F10*:
Flash-EEPROM
10
Error F11*:
Mechanical holding brake
11
Error F12*:
Motor phase
12
Error F13:
Internal temperature
13
Error F14*:
Output stage
14
Error F15:
I²t max.
15
Error F16:
Mains supply-BTB
16
Error F17*:
A/D-converter
17
Error F18*:
Regen circuit
18
Error F19:
Mains supply phase
19
Error F20*:
Expansion card error
20
Error F21*:
Handling error, plug-in card
21
Error F22:
Earth short
22
Error F23:
CAN-Bus off
23
Error F24:
Warning
24
Error F25:
Commuation error
25
Error F26:
Limit switch
26
Error F27:
AS functionality
27-30 Error F28 - F31*:
reserved
31
Error F32*:
System error
When the cause of the error has been cleared, the error state can be canceled by setting Bit 7 in
the control word (STW).
The error response of the AX2000/2500 to the reset will differ, depending on the error that has
occurred:
For errors that are marked by an asterisk (*), setting the reset bit initiates a cold-start of the ampli-
fier, whereby the PROFIBUS communication to this amplifier will also be interrupted for several
seconds. Depending on the circumstances, this break in communication may have to be separately
handled by the PLC.
For the other errors, the reset leads to a warm start, during which the communication will not be
interrupted.
A description of the individual errors and recommendations for removing them can be found in the
amplifier's installation manual.
24
PROFIBUS for AX2000/2500
Using the parameter channel (PKW)
12/05
BECKHOFF