Flowserve APKD User Manual
Page 19
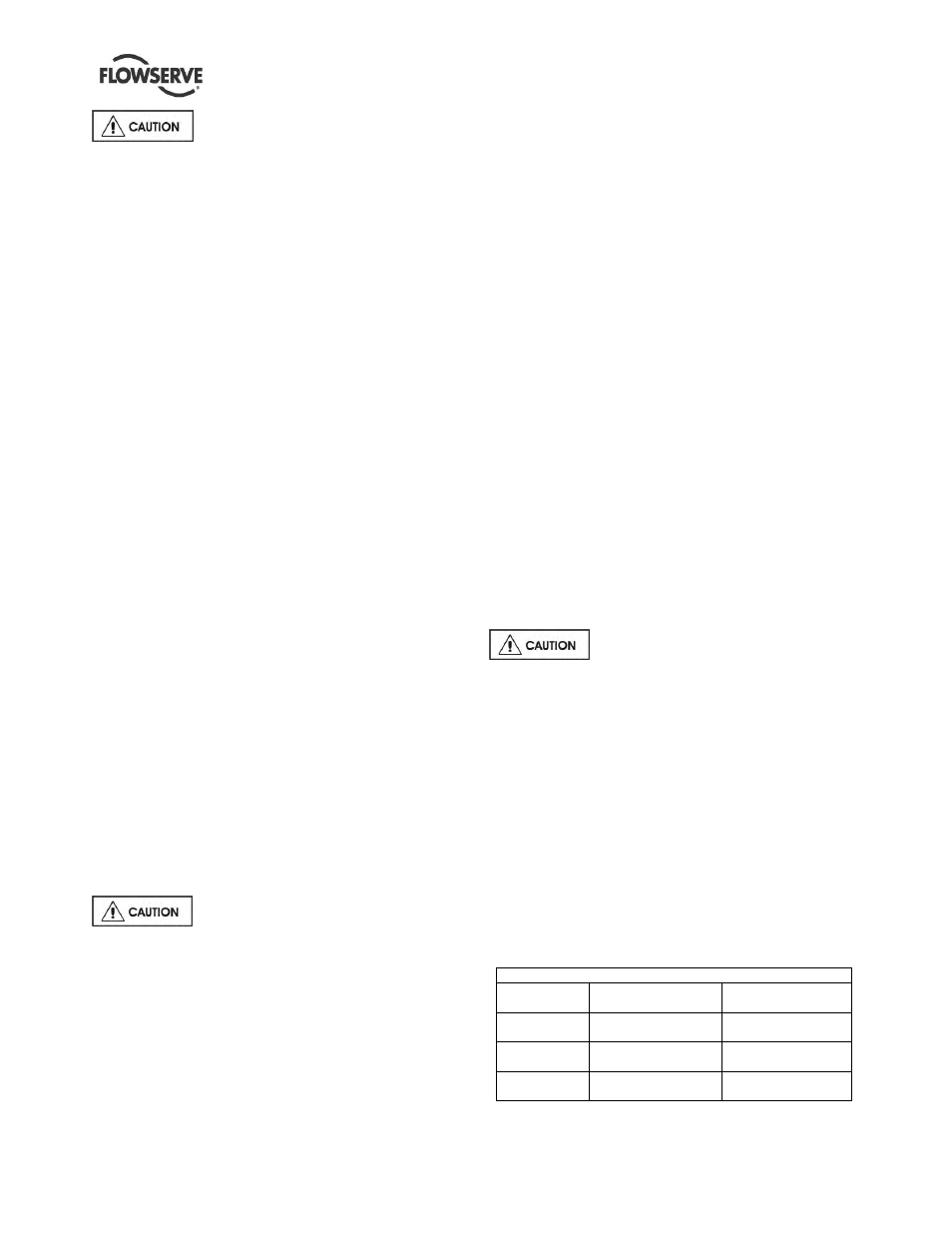
APKD DOUBLE-CASE, DOUBLE-SUCTION USER INSTRUCTIONS 26999903 07-13
Page 19 of 55
flowserve.com
Sump and piping should be
thoroughly cleaned of all loose debris before starting
installation.
Set up installation unit so that the lifting cable will be
centered directly over the well or sump. Carefully lift
the bowl assembly and suction barrel with a clamp.
Lower the bowl assembly into the well or sump. Set
the clamps or holding device that is attached to bowls
on a flat surface. This is to stabilize bowl assembly
and reduce possibility of cross threading the shaft.
a) When installing 152 mm (6 in.) or 203 mm (8 in.)
pump assembly, leave the pump securely
fastened to the wooden skid (as shipped) until the
bowl assembly is raised to a vertical position
b) Lift the pump to a vertical position. If a strainer is
used, attach it to the bowl assembly.
c) Position pump over sump or suction barrel. Align
the discharge of the pump with external piping
then lower onto the base. Level the entire pump.
d) If a mechanical seal is included, install the seal at
this point per the attached instructions.
4.1.4
Installation of pump with the suction
barrel (also referred as ‘can’)
If the pump includes a suction barrel (can), follow the
procedure as listed below. (See lifting instructions in
section 2.3)
a) Install the suction barrel first and grout the
mounting flange and bolts directly to the
foundation.
b) If soleplate is used, mount and grout the
soleplate and mount the suction barrel onto the
soleplate.
c) Level the soleplate & the suction barrel flange as
required.
d) Install the pump.
4.1.5
Installation of couplings on solid shaft
drivers.
Clean threads on pump shaft and on
adjusting nut.
Check
for
burrs and nicks.
All burrs, nicks and rust must be removed from all
mating parts of flanged coupling and pump before
installation. Failure to remove all burrs, nicks and
rust may result in misalignment causing pump to fail.
4.1.5.1
Installation of adjustable flanged
coupling WA.
a) The key [46A] for the driver shaft keyseat should
be a snug or tight fit in the shaft keyseat, and a
sliding fit in the keyseat of the driver half coupling
[42].
b) The key with pin [46] should be a sliding fit in
pump shaft keyseat and a snug or tight fit in pump
half coupling [44] keyseat.
c) Side clearance of keys in keyseats should be
checked with a feeler gauge. This clearance
should not exceed 0.076 mm (0.003 in.) for a
snug fit or 0.127mm (0.005 in) for a sliding fit.
These are maximum allowable clearances. Closer
fits are preferred, if possible. It may be necessary
to file-dress keys to obtain proper fit.
d) Insert the key [46] with pin into pump half of
coupling [44] putting the pin in the hole in keyseat.
The key should not extend below coupling.
e) Lubricate pump coupling half and key assembly
with light oil and slide it onto pump shaft [12A] with
flange up. Slide it past threads.
f)
Lubricate adjusting nut [66A] with light oil and
thread it onto pump shaft [12A] (left hand threads)
with male register down. Thread it on until top of
shaft and top of nut are even.
g) Uncrate and lift driver to allow access to drive
shaft.
The driver must be set on supports
capable of carrying the entire weight of the driver
before proceeding to step (h). Failure of supports
could cause damage to the motor or loss of life.
h) Clean and check driver shaft. Remove any burrs.
i)
Check the fit of the straight key and split thrust
rings [312A] in their respective keyseats. (Refer to
paragraph (a) regarding fit of the straight key).
j)
Install straight key into keyseat. The bottom of the
key must be above the top of circular keyseat for
the split thrust rings.
k) Lubricate driver half coupling lightly and slide it
onto driver shaft. Slide bottom of coupling above
the top of the keyseat for split thrust rings.
l)
Install split thrust rings into circular keyseat and
slide the coupling down over them.
m) Tighten the coupling bolts as follows.
Coupling bolts tightening torques
Coupling
size
Flange diameter
mm (in.)
Torque Nm (In
·lb)
1 & 2
112 & 137
(4.4 & 5.4)
121.5 (1075)
3, 4 & 5
156, 188, & 213
(6.1, 7.4, & 8.4)
237.0 (2100)
6
251
(9.9)
424.0 (3750)